History of Harting: After Six Decades, Wilhelm Harting’s Invention Keeps Getting Better
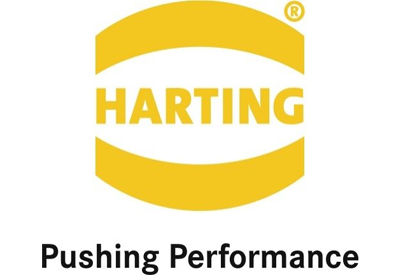
Few industrial innovations have weathered the years as well as heavy duty connectors. What was revolutionary in 1950 is an indispensable part of machine and plant design today. Legacy models continue to serve users remarkably well while the newest ones deliver important additional benefits.
Connectors’ evolution tracks that of machine design
The rectangular connector made its debut almost 65 years ago, reflecting a growing trend in machine design at the time and starting one of its own. Machines were becoming increasingly complex. No longer was machine control just a matter of plugging a power cord into an electrical outlet and flipping the on/off switch. Manufacturers were developing more elaborate power distribution and control systems and locating critical components in control cabinets outside the machine. Connectors provided a logical bridge between the cabinet and subsystems inside the machine. Few connectors were accepted as rapidly as the first rectangular connectors, embraced by the electrical and mechanical engineering communities and machine-builders alike.
The concept has evolved considerably since 1950 when Wilhelm Harting and his engineers invented the rectangular connector, forerunner of the first Han® hoods and housings. His primary objective was to develop a universal, high performance connector for all application areas. Taking the existing connector technology with its limited utility, he increased the number of contact pins, replaced the existing contacts with male and female plug-in contacts and expanded termination technology with screw-type and crimp techniques.
Since then, industrial connectors have enjoyed over six decades of continuous improvement. Today, they are more relevant than ever, with their proven reliability and cost advantages over point-to-point hardwiring of machinery. For engineers, connectors provide unrivaled flexibility in machine layout to pursue modular concepts or to merely optimize wire routing and space utilization. For machine builders, they offer time and cost savings over hardwiring in prototyping, assembly, testing and installation in the field. Every step is much faster with plug-and-play connectors. For the OEMs’ customers, connector-based wiring greatly accelerates maintenance, providing a lower total cost of ownership than hardwired systems. Connectors also improve the business case for renewing or upgrading older machines by reducing the labor cost and downtime involved.
HARTING synonymous with connectors
The HARTING Technology Group is a global connectivity giant, still owned and managed by Wilhelm Harting’s descendants, with 11 manufacturing facilities in six countries and subsidiaries and branch offices in 40. In the interest of maintaining stringent quality control, HARTING manufactures most of its connector content. That kind of commitment has made it the world leader in heavy duty connector sales. While the company has diversified into device and PCB connectivity, Ethernet and other networking solutions, RFID, 3D Molded Interconnect Device technology (MID), smart energy management and other future-looking technologies, industrial connectors remain its core business.
.
HARTING’s new connector products tend to be trend-setters in industrial design and automation. The company continues to expand its portfolio with new user-friendly models for general use as well as specialty versions optimized for rugged, demanding or niche applications like high heat or corrosive operating conditions, high current-carrying requirements or clean room or other hygienic environments.
In order to maintain market leadership, HARTING spends an amount equal to about six percent of its annual sales on R&D. It holds more than 900 patents/registered designs and 300 trademarks. With the expiration of older patents, some of its innovations end up being “adopted” by competitors. HARTING has been responsible for so many innovations in connectors and termination options that its products dominate the European market and are well-known elsewhere. In Europe, Han® is used as a noun, like Coca-Cola® or Kleenex®, another way of saying “heavy duty connector”. HARTING connectors are dominant in the machinery, robotic and transportation industries, from automobile assembly plants to high speed trains.
Wilhelm Harting’s original rectangular Han® connectors were followed over the years by several new housing and inserts lines: the Han A®, Han® B, Han D®, Han® M for harsh environmental requirements, Han-Drive® for motor assemblies, the external high current-carrying Han® HPR used extensively in rail and transit operations, Han® EMC for highly shielded connections and Han-Compact®. HARTING always has focused on rectangular and square industrial connectors, considering them superior to circular connectors in several respects. Rectangular and square designs can accommodate greater contact density and are especially well-suited for hybrid and modular configurations. They are more scalable than circular connectors, also less prone to misalignment and pin damage during mating of the hood and housing.
Many of these legacy Han housings and inserts, beginning with Han A in 1959, continue to serve customers well and remain available for purchase, giving users more choices. Their utility has been extended by the addition of new sizes, inserts, termination styles, modules and housing materials and surface coatings. They are available with options like Han-Easy Lock® locking levers in lieu of riveted metal levers. HARTING’s portfolio in the early years only covered modest signal and small power connections – 10 Amp up to 16 Amp contacts. Today, the catalogue spans an enormous range, from sensitive signal transmissions – microamps or milliamps – up to high power transmission, like 650 Amps/4000 volts, for passenger trains and other applications.
HARTING creates user-defined modularity
The 1990’s saw HARTING usher in the era of user-defined modularity with the Han-Modular® system (1994). The Han-Modular® system was a game-changing concept, allowing the customer to build a custom connector with standard parts. Whereas earlier hybrids like HARTING’s Han-Com® (1989) had fixed power and electronic contacts, Han-Modular® allowed customers to combine different transmission media in stock hoods and housings by populating the interface from a selection of inserts. Users could consolidate multiple feeds which otherwise would have to be fed individually into a machine or via an expensive, custom connector solution. The introduction of Han-Modular® both catered to the emerging modular machine design approach and helped accelerate it. Machine builders could integrate sub-systems faster with modular connectors than by hardwiring them together. They could dispense with internal terminal blocks and a great deal of wiring and other cabling for significant time and cost savings in manufacturing, assembly, commissioning and maintenance.
Today, most heavy duty connectors are modular and user-configurable. Modular connectors can combine different transmission media and contact types – power, signal, D-Sub, coaxial, fiber optic, pneumatic lines or combinations thereof – in the same unit to create a high-performance, single-purpose or hybrid interface optimized for the most complex machine and plant applications. For example, one Han-Modular® hood and housing selection can integrate power inserts – up to 200 Amps or 5000 volts – as well as pneumatic hosing, data lines, shielded bus signals and optical cables made of POF or glass fiber.
Han-Modular® remains a core HARTING product line with over 40 modules and more being added each year. The modules support almost any application and when fitted in compatible hoods and housings are designed to withstand challenging ambient conditions like dirt, dust, humidity, rain, chemical wash down, large temperature swings, sunlight, impact, shock and vibration. Modules can be put together in various size hoods and housings, including any standard Han® hood using a Han® docking frame. They also can be used in the company’s newer products like Han-Eco® and Han-Yellock®, as well as in dedicated housing options like Han-Modular® Twin, Han-Modular® Compact, Han-Modular® Docking Frames for drawer systems and Han-Modular® ECO.
HARTING adds innovations for populating connectors
The expansion of the company’s connector portfolio also has reflected the invention of additional wire termination technologies, to which HARTING contributed two of its own. From soldered or screwed connections commonplace prior to the 1950s, advances have included popular choices like crimp and cage clamp. In the 1980s, HARTING introduced axial screw termination for stranded high current wires. Just a few years ago, it achieved another breakthrough with the patented tool-free Han-Quick Lock.
Screw termination always secures the wire from the side by compressing it at a 90-degree angle. Axial screw terminates a stripped wire from the mating side and is well-suited to connecting larger wires. It acts like a cone threaded into the wire that presses the individual strands against the outside of the contact chamber. With a comparatively low screw force the installer can achieve very reliable, vibration-resistant connections. Han-Quick Lock functions like a circular cage clamp, only more space-saving with its high contact density. It consists of three components: a contact with cone, spring and active termination element. The contacts are pre-assembled in those HARTING connectors offering the Han-Quick Lock option. The advantages include time savings in installation – at least 20% faster than screw termination – high vibration safety, high wire pull-out force and low contact resistance.
Each termination technology serves a purpose. Crimp is automation-friendly and produces the best quality connections but requires special tools. Where field termination is needed, screw, axial screw, cage clamp or Han-Quick Lock are preferred, depending on the application.
Blending form with additional functionality
HARTING’s early history was devoted to creating the modern heavy duty connector. Today, some of the company’s newest products are redefining it. Han-INOX (2008), the multiple award winning Han-Yellock (2010) and Han-Eco (2011) make extensive use of Han-Modular or dedicated inserts and modules, allowing customers to build single function or hybrid, value-added interfaces. Han-INOX stainless steel hoods and housings provide safety and security from aggressive environmental conditions, both indoors and out. Indoors, they meet the demanding standards of the food and beverage and other process industries where the highest level of hygiene is essential. Han-INOX targets a wide range of potential applications from proprietary sensor and actuator solutions (for example, pickups, line switches, drives) to central control systems (bus system communications). Outdoors, the corrosion resistance of stainless steel makes it a viable choice for aerospace, transportation, ship-building, mining and construction applications.
With Han-Yellock and Han-Eco, HARTING lets machine designers and builders imagine connectivity in terms never before possible. Both combine form and function in a single, compact yet sleek interface that uses Han-Modular modules and inserts. Both have their own dedicated mono-block inserts for high contact density and Han-Yellock® has its own series of multipliers, providing bus bar functionality for one up to five contacts.
Han-Yellock modules require only male crimp contacts. The two male contacts are connected using a multiplier inserted into the connector. Each electrical feed per wire can supply up to five contacts, moving the job of multiplying potentials from terminal blocks inside the machine to the Han-Yellock, saving on space and materials. Less wiring means less cost and ultimately fewer steps in manufacturing and assembly. Stranded wires can be terminated using crimp or Han-Quick Lock for easy field assembly. Han-Yellock’s internal, latched locking mechanism is revolutionary in its simplicity. The vibration-resistant locking mechanism – the yellow press button that gives Han-Yellock its name and can be opened by pressing the button – provides extremely fast and simple disconnections and re-connections. Twist the button and it’s locked securely. The housing can be populated from the front or rear so if desired, the connector can be mounted on the outside of the machine after it’s fully built.
Han-Eco mimics the distinctive, curved shape of Han-Yellock® but moves conceptually in a different direction – giving customers the choice of a lighter weight, more economical product than the traditional metal interface. The hoods and housings are made of a high performance, fiberglass-reinforced thermoplastic. Han-Eco is ideal for applications that don’t require the full range of product features offered by the standard Han series. Even so, Han-Eco can incorporate all Han-Modular® inserts, is highly resistant to environmental stress (rated IP65 when locked) and provides outstanding mechanical stability.
Customers asking for more
Until recent years, a customer’s preference in connectors was largely driven by capability and sticker price. Now, some customers are asking for more – like more application-specific and even customer-specific solutions, and increasingly, aesthetic appeal. The emphasis on aesthetics is reflected in the distinctive design of Han-Yellock and Han-Eco. An increasing number of machinery OEMs want to differentiate themselves from their competitors’ products. They want the connector, affixed to the outside of the machine, to enhance its visual appeal rather than detract from it. HARTING product designers now consider connector aesthetics from the earliest stages of the development process.
Another customer-driven trend is the development of outdoor derivatives of popular heavy duty connectors. Some customers had such a high regard for the unique capabilities of the Han-Yellock, like the multiplier capability or push-button mating system, they wanted to use it in outdoor applications if it could withstand exposure to factors like direct sunlight and salt spray. HARTING modified the original design accordingly to create the black outdoor IP67-rated Han-Yellock. The rugged and corrosion-resistant IP65-rated Han-Eco® already was being used successfully in many outdoor applications, but now comes in an outdoor version enhanced with special UV resistant seals and gaskets. That’s typical for a forward-thinking company that takes pride in serving the industrial community with ground-breaking products that respond to and even anticipate the needs of its customers.