TapX MTC – ANCA’s Patented Motor Temperature Control (MTC) Technology
December 18, 2024
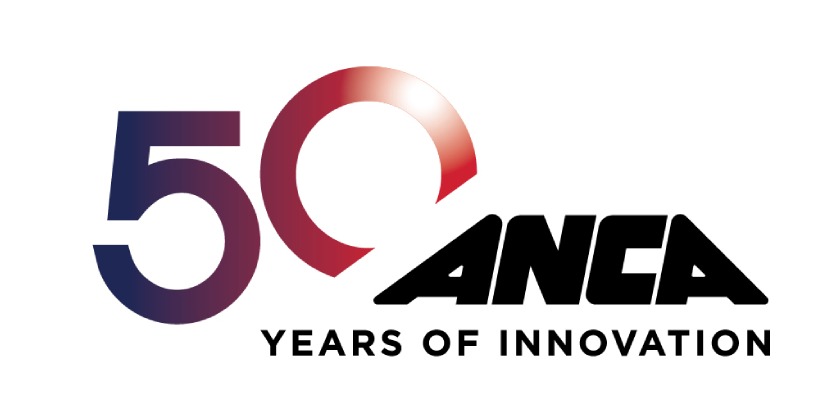
This innovative feature enables the production of consistently high-quality taps by addressing a key challenge – thermal growth.
Introducing a breakthrough in tap manufacturing: ANCA’s patented Motor Temperature Control (MTC) technology. This innovative feature enables the production of consistently high-quality taps by addressing a key challenge – thermal growth.
True to ANCA’s commitment to solving real-world manufacturing issues, MTC tackles the problem of inaccuracy and variation caused by thermal expansion. Traditionally, manufacturers rely on measurement and compensation to control these variations, adjusting for thermal and mechanical changes during grinding. But what if there was a way to eliminate a major source of inaccuracy altogether?
ANCA’s MTC does exactly that. This patented technology allows operators to set the spindle temperature for production, and the machine automatically monitors and maintains that temperature. By stabilizing the spindle’s thermal environment, MTC removes fluctuations caused by thermal growth, ensuring greater precision and consistency in tap production.

Let’s apply this unique and innovative solution to the TapX, using the cresting operation as an example.
Thread cresting is one of the most important tap features to get right. The relief of the thread typically involves a drop of 10-20 microns over the thread. The quality and shape of the thread crest are critical to the performance of the final (cut or formed) thread.
Threading is often the final operation in the manufacturing of parts, so taps play a crucial role. We do not want to scrap parts due to a tapped thread when all other value has already been added to the part. For example, the cresting affects:
Load Distribution and Thread Strength: Different crest types offer varying load distributions. High-load applications rely on high surface contact from a particular crest shape, such as a flat crest. The tap needs to form this large area without jamming or breaking.
Leak Tightness: Certain crest shapes, like rounded crests, can be more challenging to manufacture but are essential for creating effective seals in gas or fluid environments.
Thread Engagement: V-shaped threads provide high precision with increased thread engagement, while a tapered crest offers a more forgiving environment for quick or easy assembly, as well as being more durable with reduced wear.
Many tap manufacturers also have their own unique or specialized crest designs to achieve specific characteristics for a particular customer or industry. This is where ANCA’s TapX shines.
As mentioned in our previous article, reducing coolant pressure is one key to creating conditions for a more controlled operation. However, MTC takes a leap forward by regulating and maintaining a controlled manufacturing environment.
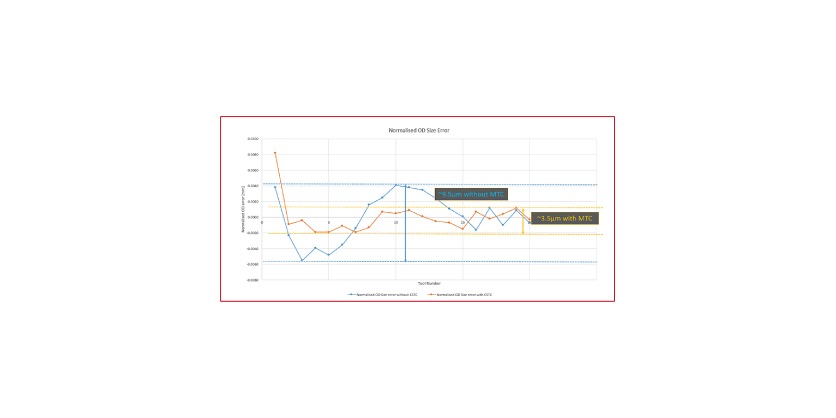
ANCA’s extensive experience has shown that thermal variation in the spindle contributes to variation in tool dimensional accuracy. OD finish operations are particularly sensitive to this. Using MTC significantly improves OD consistency over a batch.
Controlling the production environment with MTC enhances the accuracy, quality, and finish of the tap, leading to several benefits:
- Improved thread quality and surface finish
- Enhanced thread engagement and load-bearing capacity
- Increased thread wear and durability
- Reduced cutting forces and improved lifespan
More Information
For more information, visit www.anca.com or contact your local ANCA representative.
Related Story
Machine Man Reflects on 50 Years In a Challenging But Rewarding Field
For a half-century, ANCA has made the machines that make the tools that make the world go around.
One half of its founding pair, Pat McCluskey, has designed many grinding machine tools in that time.
He says that two things have remained focal when designing a machine: the customer and their expectations, and the manufactured cost.
It is never the result of a whim. It always follows information fed back through a two-way communication process on customer challenges, and meticulous market research, which is then presented to Pat’s team. Then the design gets underway.
If it sounds straightforward, it never is.