Festo Remote I/O Solutions for Electric, Pneumatic Motion Reach Unrivalled Heights With CPX-AP-A
September 6, 2023
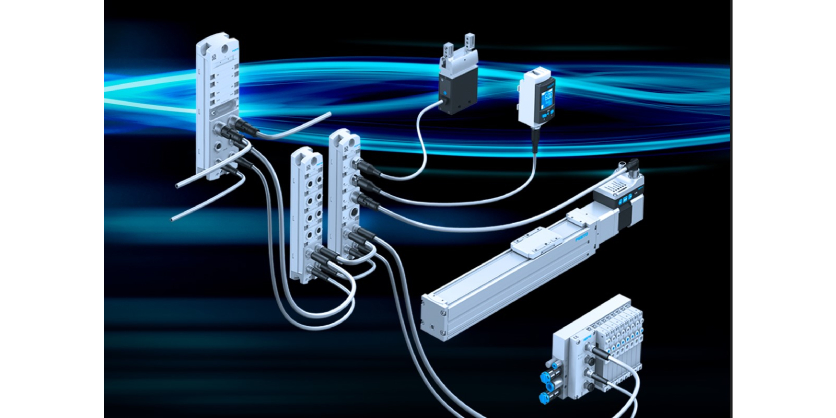
Festo Remote I/O Solutions for Electric, Pneumatic Motion
With the recent introduction of its distributed I/O solution CPX-AP-A, along with its established CPX-AP-I decentralized I/O, Festo now offers a range of electric and pneumatic automation solutions that is unmatched for performance, flexibility, cost savings, and engineering productivity. AP stands for Automation Platform and this backplane-based remote I/O system has been in development for a decade.
“The Festo AP backplane communications platform, that provides a central communication and data transfer I/O interface, is a combination of everything that we’ve learned over the past 25 years of doing electric and pneumatic linear automation solutions,” said Tim Sharkey, Director of Electric Automation, Festo North America. “AP backplane communications brings together enormous functionality and creates a higher level of integration among our devices than we’ve ever had. AP continues the tradition of Festo product development and manufacturing excellence. It leverages our strengths.”
Tim Sharkey, Director of Electric Automation, Festo North America
CPX-AP-A is the new line of distributed I/O where modules are attached within a terminal. CPX-AP-I is Festo’s decentralized I/O where modules are connected via cable at distances of up to 50 meters between modules. AP modules, whether on-terminal or individual, are IP65/67 rated and can be located in cabinets, in clusters around the cell, individually placed, and separated at great distances. Every AP module features a high-performance real-time backplane transmission rate of 200 Mbps full duplex.
AP provides the utmost in topology flexibility. It gives machine builders the freedom to optimize the machine or cell by adding I/O where they need it and in ways that will best boost performance and diagnostics capabilities. The AP ecosystem makes it efficient for end-user customers to add functionality as needs arise.
Physically attached on-terminal or connected via cable, all components such as PLCs, valves, motors, drives, and I/O appear to the programmer to be incorporated within one smart terminal under a single IP address. Having the entire distributed and decentralized I/O topology under a single IP address significantly reduces hardware and installation costs while lowering system complexity. Since many PLCs come with a limited number of IP addresses, the Festo solution means more capabilities are possible per PLC.
With all the components appearing to the programmer as resident in a single smart terminal, addressing becomes straightforward, programming time shrinks, and engineering productivity rises. As the functionality and capabilities of the system climb with the addition of modules, the overall distributed and decentralized I/O system becomes simpler to create and maintain.
Festo’s multi-year product roadmap calls for the continued rollout of AP-based PLCs, valves, linear actuators, motors, and drives. For those OEMs and end-user customers wanting extended AP capabilities today, Festo support teams can make much of that happen.
“There are many companies with distributed I/O,” observed Eric Rice, Product Market Manager, Festo North America. “On the other side there are suppliers for electric or pneumatic linear motion. Not one North American supplier on either side of that line comes close to offering the same level of performance, capabilities, and support that stems from the integration of the AP platform with the breadth of Festo motion solutions.”
Eric Rice, Product Market Manager, Festo North America
More Information
For more information on the new Festo Automation Platform and the advantages of working within the Festo ecosystem ‒ the ecosystem that leads to less engineering overhead, fast time to market, and seamless connectivity ‒ visit www.Festo.ca .
Related Product
New Festo CMMT MP Multi-Protocol Servo Drives Provide OEMs with Productivity, Cost Advantages
Festo introduces the CMMT MP multi-protocol servo drive. Every drive in this family is configurable for EtherNet/IP, EtherCAT, PROFINET and Modbus TCP.
With CMMT MP, machine builders supporting multiple communications protocols can reduce their own servo-drive inventories. A unified drive family improves engineering productivity through familiarity with a single platform, simplifies technical support, and accesses a robust supply chain for competitively priced servo drives. Festo showed the benefits of the multi-protocol approach by reducing its own part numbers from 24 to eight.