Emerson’s New Analytics Software Automates Utilities Monitoring and Reporting for Clean-in-Place Applications
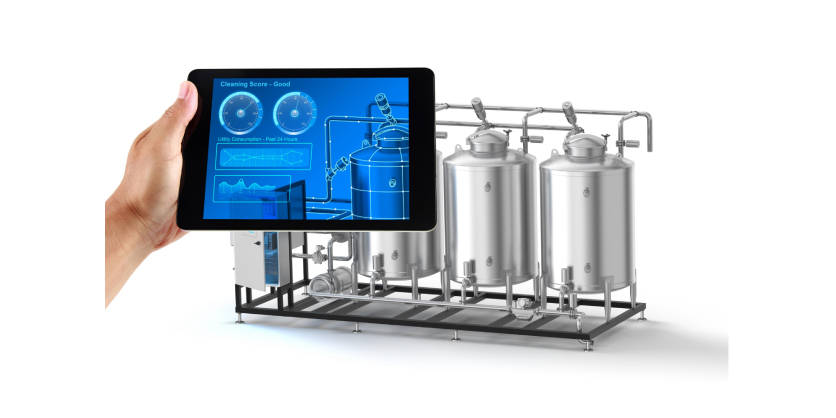
November 24, 2022
Recently Emerson announced the release of its new analytics software Clean In Place (CIP) Utilities and Automated Reporting Analytics package delivered via PACEdge™ and Movicon™ platforms on an industrial edge control device. The software aids in digitally transforming manual and semi-automated systems by optimizing utilities consumption, benchmarking against known cycles and generating automated reports that can be used to reduce energy consumption and improve productivity in a single system or throughout a facility.
The CIP Utilities & Automated Reporting Analytics package combines Emerson’s deep application expertise and industry knowledge with advanced technology to convert process and utilities data into actionable insights for the food and beverage industries and other environments that use clean- and steam-in-place operations.
Equipped with the data and analytics provided by the software, plant managers, operators and maintenance personnel can view the information on a dashboard and share the insights with sustainability officers and other stakeholders to optimize their CIP cycles. The software package can be customized and layered into an existing system, or Emerson can provide a turn-key solution of hardware, instrumentation, valves and analytics.
Central to food and beverage production, clean-in-place systems clean and sanitize internal piping, tanks and machines between product batches to help facilities meet government regulations and guarantee product quality and safety. CIP skids that don’t have sensors and analytics software in place require manual reporting, which can be time-consuming and susceptible to errors, especially when data is transferred by hand into reports. These skids may also run at unnecessarily long preset cycles and use more time and resources than required for effective cleaning.
Digitally transformed and optimized CIP processes, in comparison, only use the time, media, water, energy and labor required for effective cleaning, significantly reducing waste and increasing production time.
“Food and beverage manufacturers typically spend about 30% of utility costs on clean-in-place operations. They also lose time between changeovers and spend between 20 to 40 thousand dollars in labor costs for manual reporting,” said Amit Patel, director digital transformation for discrete and industrial at Emerson. “Emerson’s new CIP Utilities and Automated Reporting Analytics software package collects and analyzes data in real time and presents it as a report, equipping plant managers, CIP operators, maintenance personnel and sustainability officers with the actionable insights to optimize wash cycle settings, including duration and media use, for maximum efficiency and productivity.”
The CIP Utilities & Automated Reporting Analytics software package can help CIP operators better understand and forecast energy use, water consumption and resource needs. Generated reports can be used to satisfy regulation compliance, plan system maintenance, schedule downtime and order media supplies, and deeper analytics can be used to identify insights and trends that support predictive maintenance schedules and facilitate standardization of CIP processes across production facilities.
The agnostic software is compatible with any CIP equipment, which empowers manufacturers to control the digitization of their systems no matter what stage of the digital transformation journey they are in and to integrate any or all Emerson components and customize the solution for their needs.
To learn more, click here