Festo’s Bionic Mobile Assistant – a Robotic Helping Hand Like None Other
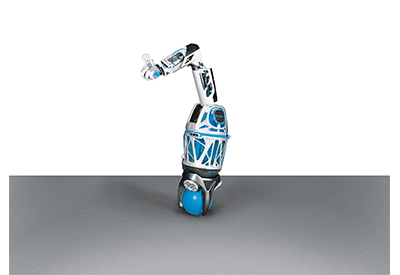
November 18, 2020
Advancing gripping technology is essential for promoting new uses for automated systems. Festo’s Bionic Mobile Assistant robotic helper, one of the latest reveals from the company’s Bionic Learning Network, represents a significant advance in mimicking that most amazing gripping tool of nature – the human hand.
The Bionic Mobile Assistant embodies three major subsystems: Bionic SoftHand 2.0, an upgraded version of the pneumatic gripper first presented by Festo in 2019 that mimics hand movements and actions; the DynaArm electric robot arm on which Bionic SoftHand 2.0 is mounted; and a ballbot for 360º mobility.
That makes Bionic Mobile Assistant more than a mere collaborative robot. Among many, potential uses of this concept robot, it would be perfect as a personal assistant or service robot, or for carrying out ergonomically strenuous or monotonous assembly tasks. It also could carry out simple tasks in challenging environments, like serving meals in hospitals where there is an increased risk of infection or in areas staff cannot access due to infections.
With its unique combination of force, dexterity and fine motor skills – the human hand is a true wonder of nature and a supreme challenge to adapt to mechanize. To enable the Bionic SoftHand 2.0 to carry out those movements somewhat realistically, compact valve technology, sensors, electronics and mechanical components are integrated in the tightest of spaces. The fingers and opposable thumb are made of flexible bellows structures with air chambers, surrounded by a firm yet yielding knitted fabric. This makes the hand light, adaptive and sensitive, yet capable of exerting strong force. The pneumatic fingers are actuated by a compact valve terminal, with piezo valves, mounted on the hand.
Making the thumb and index finger longer than in Bionic SoftHand 1.0 increased the lateral swivel range of both fingers. They now work well together and grip with great precision. Thanks to a 3D-printed wrist with two degrees of freedom, the hand also can move both back and forth, and left and right for a very tight gripping radius.
To increase the stability of the fingers, each air chamber contains two structural elements that act like bones. A bending sensor determines the positions of the fingertips. The hand also wears a glove with tactile force sensors, which allows it to sense the nature of the item to be gripped, and adapt its gripping force accordingly.
The hand also has a depth camera inside the wrist so it can visually detect objects and grip them, even if they are partially covered.
The Bionic SoftHand 2.0 is mounted on the electric DynaArm. The DynaArm can carry out fast and dynamic movements thanks to its lightweight design with highly integrated drive modules that weigh just one kilo. The ballbot is actually a sophisticated drive. The robot balances on it, so the Bionic Mobile Assistant can move freely in all directions. All energy supplies are on board: a battery for powering the arm and robot, and a compressed air cartridge for the pneumatic hand. The robot can work autonomously, orienting itself independently in three dimensions using two cameras.
Thanks to its modular concept, the Bionic SoftHand 2.0 also can be quickly mounted and commissioned on other robot arms. On Festo’s Bionic Cobot or the Bionic SoftArm, the gripper forms a completely pneumatic robotic system.
For more information, visit www.festo.com.