POSITAL Kit Encoders for Stepper Motors
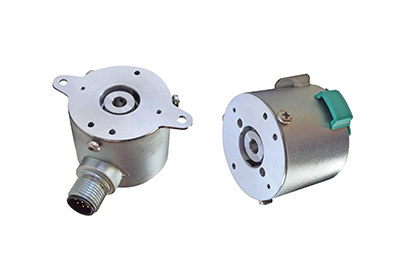
July 3, 2019
While servomotors remain the gold standard for precision motion control in industrial machinery, the improved performance of stepper motors is making these lower-cost devices an increasingly attractive alternative for many applications. The key to these performance gains is the addition of rotation-measuring encoders, especially the new absolute multi-turn kit encoders from POSITAL.
Stepper motors are brushless DC motors that turn their shaft by a small fixed amount (step) in response to a control signal. However, this is an open loop control system: if the motor fails to complete a step (e.g. due to unexpected mechanical resistance) system accuracy is degraded. This can be overcome by adding a simple incremental encoder to provide feedback as to whether step motions have occurred. POSITAL’s new magnetic encoders take this a step further by providing absolute position feedback. (With incremental feedback, control system needs to keep an accurate count of the number of steps in order to track the absolute rotary position of the motor shaft. If this count is lost or corrupted – e.g. due to a power interruption – knowledge of the position of machine components is also lost. It is usually necessary to return the machinery to a known starting position and re-initiate the step count. By contrast, with absolute measurement systems, complete position measurements are available whenever the control system queries the encoders. Production processes can be restarted directly with minimal loss of time and materials.)
POSITAL’s absolute kit encoders are available with multi-turn measurement ranges, which can be very useful when a motor is connected to a screw shaft, cable drum or gear reduction system. The multi-turn rotation counter is self-powered, using POSITAL’s Wiegand energy harvesting technology. The rotation count is always up-to-date, even if the machine has moved while control system power was out. No backup batteries are required!
POSITAL’s encoders for stepper motors are “kit” or modular devices, designed to be integrated into a motor housing, measuring the rotary position directly from the drive shaft. Kit packages are available with the same mounting form factor as popular incremental encoders for NEMA-standard stepper motors, making these encoders convenient drop-in replacements for less advanced incremental encoders. The magnetic measurement module is compact (37 mm diameter, 23 mm deep) and highly resistant to dust, moisture and shock/vibration loading. Shields are available to protect the measurement module from external magnetic fields. SSI and the more advanced “BiSS C” communication interfaces have been implemented. Both are open-source interfaces that are compatible with a wide range of PLC’s and computers.
Stepper motors with built-in position sensors are an increasingly attractive solution for positioning tasks in manufacturing equipment, packaging machinery, robots and other applications where a reliable, cost-efficient drive mechanism is needed.