Danfoss: VLT AQUA Drive FC 202
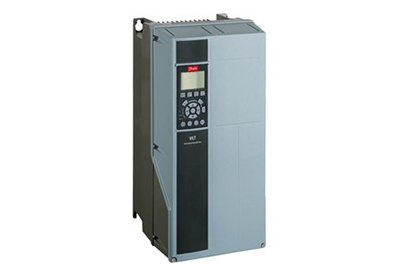
February 7, 2019
The VLT® AQUA Drive is designed to provide the highest level of performance of AC-motor-driven water and wastewater applications. Featuring a wide range of powerful standard features, which can be expanded with performance-improving options, the drive is equally suited to both new and retrofit projects.
The VLT® AQUA Drive FC 202 is designed to provide the highest level of performance of AC-motor-driven applications. Featuring a wide range of powerful standard features, which can be expanded with performance-improving options, the drive is equally suited to both new and retrofit projects. The new generation VLT AQUA Drive can realistically offer first-year cost savings of between 10–30% compared to traditional drive solutions. Its high lifetime availability and low energy consumption and maintenance costs provide you with the lowest cost of ownership. The quick and user-friendly setup reduces installation time ensuring a fast route to maximum energy efficiency and motor control. By collecting the most important parameters in one place, the risk of incorrect configuration is reduced significantly.
Water and Wastewater Applications
The considerable daily load variation in water or wastewater treatment plants makes it economically feasible to introduce motor control on rotating equipment such as pumps and blowers.
Industrial VT Applications
The VLT® AQUA Drive the perfect match for Industrial VT applications including fans, pumps, blowers, and compressors. It is a direct replacement for the FC 322. Available in a wide range of industrial enclosures from protected chassis to IP 66 (NEMA 4 X Indoor).
Supply voltages and power range
- 1 x 200-240 V…1.1-22 kW
- 1 x 380-480 V…7.5-37 kW
- 3 x 200-240 V…0.25-45 kW
- 3 x 380-480 V…0.37 kW – 1 MW
- 3 x 525-600 V…0.75-90 kW
- 3 x 525-690 V…1.1 kW – 1.4 MW
Low harmonic drive
- 3 x 380-480 V…132-450 kW
12-pulse drive
- 3 x 380-500…250-1000 kW
- 3 x 525-690…250-1400 kW
Features and benefits
Assets are protected thanks to specially designed software that prevents, for example, water hammering
Energy efficiency is maximized as a result of the drives control algorithms and design which focus on reducing heat loss
High energy savings related to air conditioning are ensured due to the unique back-channel-cooling concept that transfers 90% of heat away from the room
Electromagnetic interference and harmonic distortion are reduced thanks to the built-in, scalable RFI filter and integrated DC link chokes
Perfect system integration and adaptation to the application are possible due to freely programmable warnings and alerts
3–8% energy savings are achieved as a result of Automatic Energy Optimization