What Are Acceptable Lockout/Tagout Locks?
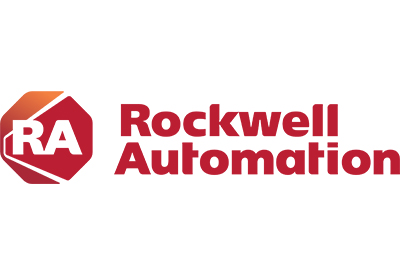
March 2, 2021
By Jake Thatcher, Senior Safety Project Engineer, Rockwell Automation
When it comes to the possibility of someone accidentally restarting a piece of equipment that another employee is working on, the only device that is protecting the employee is their lockout lock. It’s imperative that employees understand how to properly use their locks and also know to never lend out their lock or key, to ensure exclusive control at all times. When employees understand safety, and how to use keyed or combination locks properly, you can achieve a successful lockout/tagout program.
Acceptable Locks
A major requirement of OSHA’s Control of Hazardous Energy regulation (1910.147), is the use of protective materials and hardware during lockout.
OSHA requires that all locks must be:
- – Provided by the employer
- – Singularly identifiable for lockout use only, with an indication of which authorized employee is using them
- – Not used for any other purpose other than lockout/tagout
In addition:
- – The locks should be durable and able to withstand the environment in which they are being used
- – They should be substantial enough to prevent their removal without the use of excessive force
- – The locks must be standardized in color, shape, or size in a company’s lockout/tagout policy
- – Industry best practice is to use all red locks and devices, but some facilities may find it useful to use different colored locks for different departments
The employer must decide whether these locks are individually assigned or available from a pool of locks within their facility. It is also important to note that if an isolation point does not accept a lock, a lockout device with a lock must be used in this situation to keep the disconnect in the off position.
Keeping in mind all these requirements and recommendations, let’s determine whether to use combination, keyed, or both types of locks.
Keyed Locks
Keyed locks are the main type of lock used under OSHA’s 1910.147. Keyed locks are also the cheapest and safest option when it comes to lockout/tagout. It’s important to know that if your lock comes with two keys, the best practice is to dispose of the second key.
Combination Locks
Combination locks are another option that is acceptable under OSHA’s 1910.147, but there are additional safety measures that should be taken for their safe use. Just like keyed locks, only one person should be able to open the lock, which means only one person may know the combination to that lock. Therefore, it is not recommended to use combination locks for shared locks since the combination would have to get passed from employee to employee.
Pros and Cons of Different Lock Types
One benefit of using combination locks is that you don’t have to worry about losing the key for the lock, but instead must remember a series of numbers to open the lock. Since many maintenance employees already have a ring of keys, the use of combination locks will help to reduce the number of keys that they must carry around.
One major drawback with the use of combination locks is that nobody else is permitted to know the combination, not even a manager. If it’s believed that the employees will be able to remember the combination, and keep it to themselves only, then a site could consider combination locks.
If a site intends to have a pool of shared locks, such as a peg board of locks available, keyed locks will be the only option.
Master-Keyed Locks
Per OSHA, multiple-keyed or keyed-alike locks may not be used for the purpose of lockout/tagout. Any locks used must have only a single key, which must be under the exclusive control of the employee that applies the lock and is performing the service.
The subject of multiple-keyed or master-keyed locks used for lockout/tagout can be a confusing subject when referencing OSHA’s 1910.147. The standard requires that the lockout device be under the exclusive control of the employee applying the locks and performing the maintenance. In a 1995 letter of interpretation, OSHA states that a duplicate or master key may not exist for the purpose of removing a lock with a lost or misplaced key. In fact, any lock determined to have a missing key must not be used and should be immediately removed and replaced.
For more information regarding multi-keyed lockout locks, please refer to the letter of interpretation provided by the Federal OSHA.
Lock Removal – Who Can Cut Off a Lock and When?
If someone’s lock needs to be removed, the authorized employee who installed it should be the one to remove it. When this isn’t possible, a forced lock removal form and proper procedure should be followed.
According to OSHA’s lockout/tagout regulation, “When the authorized employee who applied the lockout or tagout device is not available to remove it, that device may be removed under the direction of the employer, provided that specific procedures and training for such removal have been developed, documented, and incorporated into the employer’s energy control program.”
In other words, under proper authorization of the employer, a supervisor may remove an employee’s lockout lock. This exception is only allowed under the circumstances that:
1. The employee who placed the lock is unavailable and,
2. It is necessary that the unit be returned to normal operation.
When faced with this situation, follow these simple steps to confirm it is properly handled.
DO:
- – Verify that the authorized employee who originally placed the lockout device is nowhere in the facility
- – Make all reasonable efforts to contact the authorized employee to inform them that their lockout device will be removed
- – Have the lock removed by a supervisor after verifying the authorized employee who placed the lock is not at the facility
- – The employer or supervisor should ensure that the machine is in working condition and capable of being turned back on, that all components and guarding are properly reinstalled from servicing, and no tools have been left in the area
- – Inform the authorized employee that their lockout device has been removed before they resume work at the facility
- – Provide a form to document what steps are being taken during the entire process, and to keep track of which responsibilities are being passed on to which employee
DON’T:
- – Remove the lock without notifying anyone in the facility. This is dangerous and is a direct violation of OSHA’s regulation
Employers must have a proper lockout/tagout program in place and a policy regarding the removal of lockout devices with steps that should be followed. After proper steps have been taken to remove the lockout device, standard protocol for re-energization of the equipment must be performed.