Wireless Makes the Connected Mine Possible – and Powerful
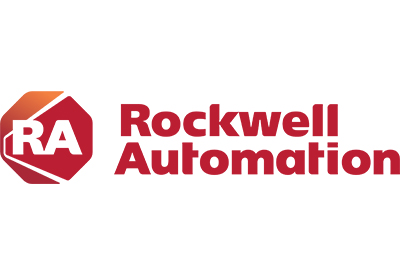
September 30, 2019
By Paul McRoberts
Mining operators face a unique predicament: They want to reap the value of a connected mine – such as with greater data access, real-time analytics, and autonomous systems and services – but their operations are perhaps the hardest in the world to reliably connect.
After all, mining operations not only span great distances, but they are often located in remote areas – including far below ground – with minimal or no communications infrastructure.
On top of that, constant digging or blasting can constantly reshape the landscapes upon which communications need to take place.
So how do you not only connect your operations but also maintain network uptime, which is crucial to both safety and productivity?
First, you need to make sure you have the right foundation in place. This requires converging your information technology (IT) and operations technology (OT) systems into a single, unified network infrastructure.
Not only does this eliminate silos of information, but it also enables seamless information sharing across your entire mining operation.
With a unified network infrastructure in place, you can implement wireless mesh communications to connect your people, places and technologies. Wireless is especially ideal for connecting all aspects of your operations – from trucks or trains, to underground workers, to analytics tools – because it can reach wherever you go, above or below ground.
But wireless can do more than connect your connected mine. It also can support new capabilities in your mine to help improve efficiencies, enhance safety and reduce costs.
Remotely connecting people. When downtime occurs, it is essential that employees have immediate, information-enabled support to quickly resolve the problem. Wireless communications in a mining operation can connect workers with the right people, in any location, helping to speed up troubleshooting when downtime happens.
Deploying autonomous transportation. It’s no secret that some mining companies are already using autonomous trucks and trains, which provide efficient transport and safety benefits. By using wireless to implement autonomous transportation, you can help to reduce the number of workers on the road and refocus their efforts on production goals.
Locating employees in an emergency: Built-in sensors on underground mining equipment, such as wristbands and helmets, are one of the many ways to help immediately and accurately locate employees in an emergency. This technology also can be useful in high-risk environments to help make sure all employees are in a safe place prior to dangerous tasks, such as blasts.
Adjusting ventilation settings underground: Ventilation-on-demand (VoD) systems can sense the presence of people and running vehicles, and change settings accordingly. This can not only enhance onsite safety but also help reduce energy costs.
Deploying wireless communications in a mining environment can be overwhelming, but there’s no denying the value or competitive advantages at stake. Don’t hesitate to ask for help from your automation and IT providers to help determine your right course for deploying a connected mine.
It is also worth taking a look at the many available free resources and best practices for using wireless in a connected mine. Learn more about mining automation solutions.