Why It’s Important to Know What Ip Rating You Need for Your Components
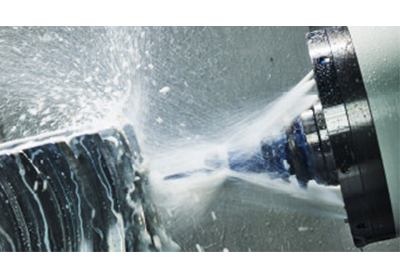
May 4, 2020
Given that many manufacturing processes involve high heat, powerful washdowns, dust, oil and other potentially harmful conditions, it’s essential to have a means of indicating the degree to which individual components can resist their operating environments. In fact, the standardization of these qualities has become a matter of international importance.
The international standard IEC 60529 provides a two-digit rating framework known as the Ingress Protection (IP) code for ascertaining how well a component will withstand environmental conditions. The first digit refers to protection from mechanical intrusion while the second refers to moisture resistance. Higher digits indicate greater protection.
In essence, the IP ratings are designed to provide a specific account of a component’s ruggedness and help manufacturers avoid using nebulous terms like “waterproof” or “water resistant” that could mean a variety of things: fully submersible in water, resistant only to condensation, or anywhere in between.
Important IP ratings to know for industrial environments
Since dust, grime and liquids are often abundantly present in industrial environments like automotive manufacturing, lower IP ratings aren’t usually very helpful. The most common IP ratings protect fully against dust (represented by a mechanical intrusion protection rating of 6) and to varying degrees against moisture.
- – IP65 – “Dust tight” and proofed against water coming from a nozzle.
- – IP66 – “Dust tight” and able to withstand powerful water jets.
- – IP67 – “Dust tight” and able to be immersed in water for a short time.
- – IP67G – Similar to IP67, but with added resistance to cutting oil. Omron has numerous sensors with this rating that are intended for applications using cutting oil. (This is not part of the IEC standards, but rather a JIS (Japanese Industrial Standards) adaptation.
- – IP68 – “Dust tight” and able to be completely and continuously immersed in water.
- – IP69K – “Dust tight” and protected against high-pressure, high-temperature water. This is the highest protection rating available, and it’s particularly important for food and beverage applications.
As you can see, there are many more gradations of water protection than simply “waterproof” and “water-resistant.” Water damage can severely hamper a component’s functionality, so it’s important to match the level of protection to the specific requirements of the application.
Omron’s ruggedized products maximize uptime and guarantee continued productivity
Omron builds protection from the elements into a wide range of technologies, including sensors, barcode readers, terminal blocks, limit switches and more. These water-, dust- and oil-resistant products are essential for ensuring the continued productivity of manufacturing equipment and processes.
Oil-resistant sensors are a key example of an Omron product that reduces unplanned downtime since it’s been shown that component failures cause 70% of unexpected production stoppages. Our oil-resistant sensor offering includes the new E3AS time of flight sensor as well as the new E2E NEXT proximity sensor series for long-distance detection in oily environments.
Our barcode reader portfolio includes the ultra-rugged HS-360X handheld imager that helps keep traceability processes running smoothly with a high level of industrial fluid and chemical tolerance. The reader itself has an IP65/67-rated casing while the charging station is rated as IP65. It’s also capable of withstanding multiple drops from as high as 8 feet.