Renown Electric: i-Alert Monitoring Solution Sensors
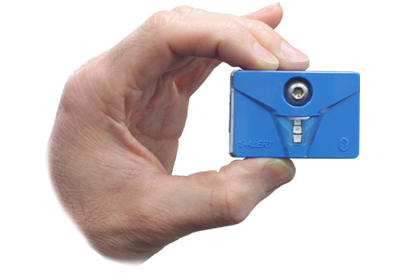
March 8, 2021
The health of industrial machinery may be determined by measuring the equipment’s vibration signature. If a gear, fan, or other essential component is out of alignment or otherwise functioning incorrectly, the vibrations of the machine will change. Monitoring vibrations can help to proactively identify problems before they substantially impact operations.
Vibration analysis typically happens as part of a regularly scheduled maintenance cycle with data being compared monthly, quarterly, or annually. Analysts will gather a baseline vibration signature from equipment while it is functioning at optimal levels, then periodically compare that data with new vibration readings to identify potential issues.
The idea of constant monitoring has traditionally been impractical – until now. Thanks to advances driven by the Industrial Internet of Things (IIoT) and continuing developments in smart technology, equipment vibration can now be monitored in near real-time, enabling early identification of problems as they arise.
Renown Electric provides our customers with preventative and predictive maintenance solutions that will help them to avoid costly downtime and catastrophic equipment failures. With the i-Alert Monitoring Solution, manufacturers and other users of industrial equipment can monitor, troubleshoot, and gather data on many applications using only i-Alert® sensors and a smartphone.
About the i-Alert Monitoring Solution
The traditional periodic predictive maintenance (PdM) inspection model comes with inherent flaws. Inspections are not only expensive, but a lot can go wrong between inspection periods.
With the i-Alert system, industrial operations can reliability monitor the health of assets without worrying about the financial cost. This affordability also means that users can monitor a broader range of equipment instead of inspecting only the most critical machinery. The i-Alert2 Equipment Health Monitor tracks factors such as:
- – 3-Axis Vibration
- – Temperature
- – Kurtosis
- – Machine run-time counter
- – Fast Fourier Transform
- – Time Waveform
Key benefits and features of the i-Alert Monitoring System include:
i-Alert monitors the health of any rotating machine, including pumps, motors, fans, mixers, gear boxes, and more. The system monitors and stores up to 720 data points and will trigger automatically in response to any change in the state of your machinery, capturing critical spectral and time waveform data to help your PdM specialist diagnose problems quickly.
Safety
Data is easily accessed via Bluetooth from a distance of 30-100 feet away, which means inspectors don’t need to physically interact with each piece of equipment.
Ease of Use
The i-Alert app enables simple use by any everyday user with a smartphone. Data gathering can occur quickly and easily as part of normal operator rounds.
Time Saving
Time spent performing route-based data collection may be reduced by up to 50%, as the i-Alert scans multiple machines at once. Eliminating the time-consuming and costly process of temporary sensor mounting frees up vibration analysts to focus on chronic equipment health problems.
Early Detection
The data provided by the i-Alert® system allows early identification of upcoming system failures and provides information to address these problems proactively. With continuous monitoring, trends can be established without waiting for several months of periodic inspection data.
Accessibility
The i-Alert does away with the use of expensive vibration analysis tools, which can cost tens of thousands of dollars and require costly special training. Now, anyone with a smartphone can access the same information.