Siemens Leads the Way with Sustainable Stainless Steel for Medium-Voltage Switchgear
January 8, 2024
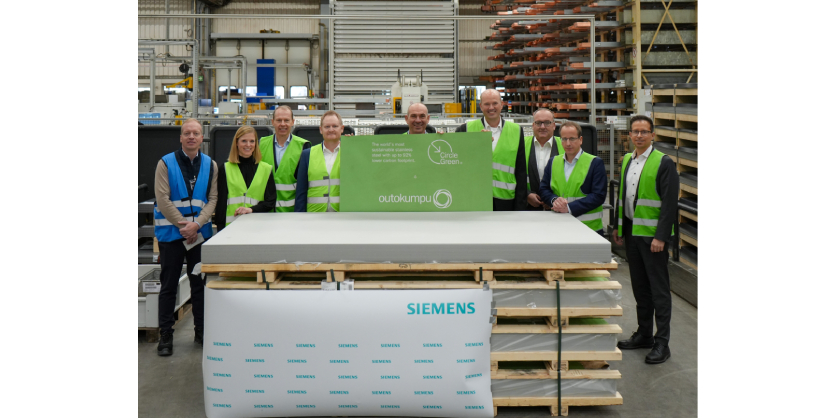
- Outokumpu to provide steel with a 93% lower carbon footprint for Siemens’ medium-voltage switchgear
- Takes delivery of towards-zero stainless steel at its Frankfurt switchgear factory
- Demonstrates clear commitment to the reduction of supply chain emissions
Underpinning its commitment to making sustainability a key priority within its operations, Siemens Smart Infrastructure has taken delivery of sustainable stainless steel at its Frankfurt switchgear factory. Recognizing that the urgent need for decarbonization and increased electrification requires sustainable solutions, Siemens is committed to using sustainable steel for medium-voltage switchgear. With plans to not only integrate the product at other locations but also to include second-tier suppliers in this sustainable approach, Siemens is prioritizing sustainability within its own operations, while also fostering a broader network of environmentally conscious practices across its supply chain.
Provided by Outokumpu, a global leader in sustainable stainless steel, Outokumpu Circle Green® steel delivers an up to 93 percent lower carbon footprint than the industry average. To produce this sustainable steel and achieve such a significantly reduced carbon footprint, 100 percent low-carbon electricity is used, alongside low-carbon raw materials, such as recycled steel.
“As industries around the world look to reduce carbon emissions to reach ambitious net-zero targets, sustainable steel has a huge potential. In Outokumpu we have found an organization dedicated to accelerating the industrial decarbonization of stainless-steel production,” said Stephan May, CEO of Electrification and Automation at Siemens Smart Infrastructure. “By utilizing sustainable materials in our Electrification and Automation portfolio, we are frontrunners in driving a responsible approach to industry progress.”
Stephan May, CEO of Electrification and Automation at Siemens Smart Infrastructure
Steel manufacturing produces more CO2 than any other heavy industry, comprising around 8 percent of total global emissions. With population growth and the resulting increased demand for energy, the demand for steel is also set to increase. However, if all stainless steel were to be produced with the same methods used for Circle Green production, it would reduce global carbon emissions from the stainless steel value chain by 364 million tons per year. This equates to over 900 million one-way flights from London to New York.
“The surge in global population will lead to rising energy demand and urbanization – affecting the need for steel across various industries and calls for sustainable materials and circular solutions. We are at the forefront of decarbonizing the stainless steel industry and the energy sector is one of many where action is needed. By transitioning to renewable energy and investing in low-carbon technologies and materials today, companies can significantly mitigate the effects of climate change. Our solution, Circle Green, enables green energy transition and we are proud to join forces with Siemens, who sets an example for a low-emission future,” says Niklas Wass, President, Stainless Europe business line, Outokumpu.
Niklas Wass, President, Stainless Europe business line, Outokumpu
More Information
For more information on Siemens Smart Infrastructure, please see:
Siemens Smart Infrastructure
Related Story
Siemens Expands Sustainable and Digital Switchgear Range for Primary Distribution Up To 24kV
Siemens Smart Infrastructure has expanded its range of sustainable and digital medium-voltage switchgear to support the decarbonization of today’s power grids. The new F-gas-free blue GIS primary switchgear enables an early transition to sustainable grids ahead of regulation. With a focus on industrialized and high-end ratings up to 24kV and 2500A, Siemens has launched the 8DAB 24 and upgraded the NXPLUS C 24.