Festo Electric and Pneumatic Intralogistics Solutions Push/Sort, Grip/Pick, and Lift/Convey
Festo integrates cobots from different manufacturers in a 7th- axis solution for bin picking
March 8, 2024
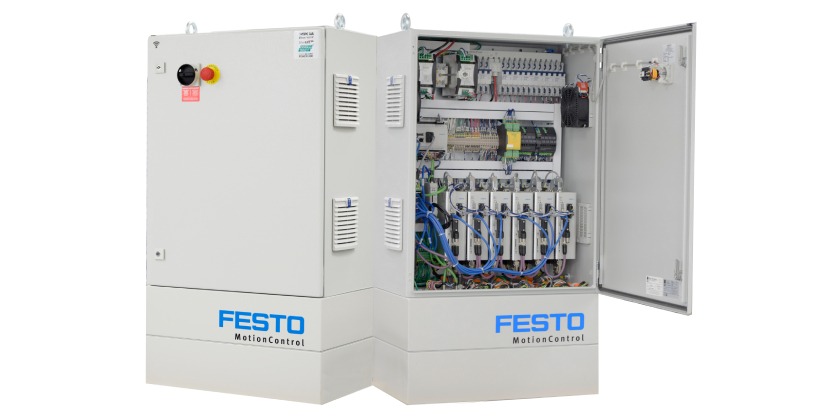
Festo introduces the company’s comprehensive selection of electric and pneumatic components for intralogistics motion automation – pushing and sorting, gripping and picking, and lifting and conveying
“No material handling competitor comes close to Festo’s breadth of electric and pneumatic components and systems, robust supply chain, and ease of commissioning systems into the top control architectures,” said Frank Vanderpool, Industry Segment Manager, Logistics Systems, Festo. “Festo’s one-stop-shop brings intralogistics solutions to market faster, with less engineering overhead.”
7th-axis solution for bin picking
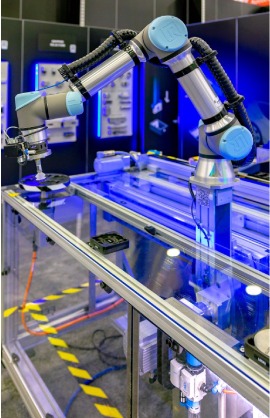
New distribution centers and existing facilities deploy robotic systems to lower labor, increase throughput, and reduce the risk of error when moving their products internally. Seventh-axis robots – robots on an electromechanical linear actuator moving horizontally, vertically, or both – offer productivity and cost advantages in picking and placing and unloading and loading applications.
Adding a linear rail extends the reach of a six-axis robot. Moving the robot closer to the payload allows smaller six-axis robots to be used for the application. Because robots are sized by reach – the longer the reach the larger the unit – 7th-axis solutions using smaller robots lowers acquisition cost. Smaller also means a more compact footprint. Seventh-axis systems can accommodate both six-axis robots and cobots.
In a new dynamic solution of 7-axis robotics in a simulation of efficient bin picking, Festo integrates cobots from two different manufacturers. Festo’s solutions are robot agnostic and system integrators can easily choose the cobot, or robot, best for the end user.
Besides a 7th-axis used for linear transfer, the Festo Motion Control Package (FMCP) panel controls turntables, automatic storage systems, conveyors, and transfer tables. The FMCP solution provides extra space within the panel for future expansion and brackets for wall mounting, which reduces footprint.
The company’s solution for bin-picking includes the adaptive shape gripper DHEF, the adaptive finger gripper DHAS, and vacuum gripping solutions.
Festo’s EGC belt driven linear axes are ideal for 7th-axis solutions and can come equipped with a robot/cobot mounting plate. The EGC has an energy chain for cable management and servo motors optimized for performance. Standard EGC axes are available in lengths of up to 8.5 m with up to 10 m axes available on request. Festo offers a host of other linear actuators, including the ELGC ball screw actuator.
Pushing and sorting
The Festo Simplified Motion Series (SMS) electric axes are comparable to pneumatics in cost and ease of installation, yet deliver the advantages of electrics. SMS axes offer lower energy consumption than pneumatics and generate a wealth of data. SMS axes deliver two-position motion through onboard controls. Or through IO-Link, a standard SMS feature, these axes can be programmed for infinitely variable positioning for flexible pushing and sorting.
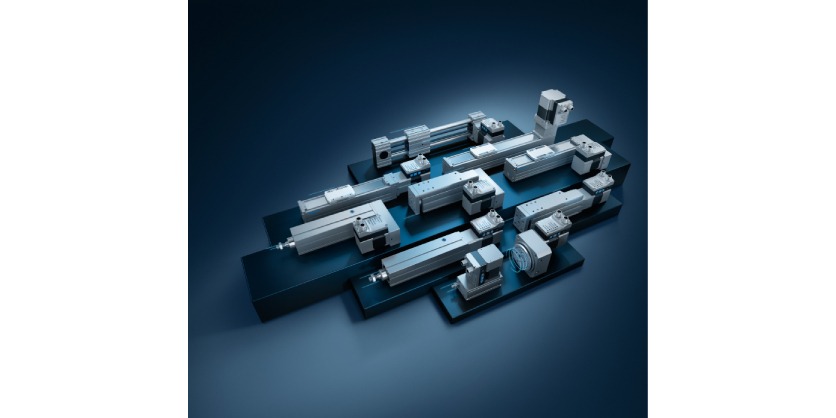
For applications where pneumatics is the optimum cost/performance solution, Festo provides its DFSP pneumatic stopper cylinder, the DSNU ISO standard round-body cylinder with self-adjusting end position cushioning, and the compact, double-acting ADN for fixed or self-adjusting cushioning.
Lifting
The rugged ELGA and ELGC actuators, EMMT-AS one-wire servo motor, and innovative multi-protocol servo drive CMMT-AS offer the ideal package for Z-axis motion. Easily add additional Festo axes and gain X and Y motion for lift and position capabilities. This solution offers low vibration and high rigidity.
Festo’s remote and decentralized I/O platform
Festo offers both the CPX-AP-A distributed I/O and CPX-AP-I decentralized I/O. Whether physically attached on-terminal or connected via cable, all components such as PLCs, valves, motors, drives, and I/O appear to the programmer to be incorporated within one smart terminal under a single IP address. Having the entire distributed and decentralized I/O topology under a single IP address significantly reduces hardware and installation costs while lowering system complexity. Since many PLCs come with a limited number of IP addresses, the Festo solution means more capabilities are possible per PLC. Festo is a leader in adopting and applying IO-Link, and customers will find IO-Link capabilities integral to the new I/O automation platform. This I/O platform is ideal for effective conveyor control.
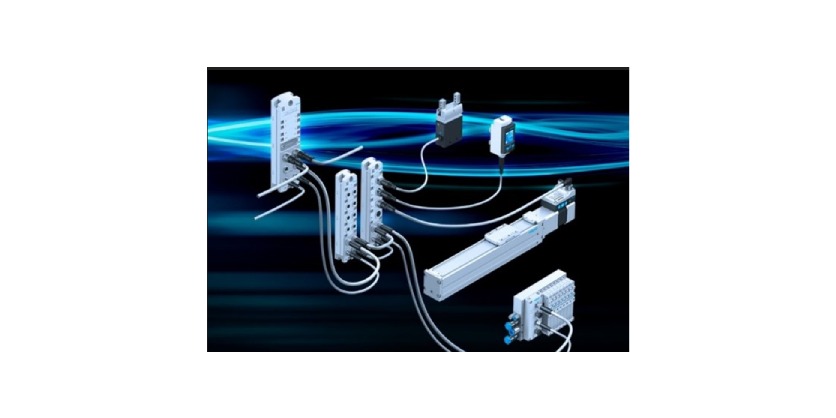
Mechatronic training from the industry leader – Festo Didactic
Festo Didactic, the training arm of Festo, has developed the Festo Learning Experience, Festo LX, a digital learning portal. Festo LX provides training module access where and when it is needed and makes it easy to create individual learning experiences for trainers and trainees.
More Information
Visit the intralogistics page on the Festo website for additional details. For more information on the advantages of working within the Festo ecosystem of less engineering overhead, fast time to market, seamless connectivity, and high-quality components, visit www.festo.com.
Related Product
Festo Introduces DHPL, a Competitively Priced Long-Stroke Parallel Gripper
From recently completed production lines, Festo introduces the DHPL, a new generation of competitively priced long-stroke grippers that offers a host of advantages for high load and torque applications. The DHPL is interchangeable with competitive long-stroke grippers. It provides the added benefits of lighter weight, higher precision, and no maintenance. The new long-stroke gripper is ideal for stacking boxes, gripping plates and shaped parts, and keeping bags open.