ABB Introduces ABB Ability™ Smart Hoisting to Take Mine Hoist Performance and Reliability to the Next Level
January 15, 2024
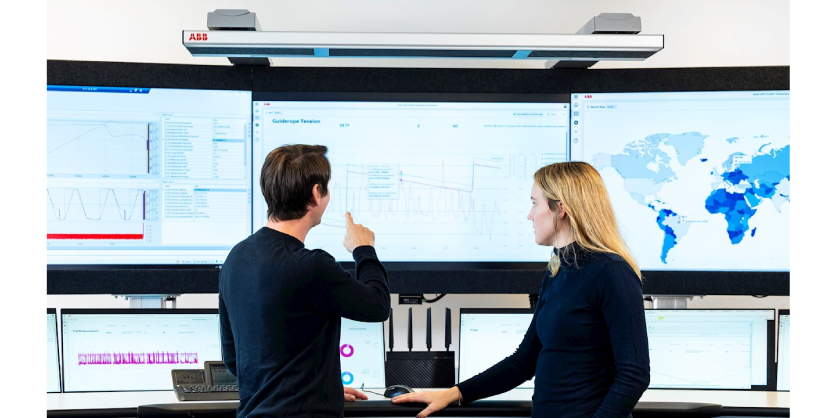
- ABB is launching a new version of its digital monitoring and optimization suite to improve the performance and reliability of mine hoists
- ABB Ability™ Smart Hoisting ensures that customers can improve uptime, availability and productivity of their equipment with actionable insights on key performance indicators
- Customers will benefit from a new era of mine hoist condition monitoring and performance optimization
ABB Ability™ Smart Hoisting ensures that customers can improve uptime, availability and productivity of their equipment with actionable insights on key performance indicators
ABB is launching a new digital suite of applications for hoist monitoring and optimization, now rebranded to ABB Ability™ Smart Hoisting, which opens it up for further integration to other cloud solutions and extended offerings that significantly increase the operational performance and reliability of mine hoists.
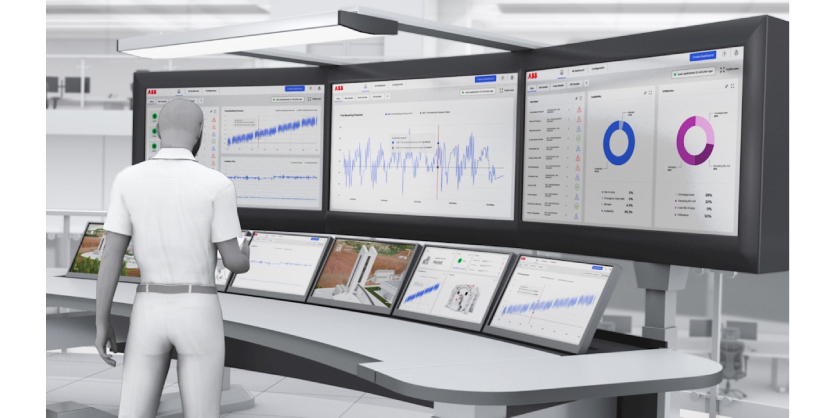
The new digital suite is an important milestone in the company’s ambition to transform predictive maintenance for mine hoists. With new features such as ABB Drive System Monitoring and new key performance indicators (KPIs), ABB is opening the door to an entirely new level of mine hoist optimization services for customers.
The traditional predictive maintenance approach relies on manual data collection and analysis over a short period of time. Intermittent issues can stay hidden or only be identified later, giving subject matter experts (SMEs) little time to program interventions exactly when needed. Additionally, manual collection and data analysis consume a significant amount of time for SMEs, preventing them from focusing on strategic performance management tasks.
ABB Ability™ Smart Hoisting is designed to significantly improve the uptime, availability, reliability, performance and productivity of hoists. By incorporating advanced monitoring features, the system provides actionable information on critical KPIs, ensuring better decision-making and optimization of hoisting operations. The automatic collection, monitoring and analysis of data will enable mining companies to increase production performance, identify potential functional safety hazards and optimize maintenance scheduling.
The combination of innovative features and improved cyber security makes this solution a unique and valuable tool in the underground mining industry. Its predictive maintenance capabilities help increase standards and drive innovation, leading to more sustainable and profitable mining operations.
Improved productivity in mining operations can lead to increased economic growth, job creation, and overall regional development. Additionally, proactive maintenance and hazard identification contribute to a safer and more environmentally responsible mining sector.
“The new and enhanced Smart Hoisting solution offers a step change in the operational performance of mine hoists,” said Charles Bennett, Global Service Manager, Hoisting at ABB. “From improved uptime, reduced environmental footprint and increased monitoring services, this new solution brings enormous benefits to the industry at an important time.”
Charles Bennett, Global Service Manager, Hoisting at ABB
“Through the integration of predictive maintenance and advanced monitoring, the evolved ABB Ability Smart Hoisting solution marks a pivotal milestone in redefining the performance benchmarks for mine hoists. This transformative solution addresses industry challenges comprehensively, fostering heightened uptime, sustainability and operational resilience.”
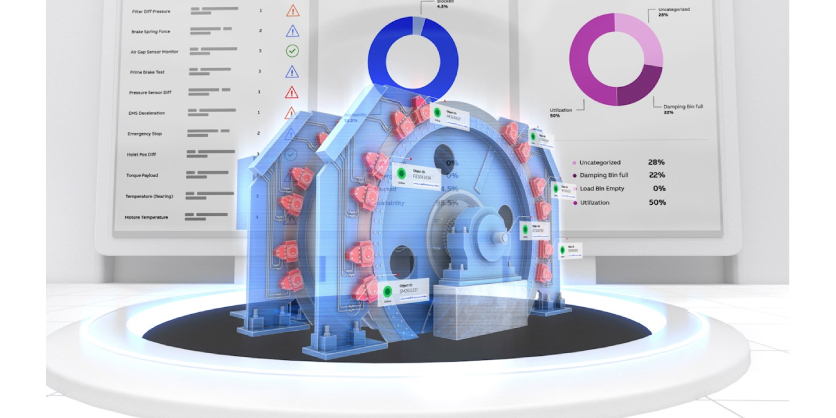
The key features of the new Smart Hoisting solution include:
- Predictive maintenance: The Smart Hoisting solution serves as a predictive maintenance tool, allowing customers to proactively identify and resolve potential issues before they escalate. This reduces downtime, increases operational efficiency, and minimizes maintenance costs
- Advanced monitoring capabilities: The solution includes Drive System Monitoring, and KPIs that provide actionable insights for better decision-making and optimization of hoisting operations
- Enhanced cyber security: With improved cyber security measures in place, ABB ensures the safety and integrity of customers’ mining operations, protecting them from potential cyber threats and vulnerabilities.
- Comprehensive solution: The Smart Hoisting solution addresses multiple customer challenges simultaneously, from increasing uptime and performance to ensuring safety and efficient maintenance scheduling. By providing a holistic approach to mine hoist optimization, ABB empowers customers to achieve better results, save time and resources, and ultimately improve their bottom line.
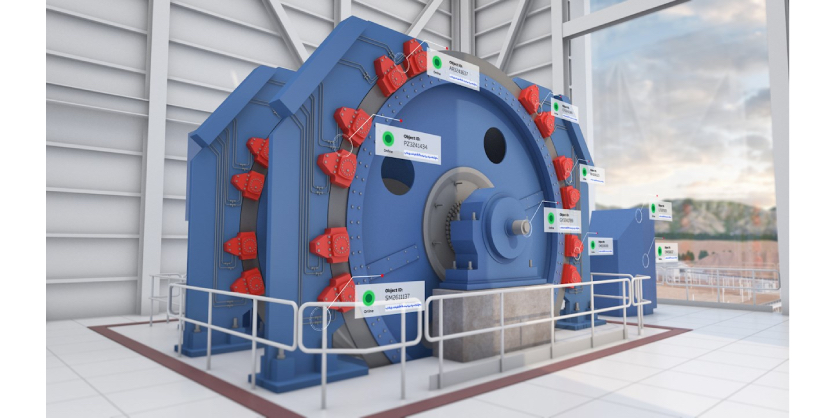
ABB has been a leader in developing world-class hoisting solutions for over 130 years. Powered by electricity with the possibility to run off renewable energy sources, hoists are very much a future forward solution for enabling the sustainable transformation. To date, ABB has delivered over 1,000 hoisting solutions globally. As a supplier of complete mine hoist systems, customers can benefit from low life cycle cost, high reliability and system availability, short project execution time, and a single source of supply for complete systems, including service and spare parts.
ABB’s Process Automation business automates, electrifies and digitalizes industrial operations that address a wide range of essential needs – from supplying energy, water and materials, to producing goods and transporting them to market. With its ~20,000 employees, leading technology and service expertise, ABB Process Automation helps customers in process, hybrid and maritime industries improve performance and safety of operations, enabling a more sustainable and resource-efficient future. go.abb/processautomation
ABB is a technology leader in electrification and automation, enabling a more sustainable and resource-efficient future. The company’s solutions connect engineering know-how and software to optimize how things are manufactured, moved, powered and operated. Building on more than 140 years of excellence, ABB’s ~105,000 employees are committed to driving innovations that accelerate industrial transformation.www.abb.com
More Information
Related Story
ABB and Gravitricity to Collaborate on Energy Storage Systems Using End-Of-Life Mine Shafts and Hoist Technology
ABB has signed an agreement with UK-based gravity energy storage firm Gravitricity to explore how hoist expertise and technologies can accelerate the development and implementation of gravity energy storage systems in former mines.