CODI Manufacturing Designs and Built New Case Packer in Four Weeks with Festo Engineering Tools and Assembly Services
November 21, 2024
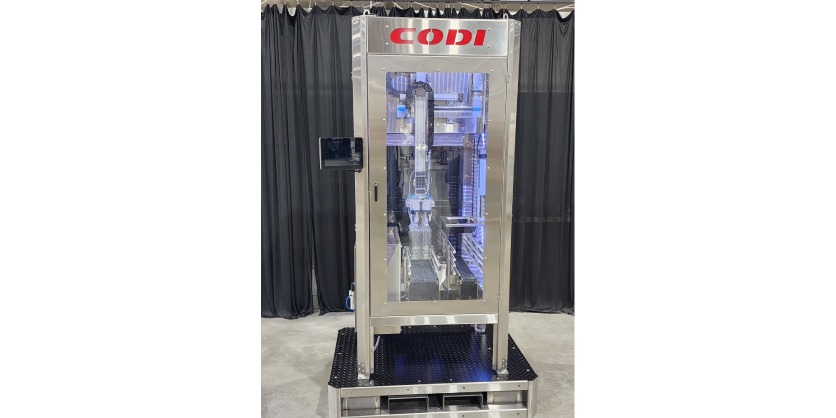
CODI Manufacturing’s new compact, flexible 12-cycle-per-minute case packer for small to mid-sized food and beverage companies achieves an industry leading price/performance ratio. The Littleton, CO-based machine builder utilized the Festo Handling Guide Online (HGO) engineering tool to design the two-axis handling system, the core of the new machine’s package handling. By having Festo assemble and ship a bolt-in-ready handling system, the company was able to build and commission the new machine in just four weeks.
“This machine is incredibly flexible,” said Jared Jones, Chief Operating Officer, CODI Manufacturing. “All the end user has to do is swap out the gripper head to change the number, type, and size of bottles, cans, jars, or pouches being packed into shipping cases, select a new recipe on the HMI, and start the machine.”
The CODI design features some of the latest Festo componentry throughout:
- New multiprotocol CMMT-AS servo drives and matching EMMT-ST one-cable motors
- New CPX-AP-A configurable remote I/O terminal
- New VTUX valve terminal
- A simplified motion series (SMS) low-cost electric-linear actuator
- The CDPX IP67 machine mounted HMI
- Festo robust linear axes
- The Festo CPX-CEC controller with EtherCAT communications for advanced motion control.
Collaboratively, Festo Engineering and CODI developed a pneumatic gripping head that provides feedback on successful gripping of each bottle. “Customers are amazed at the advanced motion automation technology on this machine for the price point,” Jones said. “It’s striking how much state-of-the-art automation is packed into such a small footprint machine.” CODI Manufacturing had wanted to build a compact case packer for small to mid-sized companies for several years.
Recently, CODI was four weeks into an eight-week project when Jones and the customer discussed adding a case packer to the order. “When I mentioned a price, the customer said he’d buy the machine if we could deliver it in four weeks with the rest of his order,” recalled Jones. “I said we’d try.”
The design session took minutes, saving CODI several days of engineering time
The core of the machine would be a two-axis handling system used to grip and lift six bottles off one conveyor and place them into a box on an adjacent conveyor. The CODI team used the Festo HGO engineering tool to specify the system where the axes, servos, motors, mounting plates, and accessories were all properly sized and interoperable. The design session took minutes, saving CODI several days of engineering time.
“One of my lead controls engineers came into my office and said that Festo would supply a bolt-in-ready handling system at basically the same cost as buying and assembling the pieces and parts,” Jones said. “There was simply so little price difference between assembled and unassembled that we went with assembled. We used CAD files from the HGO session to build the frame while we waited for the assembly. Three weeks later, the system arrived. We used eight bolts to attach it to the machine frame. For a multiple-axis system, this was the easiest and fastest assembly and commissioning we’d ever had and the lowest total cost.”
Festo at a glance
Festo, the world’s leading supplier of automation technology and technical education, is deploying its products and services to meet the challenges of digitization and smart production. Founded in 1925, the family-owned company based in Esslingen, Germany supports a wide range of needs for advanced solutions in factory and process automation. In Canada,
Festo has been supporting Canadian industry for almost 50 years, continuously elevating the state of manufacturing in this country with innovative products, optimized motion control solutions and unrivalled support. Globally, some 300,000 customers put their trust in the company’s pneumatic and electric drive products and technology. In addition, Festo Didactic provides state-of-the-art training equipment and educational programs for industrial companies and educational institutions – about 56,000 customers worldwide. The Festo Group registered sales of €3.65 billion in the 2023 financial year and is represented worldwide at 250 locations with about 20,600 employees. About 7.7% of its annual turnover is invested in research and development.
More Information
To learn more about CODI’s custom machine building capabilities in the food and beverage industry, visit www.codimfg.com. For more information on the advantages of working within the Festo ecosystem of less engineering overhead, fast time to market, seamless connectivity, and high-quality components, visit www.festo.com Handling Guide Online (HGO) web page for more information and video and the HGO brochure.
Related Story
New Festo Canada Program Helps End Users Find System Integrators for Automation Projects
For end users wanting to incorporate more automation in their operations but lacking the in-house capability to make it happen, Festo Canada has a solution to overcome that barrier. The company’s new Certified System Integrator Program will match an end user with highly skilled system integrators, providing the validated know-how and expertise to turn the aspirational into the realizable.