POSITAL: Safety First – Through Clever Design
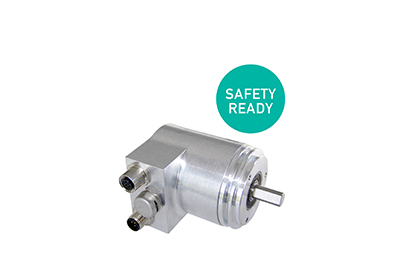
June 30, 2020
Sensor manufacturer POSITAL has introduced an inexpensive and flexible alternative for safety-critical motion control systems. Supplementing its existing range of formally certified SIL safety encoders, the new ‘diverse-redundant absolute encoders’, based on non-certified standard components, are an attractive choice for many installations where functional safety is required. When combined with functional safety PLCs, these devices are suitable for applications that are required to conform to Performance Level/ PL d, Cat. 3, according to ISO 13849. ‘Redundancy’ means that these devices contain two independent sensor systems. Measurements from these two systems are processed by a functional safety PLC. If both measured values are the same (within defined tolerances), safe operation is assumed. If there are deviations, the controlling PLC triggers an alarm – with the option of transitioning the system to a defined safe condition. To be on the safe side, POSITAL makes use of a combination of magnetic and optical sensor technology – the key words are diverse redundancy. Applications for the new safety-ready encoders range from heavy construction equipment and mobile machines, through crane technology and elevators, to complex stage technology for theatrical or film productions.
Instead of installing the redundant systems in separate housings, POSITAL has chosen a clever all-in-one solution. The new devices are designed as space and cost-saving tandem encoders. The magnetic and optical sensor elements are integrated in a compact housing (58 mm in diameter) that is easy to install. Resolution is 16 bits per revolution. Like other products in the modular POSITAL portfolio, the encoders are available with a wide variety of mechanical options. The spectrum ranges from robust housings, designed for protection levels up to IP67, through different connector types, to many flange and shaft variants (hollow or solid shaft). Communications is through the well-established CANopen interface. The new safety-ready encoders are suitable for harsh environments and a wide temperature range. Magnetic encoder technology is inherently robust, while the optical components have been specially protected against condensation by the addition of an extra membrane. Both sensor elements, optical and magnetic, are absolute encoders that measure the position value in single and in multi-turn mode – absolutely battery- and maintenance-free.
“From the very beginning, we placed great emphasis on the diverse design,” underlines Christian Fell, POSITAL’s General Manager for the Americas. “By using completely different measurement technologies, we wanted to simplify the certification of entire systems for our customers as much as possible.” With a diverse-redundant approach, errors can be detected much more easily than in a setup that makes use of two identical measurement devices. Both systems – optical and magnetic – are based on established encoder technologies that have been core competencies of POSITAL for decades. After being one of the pioneers of optical absolute encoders for precision applications in the 1960s, POSITAL in the last 15 years has become a trendsetter with high-end magnetic encoders that feature excellent dynamic response and accuracy – enabled by improved computing power, innovative algorithms, and energy-harvesting multi-turn functionality.
The new sensors are suitable for applications requiring functional safety up to Performance Level/PL d, Cat. 3 of ISO 13849. Compared to encoders with SIL-certified safety functions, they are less costly while providing more operational flexibility. Individual parameters – like the exact specifications for activating the ‘Safe State’ function – can be programmed into the PLC by the system integrator. “It is clear that SIL-certified safety encoders, which were widely introduced after the enactment of the European Machinery Directive in 2006, will continue to play an important role in specific niches,” says Fell. “Their primary use will remain in safety installations with a small number of encoders, where the customer is willing to spend the extra money for SIL-certified equipment to achieve results – quickly and easily.”
For more information, visit www.posital.com.