Highly Functional and Incredibly Energy-Efficient Thanks to Silicon Carbide
August 27, 2024
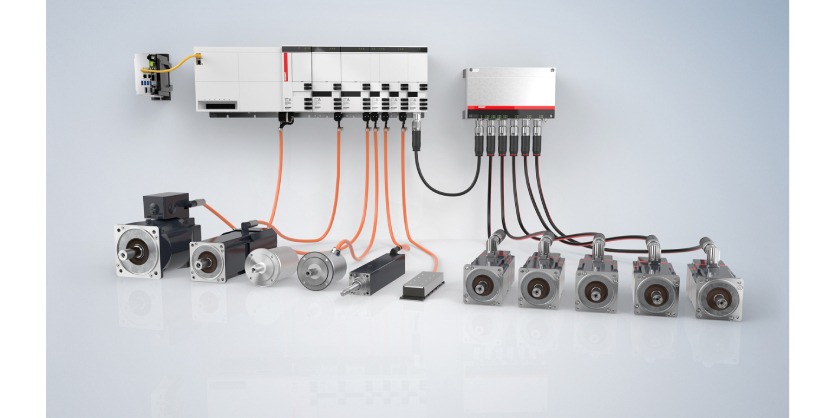
AX8000 multi-axis servo system extended by SiC axis module
The AX8000 multi-axis servo system from Beckhoff is renowned for its high functionality and has now been expanded to include an axis module with silicon carbide (SiC) semiconductors instead of the conventional IGBTs. These SiC semiconductors set new standards in switching voltage and speed, switching losses, and size. The advantages for the AX8000 are clear, as the lower power loss means the same housing can now be used for 28 A nominal current and for the 18 A IGBT device. It also results in 55% more output for the same axis module size.
The AX8000 multi-axis servo system operates within a motor performance range of 0.5 to 20 kW. The combined feed-in and axis modules with 40 kW feed-in power each have an inverter with 12.5 or 20 kW integrated directly into the housing. These can be used to operate high-frequency spindle drives for CNC machines at speeds of up to 72,000 rpm, as well as large motors for injection molding machines, blow molding machines, and more.
A further 20 kW is available on the DC bus, which can be used for the X, Y, Z, A, and B-axes. The AX-Bridge quick connection system simplifies installation in the control cabinet with its simple tool-free assembly method. Each individual module can also be removed from the network later on without having to move or dismantle the other devices.
One Cable Technology and safe drive technology
Beckhoff had its One Cable Technology (OCT) for drive technology ready for the market back in 2011. Fast-forward to today and over 90% of all Beckhoff motors are now supplied with OCT. Even TwinSAFE Safe Motion, the safe drive technology, can be implemented via OCT with just one cable. The motors can be fitted with either a Hiperface DSL or EnDat 3 safety encoder, which enables safety functionality up to SIL 3 or PL e. Offering resolutions of up to 24 bits, the encoders can achieve outstanding accuracy, consistent performance, and high dynamics. They are also available either as single-turn or multi-turn variants without battery backup – and without the risk of losing the reference position.
The AX8000 multi-axis servo system is available either with TwinSAFE STO/SS1 or with TwinSAFE Safe Motion. TwinSAFE Logic is directly integrated into both options to facilitate communication and modularization of the safety application. The functionality can be achieved via secure FSoE communication, direct wiring, or locally within the servo drive using the integrated TwinSAFE Logic. This provides the basis for the flexible implementation of safe drive functions. A total of 17 different functions are available when using a motor with an approved safety encoder.
Servo system with XFC functionality
Beckhoff components that offer eXtreme Fast Control Technology (XFC) meet the following requirements:
- EtherCAT cycle time of ≤ 10 µs
- support EtherCAT distributed clocks
- extremely fast digital inputs
- integration of oversampling technology
With a minimum EtherCAT cycle time of 62.5 µs, the AX8000 multi-axis servo system is one of the fastest bus devices on the market. This is also sufficient for applications demanding maximum performance, where the setpoints change extremely quickly. The distributed clocks synchronize all axes in the nanosecond range. Each axis module or axis has two very fast digital inputs, and their signals are automatically provided with the current position and a timestamp. With oversampling, setpoints can be transmitted precisely and highly dynamically in the current controller cycle – even with slower bus cycles.
Software for configuration, commissioning, and maintenance
The TwinCAT 3 Motion Designer can be used to determine the optimum combination for a specific application from the many possible variants of motors, gearboxes, cables, and servo drives. Specifying the available supply voltage is crucial here for making optimal component choices. The appropriate mechanism can then be selected from a series of predefined load cases and the desired movement profile can be used for the calculation. This allows the Motion Designer to suggest suitable gearboxes, motors, and servo drives.
Add to this the appropriate connection cables and accessories, such as a braking resistor, regenerative module, or mains choke, and the result is a parts list for the entire drive technology – not just for a single axis, but for the entire machine. Even the expected power loss of all components is determined so that the control cabinet air conditioning can be easily dimensioned on this basis.
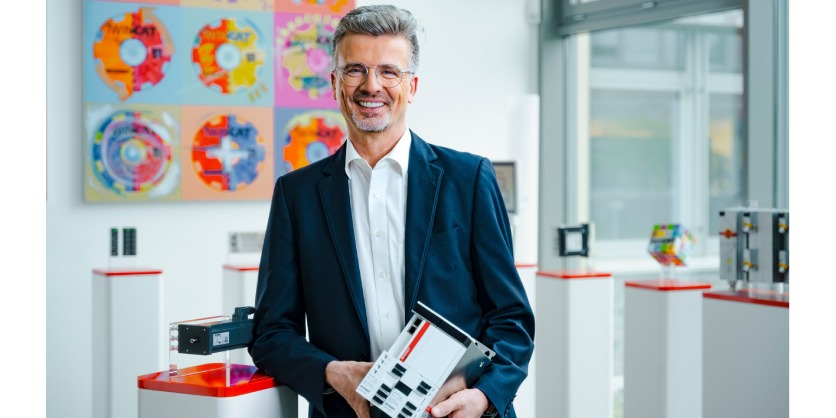
The TwinCAT 3 Drive Manager 2 is an intuitive commissioning tool in the form of software that supports and guides users during configuration and commissioning of the servo axes. The Drive Manager scans the EtherCAT network for all connected servo drives and motors, automatically sets the correct parameters depending on the supply voltage, and reads the electronic nameplates of the motors.
What’s more, it also activates cogging compensation and provides graphical charting based on TwinCAT Scope to facilitate monitoring and adjustment of the motor movement. Another new function is autotuning, which quickly and automatically adjusts the control parameters and required filters based on a Bode diagram.
Friction and wear inevitably occur during machine operation, eventually impacting the control system by causing an unnoticed increase in power consumption or a greater lag error. The TwinCAT Analytics software is ideal for visualizing this impact. This is because the servo drives provide a large number of measured variables that can be recorded and processed with TwinCAT Analytics, including temperature, current, voltage, torque, and braking power, which can be analyzed in millisecond intervals.
Envelope curves can be placed around the characteristic curves with options to trigger warnings and alarms if they are violated. Even the energy consumption per component produced can be regularly documented in reports with TwinCAT Analytics and, if required, even compared over the years with the help of long-term storage.
Servomotors made in Germany
The production of highly dynamic and high-quality servomotors from Beckhoff began in 2011 with the AM8000 series and the innovative One Cable Technology. In the years that followed, numerous additional motor variants were developed to offer increased rotor inertia, performance-enhancing active forced cooling, anodized housing, stainless steel housing for demanding environmental conditions, linear actuators, and iron-core linear motors. Motors with an integrated servo drive for low voltage (24 or 48 V DC) and high-voltage technology. The AM8000 motor series covers the entire voltage range from 24 to 480 V.
More Information
Related Story
Beckhoff Launches Compact, Multi-I/O Interface for Endless Use Cases in One Device
Beckhoff’s new EL8601-8411 EtherCAT Terminal offers incredible interface flexibility in a compact, 12-mm-wide design. With up to 12 signal interfaces (8 x DI, 2 x DO, 1 x AI, 1 x AO) and nine signal types in one terminal, the multi-interface is ideal for numerous applications. These use cases include systems that require only a few complex signals or to enable highly flexible signal configuration on custom machines without adding single-purpose hardware.