Rexroth: Hydraulics fit for Industry 4.0
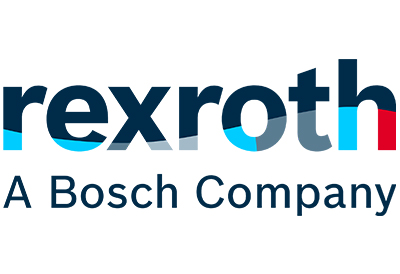
June 27, 2019
The fusion of the physical world of production with the virtual world of information technology into Industry 4.0 is becoming increasingly important. The requirements placed on automation technology have been clearly defined: Decentralized intelligence and autonomous behavior, open communication standards, quick networkability and context integration in real-time. Together with digital control technology and open communication, hydraulics meets these requirements. It also opens the physical advantages of hydraulics, such as high power density, modular design or robustness to networked solutions.
The crucial step for integrating hydraulics into Industry 4.0 has already been taken: connecting hydraulic actuators to digital control electronics to shift functions to software. All of the features of the fluid technology are already stored in the software in the form of algorithms. They automatically offset the non-linearity of this drive technology. Typical controllers such as the transition from path control to force control or for synchronism, e.g., in presses, come pre-programmed. With this decentralized intelligence, the hydraulic drives behave autonomously and adapt to changing process parameters on their own.
One of the foremost driving forces behind this development is Bosch Rexroth. As early as the start of the ’90 s, the drive and control specialist introduced the first electro-hydraulic linear axes with decentralized intelligence to the market.
Software for quick networking
Bosch Rexroth has consistently continued to apply this development, and Rexroth’s decades of practical experience has been incorporated into the software. “We have pre-defined the default hydraulic functions in our best-in-class controllers so the user can configure them directly,” explained Markus Rukaber, Head of Sales-Related Product Management in Machinery Applications and Engineering at Bosch Rexroth, the current state of the art. “This supports the user when starting up hydraulic axes.” This allows hydraulic solutions to be quickly networked and optimally calibrated online to meet individual requirements.
Drives with decentralized intelligence
Variable-speed pump drives open up additional options in the area of decentralized intelligence. They combine the benefits of electrical engineering with hydraulics. The drives in the Sytronix family by Rexroth generate flow as needed and reduce power consumption in the hydraulics compared to conventional solutions by up to 80%. Depending on the application, the Sytronix can take over the positioning of the cylinder directly. This reduces system costs, increases flexibility and simplifies start-up.
Rexroth takes it one step further with self-sustaining linear axes: These ready-made cylinder assemblies come with their own fluid circuit with variable-speed pump. The cylinder generates linear movements without wear and is protected from overloading. Selfsustaining axes are installed like electrical drives. A cable just has to be connected to the power supply and the axis connected to the control system. “These axes have all of the functions of purely electrical drives,” said Rukaber. “They also offer all of the benefits of hydraulics, including wear-free, high power density.”
Basic requirements for open standards
All experts agree Industry 4.0 demands standardized communication protocols and programming languages. The established field bus systems already connect various technologies such as electric drives, hydraulics and pneumatics with the control system. Numerous machine manufacturers have already taken it one step further and switched to real-time Ethernet protocols such as sercos, Ethernet IP and PROFINET.
“Rexroth not only supports bus connection, but also real-time connection to hydraulics through multi-Ethernet interfaces for the variable-speed pump drives and motion controller”, stressed Rukaber. The multi-Ethernet interfaces by Rexroth support all current real-time protocols such as sercos, EtherCAT, Ethernet IP, PROFINET RT, and VARAN on one piece of hardware. Control systems and higher systems thus have total access to the hydraulics and allow system integration regardless of manufacturer.
Open standards also refer to programming. The PLC languages under IEC 61131 have already become standard in machinery and plant engineering. Industry 4.0 requires more. Rexroth has been the first control system manufacturer to bridge the gap between the worlds of automation and IT. The HERMES Award-winning “Open Core Engineerings” interface technology allows Rexroth control systems to be independently programmed in high-level languages. To achieve this, Rexroth revealed the core of its control systems. In initial applications, machine manufacturers completely skipped PLC programming and use smart phones or tablets for start-up, in-service optimizations and diagnostics for their application.
Remote diagnostics and condition monitoring
Connecting hydraulics via Ethernet unlocks all remote diagnostics and remote maintenance options. All control electronics are uniquely identifiable. With the proper authorization, technicians can query data regardless of their physical location or change parameters online.
Decentralized intelligence also opens up the broad field of condition monitoring. The electronics analyze sensor signals and the software determines the current operating status of the hydraulic system. If the measured values exceed defined tolerances, the system warns of reaching critical states. This allows maintenance technicians to take upcoming action in the windows that have already been planned before the machine shuts down.
Drive physics for control systems neutralized
With decentralized intelligence and open standards, the software for hydraulic systems detects changing context and automatically adjusts the motion sequences. Drive physics no longer play a role for the higher control system. It does not matter whether the motion is electrical, electro-mechanical or hydraulic. This means, for example, that hydraulic press stations can read RFID product data and flexibly adjust the press capacity to the individual workpieces without the need for an operator or higher control system to intervene.
With this, hydraulics has matched electromechanics in terms of automation and meets the requirements of Industry 4.0. In addition, it offers unique physical advantages. Rukaber confirms: “Hydraulics integrates perfectly in today’s and tomorrow’s Industry 4.0 concepts when combined with electronics, software and open standards, and brings to the table its unique physical advantages.”