Simple Connection of Analog Sensors and Actuators in IO-Link Networks
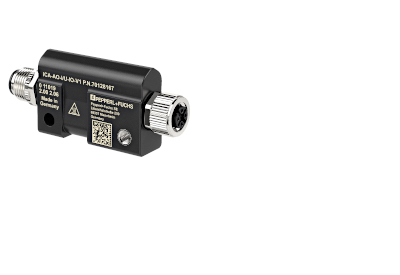
January 11, 2022
New IO-Link Analog Converters Enable Fast and Flexible Integration of Devices with Analog Interface to an IO-Link Master. More and more users are converting their plants to digital communication solutions such as IO-Link. In addition to a variety of other benefits, these provide detailed parameter, diagnostic and identification data. In standard machine and plant engineering, however, sensors and actuators with analog interfaces are still frequently used—even though their connection is complicated and expensive because shielded cables are required. Some of these sensors and actuators cannot simply be replaced by digital solutions when converting to IO-Link due to limited availability. Therefore, analog devices previously had to be connected to a control system via other communication solutions or parallel wiring, which took a lot of time and caused additional costs.
Due to the new IO-Link analog converters, sensors and actuators with analog interfaces can now be quickly and easily connected to an IO-Link master. This then passes on the data from the digital IO-Link devices and the analog sensors and actuators to a control system in bundled form, saving users time and money.
Flexible Integration Directly into IO-Link Networks
The IO-Link analog converters are installed between the IO-Link master and the analog device via M12 connectors. Due to the space-saving housing design, they can be mounted even in the smallest installation spaces.
While the converters of the ICA-AI-* series enable the connection of analog sensors, the devices of the ICA-AO-* series can control analog actuators via IO-Link. Both variants can be configured for current signals (0 … 20 mA / 4 … 20 mA) as well as voltage signals (-10 … 10 V / 0 … 10 V), so that a wide variety of devices with analog interfaces can be flexibly integrated. IO-Link enables the configuration of value ranges for the analog signals. Exceeding or falling below these values results in a corresponding diagnosis.
Highlights of the IO-Link Analog Converters
- Simple connection of sensors and actuators with analog interface to IO-Link
- Uncomplicated installation via M12 connectors
- Small housing enables installation in the tightest installation spaces
- IO-Link interface for providing parameter, diagnostic and identification data
- Configurable for current signals (0 … 20 mA / 4 … 20 mA) and voltage signals (-10 … 10 V / 0 … 10 V)
- Degree of protection IP67
Learn more about the New IO-Link Analog Converters here