Discussing AGVs with JMP Solutions’ Rob Frappier
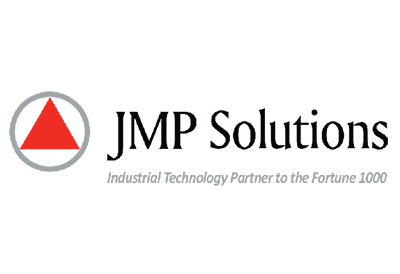
February 19, 2019
By Blake Marchand
JMP Solutions is a leader in industrial automation and technology, headquartered in London, Ontario. They have 15 business units across Canada and the United States providing engineering and turnkey solutions in process automation, control system integration, information and MES, automation and robotic systems, material handling, networking and security, and automated guided vehicles.
With respect to the latter, Drives & Control Solutions was able to table a few questions with Rob Frappier, Director of Automated Guided Vehicles and Branch Manager of JMP Solutions Control Systems Office in Cambridge, Ontario. Frappier was kind enough to take a few minutes out of his busy schedule to provide some insight into the industry and his work with JMP Solutions.
Frappier received his diploma in Robotics and Automation in 2000, returning to school in 2008 to earn his Bachelor of Science. He began his career in mechanical design for Automation Tooling Systems. Frappier said he then “switched careers to more automation, working for a local integrator on discrete applications.” Frappier added that he, “advanced through the positions quickly, then transferred to a couple of different companies gaining experience in process applications,” before ultimately settling with JMP Solutions in 2011 as a Branch Manager. He currently holds the position of Divisional Director for JMP’s AGV (Automated Guided Vehicles).
“We are doing some exciting things with AGV’s and SDV’s (Self Driving Vehicles), which is where I am focused currently.”
AGVs have been utilized since as early as 1953 – tow trucks that ran on wire tracks embedded in factory floors were the first incarnation. The technology increased incrementally over the years, with similar technology being used in the 1970’s. Solid state controls pushed automated capability beyond tow-motors, to assembly and production systems. As computing systems became smaller, more powerful and complex, technologies initially developed in the military and aerospace landscapes made their way into the industrial marketplace. And although AI, automation, IoT, and robotics have progressed significantly, even in recent years, the potential of these technologies is still being realized.
“Automation is becoming increasingly compact, easier to implement and with more features and functionality,” explains Frappier. Just like with any technological advancement, once the associated cost is brought down to a point where it can be widely utilized, manufacturers, OEMs, and service providers have more of an impetus to invest in the further research, development, and implementation.
With the current state of industry being in the midst of a new industrial revolution remaining open to continually learning and adapting with new technologies is crucial. For Frappier, when it comes to staying ahead of new technologies and trends, he said, “Our clients help us a lot. When a product or suite of products comes along that promises to be better, faster, more cost effective, our clients want to know more,” he added that, “Usually this involves a trial of some sort where we mutually invest in the training and skills required with an end goal of everybody benefitting.”
“Industry 4.0 and IoT are making connectivity as easy as plug and play. More companies are looking to do more with less for less money and that translates into taking advantage of templates, reuse, PM methodologies as well as an understanding of ROI/IRR drivers to help our clients become more competitive,” said Frappier, adding that, “IoT and industry 4.0 are definitely buzzwords at the moment. Clients want to know more so we are increasingly exposed to solutions solved by emerging technologies.”
When Drives & Control Solutions asked Mr. Frappier about interesting projects he has worked on with JMP Solutions he elaborated on their work with SDVs.
“We are in the pilot stages currently of an SDV project that will deliver raw materials directly to the machine,” he said, “Loading and unloading of the raw materials is automatically controlled via custom designed tooling with several servo axes. Power consumption and weight calculations have us pushing the limits of what the SDV can accomplish but we have great partnerships with the manufacturers, so we are continually redefining what is possible for our client.”
As Frappier explained, they certainly aren’t resting on any laurels when it comes to the limits of their applications.
“As you can imagine, our client base of automotive manufactures has production throughput and quality as their main focus,” he explained with respect to projects that have provided a challenge for his team at JMP, “We are constantly challenged with requests to help make equipment more stable, reliable and without adding excessive costs.”
“The latest challenge was a servo system rotating a shaft of an engine assembly that when a new version of the engine was put into production, the torque characteristics of the existing servo system produced excessive overtravel conditions. Ultimately, we had to replace the servo motor with one that was larger and reprogram the system.”
“We have a large focus on our project management methodologies,” noted Frappier, which allows them to remain confident when posed with an unexpected challenge or when providing clients complex solutions and problem solving.
“Every employee at JMP undergoes some form of PM training. This helps us expect the unexpected and manage the project to ensure the client has an exceptional customer experience.”
In terms of day-to-day challenges, Frappier said their biggest challenge is balancing resources.
“We have peak periods throughout the year, such as scheduled shutdowns, that have the entire team engaged,” he explained, noting they “are fortunate that JMP has two lines of business and three branches all within an hour of each other in Ontario. We work together to share resources to help each other overcome the peaks and valleys that come with the work that we do.”
In his current role, Frappier manages the day-to-day operations at JMP’s Cambridge branch, “which is the centre of excellence for the AGV line of business,” he noted, “primarily servicing the automotive sector, responsible for executing around 200 projects a year with a team of technical staff, project managers and client service managers.”
“One of the differentiating features of JMP is our wide selection of offerings. To my knowledge, JMP is unique in that we can offer discrete controls, process controls, robotics systems, autonomous vehicle systems, MES solutions, material handling equipment as well as networking and security. Each of these offerings can be found under one umbrella and each is an arm of expertise or a solution provider to our customers. Being able to extend each of these services to the Fortune 1000 makes it easy to work with us,” Frappier explained discussing what makes JMP so successful in servicing a complex and demanding industry.
JMP Solutions is an industrial technology partner to Fortune 1000 manufacturers and producers. Throughout their 30-year history they have managed to grow steadily, with their success defined not only by that growth and the satisfaction of their clients, but they have been recognized with several awards. Awards such as Microsoft’s Impact Award for Data Management Solutions, the FANUC Excellence in Intelligent Robotics awards, as well as being certified as a Rockwell Automation Solution Provider.