Facts Worth Knowing about AC Drives – Introduction
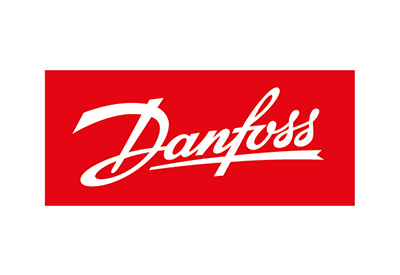
May 5, 2020
Preface
In 1968, Danfoss was the first company in the world to commence mass production of AC drives, for variable speed control of three- phase induction motors.
Today AC drives are an increasingly important component for optimizing motor operation, and the system attached to the motor. AC drives are now used in an expanding range of applications, with the following main objectives in mind:
- – Energy efficiency optimization: Converting from fixed to variable speed in applications with varying load, delivers significant energy In fact, these days, modern motor technology always requires advanced control in order to run optimally at all speeds.
- – Factory automation: Continuously escalating demand for factory throughput leading to a higher degree of automation implies a growing need for variable speed solutions.
- – Process control and optimization: Improved process control often requires variable speed motor control and leads to more precise control, higher throughput, or comfort, depending on the application.
- – Hybridization: Solving issues in power demand in the most cost effective and suitable manner by means of energy storage
The fundamentals of AC drive technology persist, but many elements are also rapidly changing. Increasingly, software is embedded in today’s products, offering new functionalities and enabling the AC drive to play a larger role in the system.
New motor types are appearing, placing additional demands on motor control. This in turn means the AC drive must be able to control an expanding variety of motor types, without burdening the end user with more complexity. In addition, new energy efficiency requirements lead to more variable speed applications, eventually making all motors variable speed and controlled by an AC drive. With this latest update of “Facts worth knowing about AC drives”, we at Danfoss would like to continue the heritage from previous versions of this book. We are proud of what we do and are enthusiastic about AC drives. With this book we hope to convey some of this enthusiasm to you!
If you would like to learn more, please feel free to contact Danfoss.
Jakob Fredsted
Senior Vice President
Danfoss Drives Technology
Content
- 1. Introduction
- 1.1 Terminology
- 1.2 Why use Speed Control?
- 1.3 How to Adjust the Motor Speed
- 1.4 AC Drives
- 1.5 System Optimization
- 2. Electric Motors
- 2.1 Overview
- 2.2 Fundamentals
- 2.2.1 Stator and Rotor
- 2.2.2 Power and Torque
- 2.2.3 AC and DC Motors
- 2.2.4 Electromagnetic Induction
- 2.2.5 Poles, Synchronous Speed and Asynchronous Speed
- 2.2.6 Efficiency and losses
- 2.3 Induction Motors
- 2.3.1 Rotating Field
- 2.3.2 Squirrel-cage Motor
- 2.3.3 Slip, Torque and Speed
- 2.3.4 Typical Operating Conditions
- 2.3.5 Changing Speed
- 2.3.6 Motor Nameplate and Star or Delta Configuration
- 2.4 Synchronous Motors
- 2.4.1 Permanent Magnet (PM) Motors
- 2.4.1.1 Back EMF
- 2.4.1.2 Torque and Speed Range
- 2.4.2 Brushless DC (BLDC) or Electronically Commutated (EC) Motors
- 2.4.3 Line Start PM Motor (LSPM Motor)
- 2.4.4 Reluctance Motors
- 2.4.5 Synchronous Reluctance Motor with Squirrel Cage
- 2.4.6 Synchronous Reluctance Motor (SynRM)
- 2.4.7 Permanent Magnet Assisted Synchronous Reluctance Motor (PMaSynRM)
- 2.4.8 Switched Reluctance Motor (SRM)
- 2.4.1 Permanent Magnet (PM) Motors
- 2.5 Medium Voltage Motors
- 3. AC Drives
- 3.1 Direct Converters
- 3.2 AC Drives with an Intermediate Circuit
- 3.3 Rectifier
- 3.3.1 Uncontrolled Rectifiers
- 3.3.2 Semi-controlled Rectifiers
- 3.3.3 Fully-controlled Rectifiers
- 3.3.4 Active Front-End/Active Infeed
- 3.4 Intermediate Circuit
- 3.4.1 Variable Intermediate Circuit
- 3.4.2 Constant Intermediate Circuit
- 3.4.3 Capacitorless Intermediate Circuit
- 3.4.4 Common DC Bus
- 3.5 Inverter
- 3.6 Modulation Principles
- 3.6.1 Pulse Amplitude Modulation (PAM)
- 3.6.2 Pulse width Modulation (PWM)
- 3.6.3 Asynchronous PWM
- 3.6.3.1 SFAVM
- 3.6.3.2 60° AVM
- 3.7 Control Circuit and Methods
- 3.7.1 Simple Control Method
- 3.7.2 Scalar Control with Compensation
- 3.7.3 Space Vector with and without Feedback
- 3.7.3.1 Space Vector (Open Loop)
- 3.7.3.2 Space Vector (Closed Loop)
- 3.7.4 Open Loop and Closed Flux Vector Control
- 3.7.4.1 Flux Vector (Open Loop)
- 3.7.4.2 Flux Vector (Closed Loop)
- 3.7.5 Servo Drive Control
- 3.7.6 Integrated Motion Controller
- 3.7.7 Control Conclusions
- 3.8 Danfoss Control Principles
- 3.8.1 Danfoss VVC+ Control Principle
- 3.8.1 Danfoss Flux Vector Control Principle
- 3.9 Medium Voltage Drives
- 3.9.1 MV Semiconductors
- 3.9.2 MV Drive Topologies
- 3.10 Standards and Legislation
- 4. Star and Delta Configuration in Field Weakening Operation
- 4.1 Basic Principles
- 4.1.1 U/f Operation and Field Weakening
- 4.1.2 Star and Delta Configuration in Field Weakening Operation
- 4.1.3 Running in Current Limit
- 4.2 Compensations
- 4.2.1 Load-independent Start Compensations
- 4.2.2 Load-dependent Start Compensations
- 4.2.3 Load Compensations
- 4.2.4 Slip Compensations
- 4.2.5 PM Motor and SynRM compensations
- 4.3 Danfoss Automatic Motor Adaption (AMA)
- 4.4 Operation
- 4.4.1 Motor Speed Control
- 4.4.2 Reversing
- 4.4.3 Acceleration and Deceleration Ramps (Ramp Up and Down)
- 4.4.4 Motor Torque Control
- 4.4.5 Watchdog
- 4.4.6 Energy Efifcient Motor Start
- 4.4.7 Energy Efficient Motor Control
- 4.5 Dynamic Brake Operation
- 4.5.1 Extending Deceleration Ramp
- 4.5.2 Motor as a Braking Resistor
- 4.5.3 Brake Chopper Circuit (Brake Module) and Resistor
- 4.5.4 Use of a Regenerative Braking Unit
- 4.6 Static Brake Operation
- 4.6.1 Coasting to Stop
- 4.6.2 DC Braking
- 4.6.3 DC Hold
- 4.6.4 Electromechanical Brake
- 4.7 Motor Heating and Thermal Monitoring
- 4.8 Functional Safety
- 4.1 Basic Principles
- 5. Saving Energy with AC Drives
- 5.1 Potential
- 5.2 Motor + AC Drives Efficiency
- 5.3 Classification of Energy Efficiency Componenets
- 5.4 Load over Time
- 5.4.1 Applications with Variable Torque
- 5.4.2 Applications with Constant Torque
- 5.5 Life Cycle Costs
- 5.6 System Savings
- 5.7 Using Regenerated Power
- 5.8 Hybridization
- 5.8.1 Grid Converter
- 5.8.2 DC/DC Convterter
- 6. Electromagnetic Compatibility
- 6.1 EMI and EMC
- 6.2 EMC and AC Drives
- 6.3 Grounding and Shielding
- 6.4 Installations with AC Drives
- 6.5 Output filters
- 6.5.1 dU/dt filters
- 6.5.2 Shine-wave filter
- 6.5.3 Common-mode Filter
- 6.6 Bearing electric stress
- 6.7 European EMC Directive and EMC Standards
- 7. Protection against Electric Shock and Energy Hazards
- 7.1 General
- 7.2 Mains Supply System
- 7.3 DC Supply Systems
- 7.4 Ground Fault Protection
- 7.5 Fuses and Circuit Breakers
- 7.6 DC Guard for Common DC Bus Systems
- 8. Harmonics
- 8.1 What are Harmonics?
- 8.1.1 Linear Loads
- 8.1.2 Non-linear Loads
- 8.1.3 The Effect of Harmonics in a Power Distribution System
- 8.1.4 The Effects of Harmonics on Motors
- 8.2 Harmonic Limitation Standards and Requirements
- 8.3 Harmonic Reduction Methods in AC Drives
- 8.3.1 Passive Harmonic Mitigation
- 8.3.2 Active Harmonic Mitigation
- 8.4 Harmonic Analysis Tools
- 8.4.1 VLT Motion Control Tool MCT 31
- 8.4.2 Harmonic Calculation Software (HCS)
- 8.1 What are Harmonics?
- 9. Interfaces
- 9.1 Human Machine Interface (HMI)
- 9.2 Operating Principles of Serial Interfaces
- 9.3 Standard Serial Interfaces in AC Drives
- 9.4 Fieldbus Interfaces in AC Drives
- 9.5 Fieldbuses Standardisation
- 9.6 Industrial Ethernet and the Internet of Things
- 10. Sizing and Selection of AC Drives
- 10.1 Get the Drive Rating Right
- 10.2 Rating of the Frequency Converters from Motor Specification
- 10.3 Overload Capacity
- 10.3.1 Energy Efficiency Concerns
- 10.4 Control Range
- 10.5 Heat Losses and Cooling the Drive
- 10.5.1 Air-Cooled Drives
- 10.5.2 Liquid-Cooled Drives
- 10.6 Derating of an AC Drive
- 10.7 Regenerative Energy
- 10.8 Motor Cables
- 10.9 Environment
- 10.10 Centralized versus Decentralized Installation
- 10.11 Examples
1. Introduction
By definition, an AC drive (or drive) is an electronic device that converts alternating current (AC) of a fixed frequency to any frequency. Traditionally, these devices were electro-mechanical machines (motor-generator set). Those are sometimes referred to as “dynamic” drives. With the
invention of solid state electronics, it has become possible to build 100% electronic drives, which are often referred to as “static” drives (no moving parts).
Whilst the principle of converting fixed mains voltage and frequency into variable quantities has always remained virtually the same, there have been many improvements from the first AC
drives, which featured thyristors and analogue technology, to today’s microprocessor-controlled, digital units.
Because of the ever-increasing degree of automation in industry, there is a constant need for more automated control and a steady increase in production speeds, so better methods to further improve the efficiency of production plants are being developed all the time.
Today, the drive-controlled, three-phase motor is a standard element in all automated applications. High-efficiency induction motors, but especially motor designs such as permanent magnet motors, EC motors and synchronous reluctance motors, need regulation with AC drives, many motors cannot even be operated directly from the 3-phase standard power supply.
1.1 Terminology
Different terminologies are used for systems that can control or alter the speed of electrical motors. The most commonly used ones are:
- – AC Drive
- – Frequency Converter (FC)
- – Variable Speed Drive (VSD)
- – Adjustable Speed Drive (ASD)
- – Adjustable Frequency Drive (AFD)
- – Variable Frequency Drive (VFD)
While VSD and ASD refer to speed control in general, AFD, VFD and FC are directly connected to adjusting the feeding frequency of a motor. In this context, AC drive and the abbreviation “drive” are used as well. These two terms will be widely used throughout this book. This wording covers the power electronic part of the devices and the supporting components like current sensors, I/Os and Human Machine Interface (HMI).
1.2 Why Use Speed Control?
There are numerous reasons for adjusting the speed of an application:
- – Save energy and improve efficiency of systems
- – Match the speed of the drive to the process requirements
- – Match the torque or power of a drive to the process requirements
- – I mprove the working environment
- – Reduce mechanical stress on machines
- – Lower noise levels, for example on fans and pumps
Depending on the application one or the other benefit is predominant. However, speed control is proven to bring significant advantages in many different applications.
1.3 How to Adjust the Motor Speed?
There are three main technologies to realize speed control used in industry. Each has its unique features:
Hydraulic
- – Hydro-dynamic type
- – Static types
They are often favored in conveyor applications especially for earth-moving and mining equipment. This is basically due to inherent “soft start” capability of the hydraulic unit.
Mechanical
- – Belt and chain drives (with adjustable diameters).
- – Friction drives (metallic)
- – Variable speed gear
Mechanical solutions are still favored by many engineers – especially mechanical engineers – for some applications, mainly because of their simplicity and low purchase price.
Electrical
- – AC drive with electrical motor
- – Servo systems (for example servo amplifier and servo PM motor)
- – DC motor with control electronics
- – Slip-ring motor (slip control with wound-rotor induction motor)
Historically, electrical devices for speed control were complex to handle and expensive. They were used for the most challenging tasks where no alternatives were available.
The provided list of technical solutions for speed control of motors is not exhaustive and shall give an insight of the possibilities only. This book will focus on speed control of electrical motors by AC drives.
1.4 AC Drives
Modern AC drives can be applied to adjust and maintain the speed or torque of a driven machine with an accuracy of ±0.5%. This is independent of the load when compared to fixed speed operation of the induction motor, where the speed can vary by as much as 3 – 5% (slip) from no-load to full-load operation.
Motor manufacturers employ a variety of concepts to achieve high efficiency in electrical motors. For users it can be difficult to see the main benefit from one technology to another, but the user will surely observe that energy efficient motors need high technology controls.
In principle, nearly all motors can be operated with control algorithms specially adapted to each motor type. Some manufacturers of AC drives relate their design to a narrow group of motor technologies, but many manufacturers have the different algorithms built-in and selectable during commissioning.
For the commissioner it is important that the drive is easy to commission based on the data, which is normally available for the used motor type. After commissioning the user must be confident that the system is really set up as expected, thus online measurements of actual energy consumption and easy access to important data about the operation is essential.
1.5 System Optimization
To ease the selection of components and ensure the various Government aims to reduce energy consumption, there is a big motivation for a complete set of international regulations.
According to the German Association of Electrical and Electronics Manufacturers (ZVEI), approximately 10% of the savings can be achieved by using high-efficiency motors, 30% of the savings are achieved by variable speed, but as much as 60% of the potential savings are achieved by looking at the overall system and optimizing accordingly.
With that in mind, please read all chapters in this book and remember you cannot judge a system by looking at only one or few of the components involved.
We wish you an interesting read.