Yokogawa Releases ProSafe-RS R4.05.00, the Latest Version of a Core Product in the OpreX Control and Safety System Family
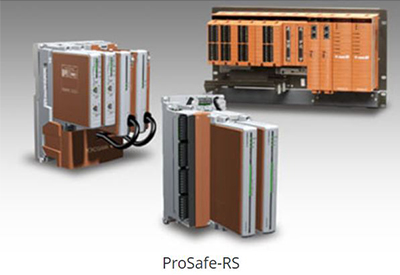
November 13, 2019
Yokogawa Electric Corporation announces the November 15 release of ProSafe-RS R4.05.00, an enhanced version of the ProSafe-RS safety instrumented system. ProSafe-RS is a core product of the OpreX Control and Safety System family.
This latest version of ProSafe-RS has a new processor module with a Yokogawa-developed microprocessor unit (MPU). The use of an MPU of Yokogawa’s own design eliminates the risk of disruptions caused by the modification or discontinuation of commercially available electronic components, ensuring the long-term stable provision of the ProSafe-RS system. This version of ProSafe-RS also features an enhanced function that speeds up system software upgrades and a new function that helps to prevent operator errors. With these enhancements, Yokogawa is helping to ensure safety and sustainable operations over the entire lifecycle of plant operations, from commissioning to end of service.
Development Background
In energy and basic materials industries such as oil, gas, petrochemicals, and chemicals, safety instrumented systems are employed to safely initiate emergency plant shutdowns whenever abnormal conditions are detected, and they operate as part of fire and gas systems that annunciate alarms and initiate appropriate countermeasures if toxic gas, flame, smoke, or heat is detected.
Rapid advances in technology are resulting in ever shorter lifecycles for the electronic components that are used in a wide variety of products and systems. When an electronic component is modified or discontinued, suitable substitutes are not always commercially available. As a result, manufacturers must often make significant modifications to their products and systems. To address such needs and thereby ensure long-term support over the entire plant lifecycle, Yokogawa has developed components of its own design for ProSafe-RS and has added and enhanced functions that help to keep software up to date and improve operability.
Enhancements
-
New S2CP471 processor module with Yokogawa-developed MPU
The safety control station (SCS) is a key component of the ProSafe-RS system, and the processor module is a vital component of the SCS. For this latest version of ProSafe-RS, Yokogawa has developed the S2CP471 processor module. To ensure long-term product lifecycle support (supply chain security) and thereby contribute to the overall stability and continuous of plant operations, Yokogawa has incorporated a new MPU of its own design in the S2CP471 processor module.
-
Ability to upgrade system version while SCS is operating
To ensure safe plant operations, the latest security features and other countermeasures must be implemented in plant system software. Until now, upgrade to the SCS software could normally once every few years because it required a shutdown of related production processes. This new version of ProSafe-RS features an enhanced SCS program upgrade function that is able to perform software updates online, thus allowing the upgrade to a new version without suspending production processes. This allows greater freedom when choosing when to perform system software upgrades. A risk assessment is required before using this new function.
-
Addition of forced I/O viewer to improve visibility and plant awareness
The forcing of I/O and application program variables is usually necessary during plant commissioning and maintenance. Identifying whether specific I/O and program variables are forced has required consultation with safety engineers or the looking up of such information in work shift documentation. To improve efficiency and accuracy, Yokogawa has developed a forced I/O viewer that enables operators to identify at a glance for all SCSs whether an I/O or variable has been forced. This enhances visibility and awareness so that appropriate countermeasures can be taken whenever an unsafe situation occurs.