Enhancing Efficiency and Sustainability with Rittal’s New Blue e+ S Cooling Units
July 9, 2024
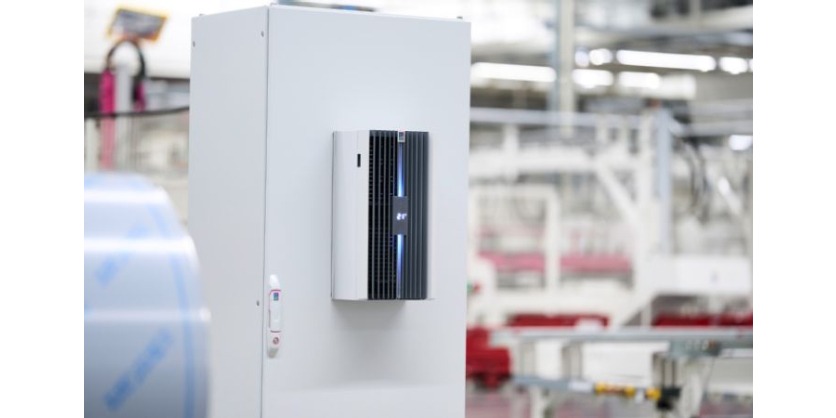
Introduction
The push towards sustainable manufacturing is driving the need for efficient enclosure cooling units, especially in industries like automotive where consistent cooling is crucial. The challenge lies in maintaining necessary cooling outputs while adhering to eco-friendly standards.
The Blue e+ S Advantage
Rittal’s Blue e+ line has set a benchmark in industrial cooling. The new Blue e+ S takes it further with precise cooling, a smaller footprint, and greater energy savings.
Key Features of Blue e+ S
- Enhanced Cooling Efficiency: Complies with UL/CSA 60335-2-40 standards, offering lower output categories (.3 kW, .5 kW, 1 kW) without compromising on cooling.
- Innovative Technology: Utilizes heat pipe and inverter technology, reducing energy consumption by up to 75%.
- Global Compatibility: cUL approval and multi-voltage capability make it suitable for worldwide use.
How Blue e+ S Increases Cooling Efficiency
Increased regulatory standards for sustainable manufacturing like UL/CSA 60335-2-40 Standard have enhanced the importance of efficient climate systems that cut emissions and energy usage. What differentiates the new Blue e+ S from other cooling units in the quest to comply with the guidelines of the new UL Standard is the ability to provide lower output categories of .3 kW, .5 kW, and 1 kW without sacrificing adequate cooling necessary to keep enclosures at optimal operating temperatures.
Using heat pipe and inverter technology, the Blue e+ S provides robust cooling without the need for a compressor, expansion valve, or other regulating elements, thus significantly reducing the amount of energy required to run the unit — in fact, the internal fan is the only component that requires energy for use.
Depending on the thermal energy generated inside the enclosure and the current ambient temperature, targeted cooling can be achieved with only the heat pipe. To further increase efficiency, the Blue e+ S only uses additional compressor cooling if a large amount of heat needs to be dissipated from the enclosure or if the ambient temperature reaches suboptimal levels. However, when compressor cooling is required, it is actually far more energy-efficient than conventional units due to an inverter-controlled drive that automatically adjusts fan and compressor speeds depending on cooling needs.
As a result of this cutting-edge engineering, the Blue e+ S can reduce overall energy consumption by 75%. This significant decrease in energy usage also helps manufacturers facilitate more efficient and sustainable production programs.
With cUL approval and multi-voltage capability, the Blue e+ S is designed for global use to help manufacturers around the world meet the demands of more efficient, sustainable manufacturing.
Smart Technology for Sustainability
- IIoT Integration: Digital monitoring and condition reporting via the Smart Service Portal.
- User-Friendly Interface: LED displays and NFC connectivity for easy data transmission and device management.
- Predictive Maintenance: Helps avoid breakdowns and reduces energy consumption.
The new Blue e+ S is built upon a fully-integrated IIoT interface that allows for digital monitoring and condition reporting to help manufacturers better understand the state of their cooling units on a 24/7 basis. The Blue e+ S easily connects Rittal’s new Smart Service Portal, where available, for remote monitoring and reporting and new LED displays make cooling unit alerts and notifications more noticeable than ever before.
Additionally, you can connect your smartphone to the enclosure cooling units via Near Field Communication (NFC) to transmit device data and parameters or scan the product QR code to see all relevant product information. The Scan & Service app is available on the App Store and Google Play. With NFC at your disposal, you’ll have:
- Faster parametrisation and commissioning of your cooling units
- Time-efficient working with Fast-Copy, allowing you to copy settings 1:1 to other cooling units
- Ability to generate and send service messages
- Capability to generate and send wish lists of accessories and spares
- All product information at a glance
- Ease of managing scanned products
This emphasis on smart technology and digitalizing climate control systems is key to prioritizing predictive maintenance in order to avoid costly breakdowns and downtime. In addition, predictive maintenance also helps better identify cooling units that need repair or replacement before failing units significantly impact energy consumption and costs. When maintenance is required, the streamlined design and engineering of the Blue e+ S means standard tools are all you need to quickly and easily get your cooling unit back online.
Environmental Impact
- Reduced Carbon Emissions: Uses a refrigerant with 56% lower Global Warming Potential (GWP).
- Compact Design: Smaller size for flexible factory floor configurations.
The technological evolution with the Blue e+ S also manifests in significant cuts in carbon emissions. Whereas other industrial cooling units rely on refrigerants containing environmentally harmful chemicals, the Blue e+ S uses a refrigerant with a Global Warming Potential (GWP) that is 56% lower than those used in comparable cooling units to minimize carbon dioxide emissions.
Plus, the Blue e+ S is smaller and more compact than previous incarnations of Rittal cooling units to help manufacturers reduce their automation footprint and achieve more flexibility in factory floor configurations. This makes the Blue e+ S ideal for retrofitted manufacturing facilities as well as seamless integration with existing industrial enclosure systems.
Conclusion
The Blue e+ S cooling units represent a significant advancement in industrial cooling technology, combining precise cooling capabilities with a reduced automation footprint. By leveraging innovative technologies such as heat pipe and inverter technology, these units achieve up to 75% energy savings, making them a cornerstone for sustainable manufacturing practices.
The integration of smart technology, including IIoT interfaces and predictive maintenance features, ensures that manufacturers can monitor and manage their cooling systems efficiently, reducing downtime and maintenance costs. The use of a refrigerant with a 56% lower Global Warming Potential further underscores Rittal’s commitment to environmental sustainability.
Moreover, the compact design of the Blue e+ S allows for flexible factory floor configurations, making it ideal for both new installations and retrofitted facilities. With global compatibility and compliance with stringent standards like UL/CSA 60335-2-40, the Blue e+ S is poised to meet the diverse needs of manufacturers worldwide.
In summary, the Blue e+ S cooling units not only enhance operational efficiency and sustainability but also provide a robust solution for the evolving demands of modern manufacturing. By adopting these advanced cooling units, manufacturers can achieve significant energy savings, reduce their carbon footprint, and ensure optimal operating conditions for their industrial enclosures.
More Information
Related Story
Blue e+ Fan-and-Filter Unit: More Power for Your Enclosure Cooling
Rittal Blue e+ fan-and-filter units help you to achieve your climate goals while at the same time reducing your energy costs. The 40% greater air throughput of the new fan-and-filter unit with pleated filter – compared to a chopped-fibre filter – is unrivalled by any other unit on the market.