Comau Showcased Advanced Material Handling and Integrated Robotics Solutions at the Annual Rockwell Automation Fair
December 4, 2023
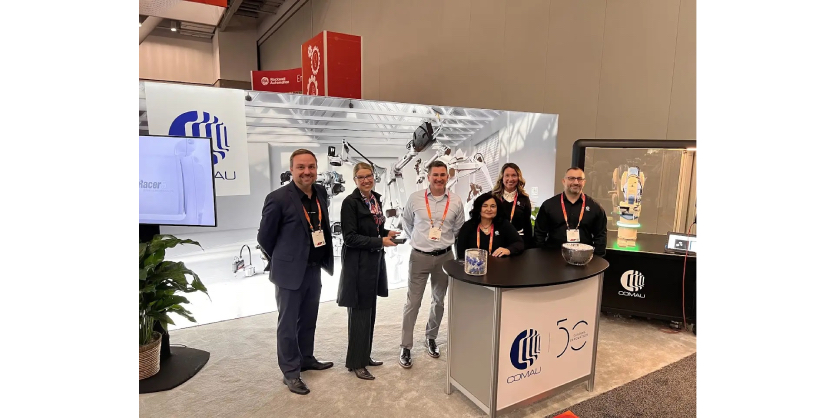
Comau joined Rockwell Automation at its 32nd annual Automation Fair®, November 6 – 9 in Boston, Massachusetts, (BOOTH #282) to highlight the full integration of its high-performance articulated robots and advanced vision systems with Rockwell Automation’s unified robot control platform.
Comau-Rockwell Automation integrated solutions, which will be on display by systems integrators and distributors throughout the show, allow companies of all sizes to control one or more robots via their existing PLC environment. This both eliminates the need for a dedicated controller for every robot and allows operators to drive even the most seemingly complex applications with the same PLC running in other parts of the operation.
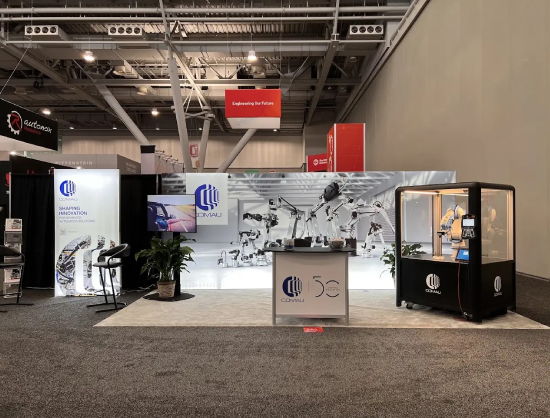
In tandem, Comau has automated a complex and nonlinear picking process in an open and intuitive way. Visitors at the Comau Booth could find an automated picking system that autonomously recognizes, locates and grasps randomly placed objects. Leveraging its Racer5 and MI.RA/3D enhanced vision system, Comau’s material handling application can automatically and accurately detect and distinguish between various parts, picking them from anywhere in the cell. These types of advanced industrial robotic systems allow companies faster, simpler access to streamlining their processes, improving their flexibility and minimizing production losses.
Since launching their collaboration in mid-2021, Comau and Rockwell Automation have worked to leverage the power of advanced robotics to increasingly help businesses maximize their manufacturing efficiencies through unified robot control solutions. The seamless integration of Comau’s robots and the PLC lets companies easily design and control their robot lines using a common programming environment. Furthermore, the optimized connectivity achieved due to the perfect synchronization of the robots, processes, workflows and peripherals allows these companies to enjoy increased production rates, faster deployment times, better resource allocation and increased sustainability.
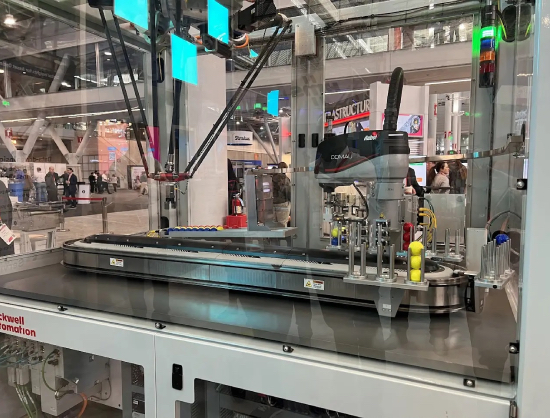
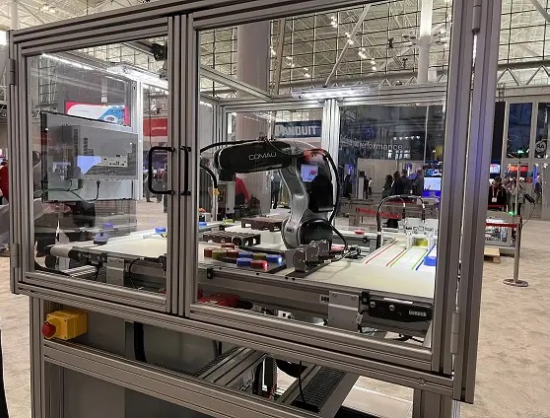
About Comau
Comau, a Stellantis company, is a worldwide leader in delivering sustainable advanced automation solutions. With 50 years of experience and a global presence, Comau is helping companies of all sizes in almost any industry leverage the benefits of automation. Backed by a continuous commitment to designing and developing innovative and easy to use technologies, its portfolio includes products and systems for vehicle manufacturing, with a strong presence in e-Mobility, as well as advanced robotics and digital solutions to address rapidly growing markets in industrial sectors.
The company’s offering also extends to project management and consultancy. Through the training activities organized by its Academy, Comau is committed to advancing the technical and managerial knowledge necessary to face the challenges related to automation and leverage the opportunities of a constantly changing marketplace. Headquartered in Turin, Italy, Comau has an international network of 5 innovation centers, 5 digital hubs, and 12 manufacturing plants that span 13 countries and employ 3,700 people. Together with its wide network of distributors and partners, the company is able to respond quickly to the needs of its customers, no matter where they are located throughout the world.
More Information
Related Story
Comau Powers The Efficient Automation Production Of Next-Generation Electric Drive Systems For NIO
Comau has implemented a high-performance turnkey solution to automate manufacturing of NIO’s next-generation electric drive systems. The multi-faceted project also ensures fast and reliable co-line production for the electric vehicle manufacturer’s third-gen induction and permanent magnet motors, both of which are integral parts of its proprietary electric drive systems (EDS). The comprehensive solution includes primary lines such as e-motor assembly lines, gearbox manufacturing and inverter assembly lines, as well as EOL (End of Line) testing processes. It is designed to support a large-scale annual production capacity of 1 million units, to be used within NIO’s electric sedans, coupes and SUVs, as well as select models of its sub-brand ALPS.