VFD Leakage Current and Ground Fault Protection: Ensuring Safety and Compliance
February 18, 2025
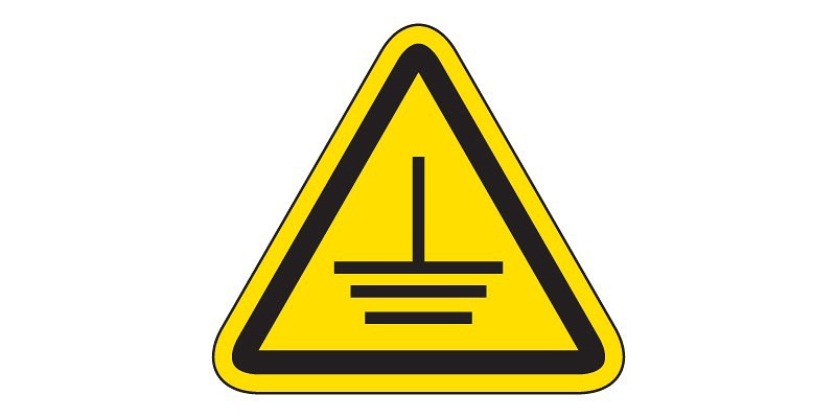
By Damien Herweg, Product Marketing Manager SmartD Technologies
Why the Smallest Currents Matter:Understanding LeakageCurrent and Ground Faults in Modern VFDs
Imagine a bustling manufacturing plant where machines produce thousands of components every hour. The electrical cabinets buzz with energy, and a labyrinth of cables branches out to every corner, connecting motors large and small. In one corner stands a shiny new Variable Frequency Drive (VFD) controlling a high-horsepower motor. Nearby, an experienced technician named Alex notices something on his handheld meter: a small current is flowing to the ground.
At first, it might seem like no big deal, just a few milliamps. But is it dangerous? Or completely normal? This is the heart of our story, and it brings up a question that might be obvious to an experienced professional but still makes you think deeply.: why do we place so much emphasis on the small currents? Why do we, as engineers and technicians, meticulously measure, analyze, and sometimes worry about these tiny currents that appear to do no harm? The reason, of course, is because these small currents can be indicators—indicators of normal operation, or signs of a potential problem that could cause serious safety issues.
Welcome to the world of leakage current and ground faults in VFD systems. In this article, we’ll explore these phenomena with a didactic approach, focusing on why they matter, how they behave, and what sets them apart, especially when looking at clean power VFDs. Whether you’ve spent decades in electrical systems or you’re just stepping into this specialized area, this exploration aims to reinforce the concepts and inspire you to dig deeper into the nuances of these tiny but critically important currents.
Setting the Stage: Leakage Current in VFDs
Leakage current is that “small” amount of current that flows through an unintended path to ground/earth.” In the context of a VFD, it typically emerges due to capacitances and inductances within the drive or from the high-frequency switching in power electronics. If you’ve ever measured ground current in a VFD system, you’ve probably noticed that it rarely is at zero. Instead, there’s almost always a measurable reading—often in the milliamps range. Why is that?
Filters
Most VFDs include internal filters to mitigate electromagnetic interference. These filters, by design, have capacitors from the drive’s internal circuitry to the ground. Even when everything is functioning perfectly, a small current (the filter’s design leakage) flows through these capacitors. It’s not a bug; it’s an inherent part of the filtering solution.
Motor Cables and Motor Windings
Next, consider those long cable runs from the drive to the motor. With high-frequency PWM signals, these cables act like capacitors between the conductors and any nearby grounded metal conduit. The rapid switching transients lead to a small “charging current” to the ground. We often measure this on the order of milliamps, but for large motors and very long cables, it can reach tens or even hundreds of milliamps.
Semiconductor Switching Devices
Whether you’re using IGBTs or SiC MOSFETs, each transistor has parasitic capacitances that can let a small current pass to ground during switching transitions. Again, not a fault condition—it’s simply physics at work.
The Nature of Leakage Current
Leakage current is usually continuous (or quasi-continuous) in normal operation. The amplitude might fluctuate with load, switching frequency, and cable length, but it doesn’t typically spike into the ampere range under normal circumstances. A typical range might be from a few milliamps up to tens of milliamps. The key is that it is expected. In fact, some standards address this directly. For instance, Standard IEC 61800-5-1 (section 4.3.5.5.2.) stipulates that if a drive’s normal touch current is above 3.5 mA AC or 10 mA DC, you must have a protective measure.
Enter the Ground Fault: A True Fault Condition
Now, let’s talk about ground faults. A ground fault is, by definition, an unintended or accidental path for current to flow to the ground. This typically arises due to insulation failures within motor windings or cables. It might be caused by physical damage, moisture infiltration, chemical contamination, or simple aging of materials. When a ground fault occurs, the current level can skyrocket—from amps to hundreds of amps—depending on the system voltage and the impedance of the fault path.
For example, imagine Alex sees a sudden spike in ground current, jumping from a steady 10 mA to 5 A within milliseconds. That’s a strong sign of a ground fault. Protective devices such as circuit breakers, fuses, or ground-fault protective relays typically detect this surge and trip to isolate the equipment, safeguarding people and property. So while leakage currents are generally mild and continuous, a ground fault is a high-magnitude event that demands immediate attention.
Why is it so critical to detect ground faults quickly? Beyond the obvious safety aspect (risk of shock or electrocution), ground faults can destroy motor windings, damage drive components, and cause extended production downtime. Thus, in a properly designed system, you’ll see clear isolation of these high currents within a fraction of a second.
Why the Confusion?
You might be asking yourself: “If one current is normal and the other is a fault, why do so many technicians confuse the two?” The answer lies in a few factors:
- Both Flow to Ground
A meter placed on the ground conductor merely sees “some current.” If an engineer is not aware of the typical leakage values of a VFD, they might prematurely label any ground current reading as a “fault.” - Protective Device Sensitivity
Many residual-current or ground-fault devices are designed with thresholds that might be too low for typical VFD leakage currents. A sensitive device might trip at, say, 30 mA, which is not uncommon as a normal VFD leakage current. Hence, you get nuisance tripping. - High-Frequency Components
Standard measuring devices may interpret the high-frequency leakage from PWM signals as a fault if they’re not designed to filter out these components. - Loose Terminology
In everyday conversations, people might casually call anything going to ground ‘leakage,’ without distinguishing between normal and fault conditions.
So, Are They the Same?
Absolutely not. Leakage current is expected and often inherent to the design of VFDs—particularly those using PWM with EMI filters. Ground faults, on the other hand, are unplanned events that signal an electrical breakdown and require immediate action. One is normal, the other is not.
A Look at Clean Power VFDs
As technology evolves, we now have Clean Power VFDs that use multi-level SiC MOSFETs to generate a pure sine wave instead of the typical PWM wave. With fewer high-frequency transitions, the entire leakage current profile changes.
- Minimal High-Frequency Components
Since the Clean Power VFD outputs a true sine wave rather than a high-frequency PWM waveform, there is minimal capacitive coupling to the ground. This reduces the need for large EMI filters, inherently lowering leakage currents and improving compatibility with ground fault protection devices. - Active Front End (AFE)
A robust, low-distortion input stage ensures that the line side sees a sinusoidal current draw, reducing the overall ground-referenced noise. This gets rid of many common VFD issues, like high-frequency leakage or harmonic-induced ground currents. - Easier Ground Fault Detection
Since normal leakage is minimized, the differentiation between a normal ground current and a genuine ground fault becomes more pronounced. Protective settings can be more sensitive without risking nuisance trips.
Nonetheless, let’s not be fooled into thinking Clean Power VFDs eradicate ground faults altogether. Whenever insulation fails, a ground fault remains a ground fault—no matter how sinusoidal the drive’s output is. The real advantage is the clarity in diagnosing the problem because you have a lower baseline of leakage current to sort through.
Bridging Theory and Practice
Picture Alex, our plant technician, working on a brand-new Clean Power VFD installation. After running the cables, testing insulation resistance, and powering up, the drive shows a stable and low leakage current. Now, if that drive were a standard PWM-based VFD with significant EMI filters, Alex might measure 30–50 mA and question whether it’s normal. With the Clean Power VFD, it’s more straightforward for him to interpret the ground current values.
But does that mean Alex can forget about ground fault protection? Absolutely not. If a day later, the drive logs a sudden spike or meltdown in ground current, that signals a true problem—insulation breakdown, moisture intrusion, or mechanical damage. He’ll rely on the drive’s ground-fault detection to trip safely and log the event.
The “Why” That Guides Us
Why should engineers and technicians care about leakage current and ground faults in VFDs?
- Safety of Personnel
Even small currents can cause serious shock risks if a path through the body is formed. Ground faults, of course, are far more dangerous in magnitude. - Protection of Equipment
Proper classification of ground current prevents nuisance tripping and ensures that real faults are cleared quickly, sparing equipment from catastrophic damage. - Regulatory Compliance
Standards like IEC 61800-5-1 define minimum requirements for protective earth connections and permissible leakage current levels. Ignoring these can lead to code violations and legal ramifications. - Operational Continuity
Minimizing nuisance trips and quickly resolving actual ground faults keeps production lines running, satisfying operational demands and maintaining profits.
A Final Word on Design and Coordination
The key is understanding the nature of the ground currents and coordinating protection accordingly. If your system regularly sees tens of milliamps due to EMI filters, you may need to adjust your ground-fault protective devices or incorporate advanced filtering methods. If you adopt a clean power VFD, you’ll likely see lower leakage current and thus simpler fault discrimination.
But in all cases, the principles remain the same:
- Leakage Current: Normal, predictable, usually small.
- Ground Fault: Abnormal, unintended, potentially large, and requires immediate attention.
By recognizing the distinction and applying the right protective strategies, you ensure a safer, more reliable environment—one where Alex and every other technician can confidently interpret ground current measurements without second-guessing whether a small reading is a sign of imminent danger or just the steady hum of a well-designed VFD system.
Understanding the difference between leakage current and ground faults is key for maintaining a safe and efficient VFD system. If you want to ensure your systems are operating at their best, consider conducting a thorough inspection and implementing the right protective measures. Don’t hesitate to reach out to a professional for in-depth analysis and tailored solutions. Your safety and operational efficiency depend on it.
Related Story
2-Wire vs. 3-Wire VFD Configurations: A Comprehensive Guide for Safer and More Efficient Motor Control
Recent discussions Damien Herweg had with colleagues motivated him to write this article—to explain, simplify, and share the concept of 2-wire and 3-wire preset configurations in Variable Frequency Drives (VFDs).
Whether you’re an experienced engineer or you’re new to industrial automation, this guide will clarify how these wiring modes work, why they matter, and when to use each of them.