Wonderful Pistachios Meets Global Demand With Food Production Facility
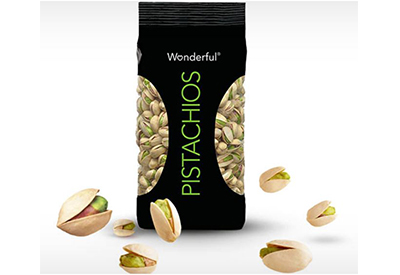
March 3, 2020
Pistachio trees didn’t exist in this country in the 1930s. Today, the U.S. is the world’s second-largest producer – and worldwide demand continues to grow.
Once reserved for royalty, pistachios have become a global snack sensation. People are hungry for the green nut because of its unique flavor, along with its natural health attributes. Like almonds, walnuts and other nut varieties, pistachios are packed with protein, antioxidants and fiber.
Wonderful Pistachios is a leader in satisfying worldwide demand for this tiny treat. The company is based in California’s central San Joaquin Valley, the heart of America’s pistachio industry. To flourish, the trees require cool winters and long, hot summers with low humidity. This largely limits pistachio production to three primary places on the planet – Iran, Turkey and California.
Today, Wonderful Pistachios alone accounts for 50 percent of the global pistachio market and 65 percent of the domestic sales. To continue to grow, Wonderful Pistachios needed a new facility where it could convert more raw fruit into the roasted – and usually salted – snack craved by consumers around the world.
Building a New Facility – Fast
The first stage of the production process – hulling – is time-sensitive. The nuts come off of the trees encased in a protective outer layer, which must be quickly removed to prevent spoiling. That’s why Wonderful Pistachios built the new facility in Firebaugh, California, close to the pistachio groves.
The hulling section of the new facility needed to be ready in time for the harvest, which begins in September and lasts eight to 10 weeks. After hulling, the nuts can be stored for the year-round processes of sorting, roasting, salting and packaging. Company managers planned to complete those subsequent sections once the hulling area was up and running.
They projected that more than 4.8 million pounds of pistachios would be hulled each day of the harvest. To handle such a huge volume – eventually across the entire production process – the new facility required major infrastructure investments, including a 30-megawatt transmission substation and miles of natural gas pipes.
With that groundwork under way, the company began planning the design of the hulling and production lines.
To manage the entire process, the Wonderful Pistachios team needed a control solution they could implement quickly, and later expand to include critical stages, such as pasteurization and precise roasting.
Precise Controls for a Precise Process
The choice of a control solution collaborator was straightforward for the project team since they’ve worked with Rockwell Automation for over 20 years. Almost 15 years ago, Wonderful Pistachios began standardizing on the Rockwell Automation control platform, including motor control centers (MCCs).
“In our industry, the turnaround time for projects is very fast,” said Don Kloster, electrical engineering manager for Wonderful Pistachios. “The Rockwell Automation control platform allows us to order and install controllers and MCCs, and start production in a few weeks.”
To control the 500 motors powering pistachio production at the new facility, Kloster and his team designed the process, confirmed their motor control needs, and ordered Allen-Bradley CENTERLINE® 2100 MCCs from Rockwell Automation in bulk.
The smart MCCs, integrated with Allen-Bradley PowerFlex® 70 and PowerFlex 525 drives from Rockwell Automation, help provide flexible control of production. The MCCs include preconfigured software that gathers real-time production and diagnostic data, trends, component history, wiring diagrams, user manuals and spare parts.
The MCCs provide significant startup time savings compared to Wonderful Pistachios’ previously in-house built panels. As always, the MCCs were fully inspected before arrival, easing installation for the Wonderful Pistachios team.
In addition, the MCCs’ centralized control and intuitive add-on instructions help provide a lower total cost of ownership compared to the in-house panels by reducing downtime and troubleshooting time. The team can easily make changes in the field, and quickly and safely move MCC buckets as needed.
The MCCs communicate the production and diagnostic data via an EtherNet/IP™ network to Allen-Bradley ControlLogix® programmable automation controllers (PACs) from Rockwell Automation.
Facility operators can access the data directly from the controllers and pull historical production reports within an hour. That data allows them to quickly determine – and if necessary, adjust – production variables, such as dryer temperatures and roaster speeds. With the EtherNet/IP network connectivity, Wonderful Pistachios can monitor all systems remotely and quickly respond to any issues.
In addition, the open nature of the control platform and the EtherNet/IP network allowed the Wonderful Pistachios team to easily install and connect OEM-supplied equipment. The team purchased dryers, pasteurizers and other equipment without controls, and integrated them into the ControlLogix platform.
Production by the Millions
After the MCCs arrived, the production line was ready to go live within three weeks, just in time for the fall harvest season. Pre-processing then started the following year, which exceeded volume estimates by 15 percent.
With the control system’s reliability and monitoring capabilities, the new facility runs lean.
“In 2000, 100 people were required to run a facility that would produce 1.5 million pounds per day,” said Paul Hughes, general manager of capital projects at Wonderful Pistachios. “At the Firebaugh facility, 10 people onsite manage production of 5.6 million pounds per day during harvest season.”
By 2023, the facility will have finishing-processing capabilities, and the entire buildout will be completed by 2025.