Software PNOZmulti Configurator – What’s New in Version 11.4
July 29, 2024
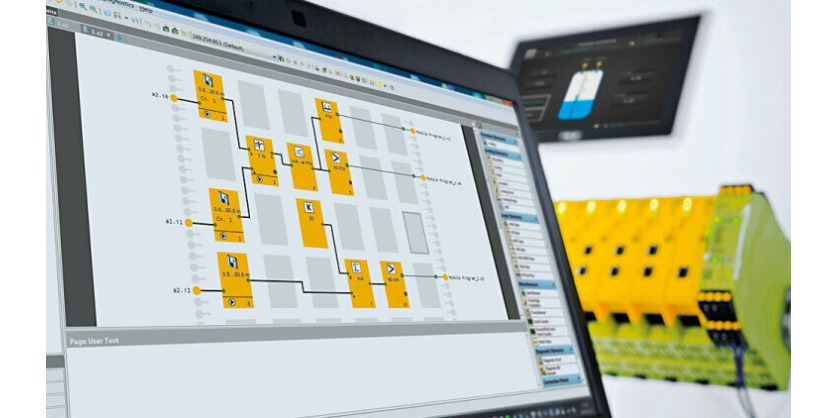
The software tool PNOZmulti Configurator is used to configure the hardware of the safe small controllers PNOZmulti 2 and to create the safety circuit. The original configurable safety program is proven to be easy to use.
Version 11.4 includes these new features:
Hardware:
Decentralised input and output modules of protection type IP67 with 8 safe inputs and 4 safe semiconductor outputs, which allow the direct connection of decentralised peripherals via four 5-pin M12 female connectors to PNOZmulti 2. In total up to 64 sensors or actuators can be flexibly monitored in the field. Less wiring saves costs during commissioning. A version with stainless steel screw connections is available, for use in the food industry for example.
A new ESI file:
Version 102, for the secure Safety over EtherCAT module PNOZ m EF EtherCAT FSoE has been integrated into the software tool. Using FSoE means you can implement safe plant structures with a “one-cable solution” at fieldbus level.
Motion monitoring modules:
Frequency filtering can be configured to suppress short-term implausible frequency signals or EMC interference.
Security functions:
The base unit PNOZ m B1 protects you against unauthorised access via user management. To access the device or perform certain tasks via PNOZmulti Configurator, a user must authenticate with their access data. Thus using PNOZmulti 2 is not only safe but also secure!
Download now! No licence costs – Version 11.4 PNOZmulti Configurator
Software PNOZmulti Configurator – What’s new in Version 11.3
Laser scanner function blocks for PSENscan, motion monitoring for AGVS
From software version 11.3.0, new blocks provide for the most secure und flexible monitoring of the:
The zone selection function block enables productive solutions for stationary and mobile danger zone safeguarding in conjunction with the safety laser scanner PSENscan, used to monitor 2D zones. In this way, for example, it is possible to monitor open robot cells safely, or also guarantee efficient processes in a logistics or production environment.
Motion monitoring software blocks for safe synchronisation monitoring, for example, plus three others for safe position monitoring (Safe Position Comparison, Safe Position Range and Safe Position Monitoring), are available for monitoring automated guided vehicle systems (AGVS). They are used in conjunction with the safe motion monitoring modules PNOZmulti 2.
– With safe synchronisation monitoring, two axes are compared – a comparison is possible based on higher, lower or same speed. Tolerance windows can be defined in the software tool, enabling an even more flexible application. PNOZ m EF 2MM is the module of choice in this regard. Safe detection of anomalies in the synchronisation of two axes protects human and machine. Also, synchronous operation can be monitored on synchronous axes. Safe path detection is enabled by monitoring and comparing the two drive axes on an AGVS.
– When safe position monitoring is used, the position and position range of an axis can be monitored. The modules PNOZ m EF 1MM/2MM/1MM 2DO can be used for this purpose. The steering axis and current position of an axis can be monitored safely once a reference marker to detect the zero point has been set.
Hardware – Perfectly tailored to the application:
- The input module PNOZ m ES 16DI has 16 digital inputs and monitors standard applications.
- The communication module PNOZ m EF EtherCAT FSoE enables safe data transfer with Safety over EtherCAT in conjunction with the base unit PNOZ m B1. PNOZmulti 2 can be used as FSoE Master, FSoE Slave or EtherCAT Slave.
- Decentralised input and output modules PDP67 F 10DI4DO (VA) forward signals from the connected sensors to the safe small controller PNOZmulti 2. New features are the four safe semiconductor outputs on the PDP67, which enable safe sensor technology such as the modular safety gate system PSENmlock to be connected directly to the PNOZmulti 2 via cable. Up to four of the modules with protection type IP67 can be connected to the PNOZmulti 2 via the link module PNOZ m EF PDP-Link. Up to four safe sensors per PDP67 module – a total of up to 64 sensors – can be monitored flexibly in the field in this way. A version with stainless steel screw connections is available, for use in the food industry for example. M12 plug-in connectors link sensors and actuators quickly and easily to the PDP67 module. Complicated wiring is avoided. That reduces costs when expanding and commissioning modular production plants.
Your application advantages:
- Maximum flexibility due to the module program configuration
- Safe solutions for stationary and mobile danger zone safeguarding with the laser scanner PSENscan
- Parameters for motion monitoring safety functions are easily set via software, for the safe monitoring of automated guided vehicle systems (AGVS)
- Software tool can be used free of licensing costs
Software tool PNOZmulti Configurator – Full Version 11 available free of licence costs!
From Version 11 there is a significant change in terms of licensing: you can now use the “basic” functionality of the software tool PNOZmulti Configurator without any licence costs. The software can be downloaded free of charge and used in automation projects. A licence fee is still payable for “Advanced” software elements.
Version 11 is used to create new PNOZmulti 2 projects and to open and edit existing PNOZmulti 2 projects. Powerflow, diagnostics, error stack etc. are available as usual for commissioning and maintenance.
Major innovation in Version 11
- “Basic” version has no licence costs
- New, higher performance software architecture
- Supports Windows 64-bit system
- Streamlining of the product range: all 2nd generation base units such as PNOZ m B0, PNOZ m B1, PNOZ m B1 Burner as well as the new base unit PNOZ m B0.1
- All PNOZmulti 2 expansion modules
Software tool Version 10.14, long-term-supported version
- Contains hardware from the PNOZmulti 2, PNOZmulti Classic and PNOZmulti Mini product ranges
- This version can be used to migrate PNOZmulti Classic or Mini projects to PNOZmulti 2
- PNOZmulti Classic/Mini projects Open, edit, create projects
- New PNOZmulti 2 hardware is only supported from Version 11.0 and above
- Existing licence keys can be used
Download now! – Version 11.4 PNOZmulti Configurator
Benefits at a glance
- Software with pre-assembled, certified blocks
- Easy, retrospective modifications and adjustments to the configuration
- Simple, comprehensive diagnostics mean short machine downtimes and high plant availability
- Worldwide safety standard for various automation environments and different communication systems
- Rapid commissioning and minimal wiring work – See for yourself!
Features at a glance
CONFIGURE RATHER THAN WIRE THE SAFETY CIRCUIT
- Operation is intuitive: creating your safety circuit is refreshingly easy
- Freely configurable: parameters for all inputs and outputs are conveniently set with a few clicks in the software tool
- Use logic operators to link these to form a safety circuit using drag-and-drop
- You select all function, logic and output elements on the workspace
AUTOMATIC ERROR CHECK, PROTECTION AGAINST CHANGES
- Safe: the software tool checks the created safety circuit for error sources
- Protected: you can certify the completed configuration, thereby protecting it from unwanted changes
- Flexible: you can edit, amend or expand uncertified circuit diagrams at any time
- Simple: for documentation just print out the circuit diagram configuration
More Information
Flyer for safe small controllers PNOZmulti Configurator Version 11
Source
Related Story
Software PNOZmulti Configurator – What’s New in Version 11.3
From software version 11.3.0, new blocks provide for the most secure und flexible monitoring of the:
Laser scanner PSENscan:
The zone selection function block enables productive solutions for stationary and mobile danger zone safeguarding in conjunction with the safety laser scanner PSENscan, used to monitor 2D zones. In this way, for example, it is possible to monitor open robot cells safely, or also guarantee efficient processes in a logistics or production environment.
Automated guided vehicle systems (AGVS):
Motion monitoring software blocks for safe synchronisation monitoring, for example, plus three others for safe position monitoring (Safe Position Comparison, Safe Position Range and Safe Position Monitoring), are available for monitoring automated guided vehicle systems (AGVS). They are used in conjunction with the safe motion monitoring modules PNOZmulti 2.