Beckhoff’s TwinCAT Automation Software
June 12, 2024
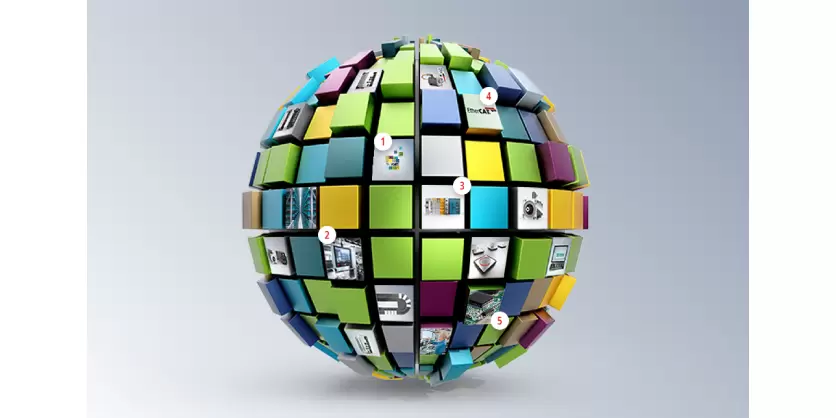
The world of TwinCAT: Open, PC-based control technology
When Beckhoff launched its PC-based control technology, it created a global standard for automation. In terms of software, the core of the control system has taken the form of The Windows Control and Automation Technology – or TwinCAT – automation suite since 1996. In combination with TwinCAT, the Beckhoff portfolio results in optimally coordinated automation concepts that fulfill the basic principles of an open and highly scalable control system.
TwinCAT transforms almost any PC-based system into a real-time control complete with multiple PLC, NC, CNC, and/or robotics runtime systems. The possibility of modular extensions means functional changes and additions can be made at any time. If required, the openness of the control system allows not only the integration of third-party components, but also customized retrofit solutions for existing machines and systems. This ensures flexibility and investment protection for the customer.
TwinCAT 3: The flexible software solution for PC-based control
With TwinCAT 3, the latest version of the software, the Beckhoff portfolio results in optimally coordinated automation concepts that fulfill the basic principles of an open and highly scalable control system.
TwinCAT 3 follows on logically from TwinCAT 2 as the latest development in the series, which is already redefining the world of automation technology as we know it. The way the complete control intelligence is implemented on a single software platform, divided into engineering and runtime, still represents the basis of the system.
What’s more, both engineering and runtime can be flexibly extended by application-specific software modules, known as Functions, so that the TwinCAT system can be perfectly adapted to suit individual requirements.
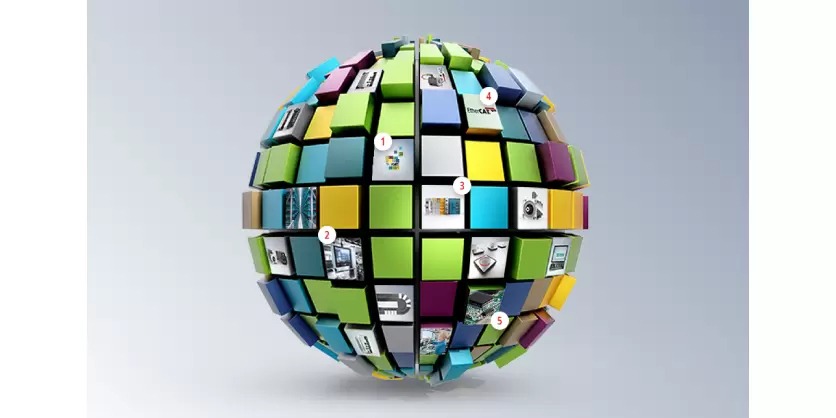
Structure of TwinCAT 3
Engineering
TwinCAT XAE (eXtended Automation Engineering) allows hardware to be programmed and configured in a single engineering tool. In addition to the IEC 61131-3 programming languages, C/C++ and MATLAB®/Simulink® are also available for programming. The tool even offers integrated debugging options for the program code and diagnostic functionalities for the control hardware. Functions are available to flexibly extend the basic engineering to include additional functionalities such as a software oscilloscope.
Runtime
TwinCAT XAR (eXtended Automation Runtime) is a real-time-capable runtime in which the program code can be executed to control the field level of the machine. The modular architecture makes it possible to install and load extensions on an application-specific basis in the form of functions. In addition to the actual real time, which is executed independently of the operating system, an operating system always runs on the PC-based controls, which also enables other programs to be executed. This means the control platform can also be used for tasks such as visualizing or executing customer-specific software.
TwinCAT 3 Functions
TwinCAT is a modular system that can be put together on a project-specific basis to suit individual requirements. In addition to the actual engineering and control system itself, this modularity is mapped via over 100 Functions, which are assigned to different subject areas.
The TwinCAT Functions extend the basic system in areas such as motion and safety individually depending on the application. Measurement or, for example, a TwinCAT HMI-based user interface are modules that interact seamlessly with the actual machine control via a uniform interface. When it comes to supporting additional communication protocols such as OPC UA, users can simply install the corresponding module at a later stage as required. Even the latest Functions, such as those from the fields of machine learning or vision, can be retrofitted to existing systems in the same way.
Advantages of TwinCAT 3
In addition to the basic principle of simplification, which applies to TwinCAT 3 from the engineering process and runtime to transparent cost representation, the automation software also offers a whole host of other outstanding features:
- Maximum flexibility: TwinCAT 3 enables hardware-independent development of the application: from small, ARM-based controls to many-core CPUs. When it comes to programming the real-time control software, a flexible choice can be made between the IEC 61131-3 programming languages, C++, and MATLAB®/Simulink®.
- Efficient project planning: The modular architecture of TwinCAT facilitates the reuse and maintenance of software components. Reusable structured program code can be generated on the basis of object-oriented programming. Communication between modules is also easy to implement via a standardized data exchange, so that the modules can be flexibly combined with each other in the IEC 61131-3 programming languages, C++, or MATLAB®/Simulink®.
- Free choice of interfaces: TwinCAT 3 provides a wide range of interfaces, which facilitates a connection to the IT world from databases to cloud systems via OPC UA and other protocols. The existing protocols can be extended with customer-specific adaptations. Beckhoff also supports all common fieldbus systems, which allows it to react flexibly to requirements in the fieldbus area.
- Fair pricing: TwinCAT 3 Engineering is available free of charge with basic functionality. The TwinCAT Runtime environment used to execute the control code can also be trialed on a renewable 7-day license. For permanent operation, a license model applies depending on the performance of the hardware used. In terms of support, this is available free of charge to all customers worldwide.
- Sound investment: TwinCAT 3 has been available on the market since 2010, and the software is constantly being further developed with innovative technologies such as image processing and machine learning. Projects created in the previous version can still be migrated today using a converter. This ensures that the expertise from older projects can continue to be exploited in new versions and expanded with the latest functionalities.
Related Story
Precise Machining of Small Parts with TwinCAT CNC
Producing large parts with precision is not easy. But how do you produce the smallest components, such as gears and screws for the watch industry or contact pins for connectors, with micrometer-level accuracy and in large quantities? Swiss companies Esco and Affolter achieve this feat in their CNC machines with TwinCAT CNC and servo drive technology from Beckhoff.