Mitsubishi Electric’s KOTSUMON System Uses AI Video Technology to Analyze Production Line Workers’ Motions
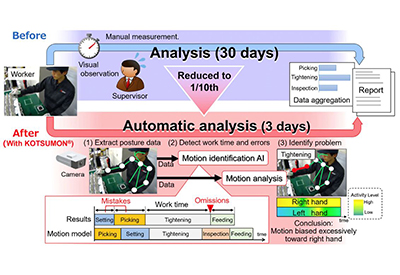
October 15, 2019
Mitsubishi Electric Corporation announced recently its newly developed KOTSUMON system uses the company’s Maisart artificial-intelligence (AI) technologies to extract video data for the automatic identification and analysis of specific types of human motions, such as those of workers on production lines. The system simply requires a normal video to automatically measure work efficiency and detect omitted or mistaken motions, which manufacturers are expected to use to upgrade their line operations for improved productivity.
Key Features
-
Measures work time and detects mistaken motions to reduce analysis time to one-tenth normal
Mitsubishi Electric’s new system automatically identifies motions with 90 percent accuracy by using AI to learn a worker’s poses and motions. Since the analysis can be performed with normal videos, there is no need to attach sensors to the worker, etc. Moreover, the analytical workload and time is just one-tenth** that of visual observation performed manually by supervisors. The technology was developed in collaboration with Professor Aoki Yoshimitsu and Aoki Media Sensing Laboratory of Department of Electrical Engineering, Faculty of Science and Technology, Keio University.
-
Motion extraction and visualization enables standardized analysis by any supervisor
Correcting a line worker’s motions is generally a three-step process: firstly, detect inappropriate or useless motions; secondly, determine needed corrections in physical processes and/or working environment; and thirdly, teach the worker more efficient motions. Often, however, workers move too fast to detect problems visually, and analytical results can vary from one supervisor to the next, making it difficult to obtain consistently useful results through manual analysis.
Mitsubishi Electric’s new system, which is based on the principles of motion economy, can extract a worker’s motion data from a video to automatically detect incorrect movements. Even problems not detectable manually can be identified automatically to ensure consistent, standardized results regardless of the supervisor in charge.