Understanding Motor Duty Cycles
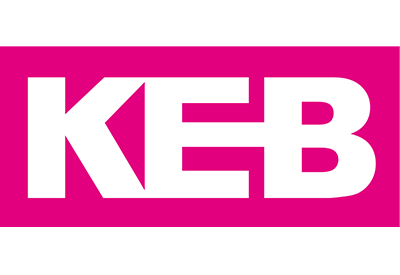
February 18, 2020
By Mike Keefe
When selecting a motor, it is important to consider the required duty cycle to ensure the motor can meet the needs of the application.
Knowing what type of duty cycle your motor requires will help a motor manufacturer like KEB select the best motor for your application. Watch the video below to see the most common types of motor duty cycles.
{videobox}O-ODHlWzDj8{/videobox}
The International Electrotechnical Commission (IEC) defines eight classifications for duty cycle which are grouped by continuous, short term, or periodic cycles. These cycles refer to the sequence and durations in time of all aspects of a typical operation, including starting, running with no load, running with full load, electric braking, and rest. These operations are viewed by how they affect the motor temperature in order to determine if the selected motor is correct for the application, if increased cooling such as a forced ventilation fan is required, or if a whole new motor should be used.
Continuous Duty
The first, and simplest, type of motor duty cycle is continuous duty. This is also referred to by its abbreviated name, S1 duty. In this type of operation, the motor runs with a constant load for a long enough duration so that it reaches thermal equilibrium. This also assumes the starting of the motor can be considered to have a negligible effect on the motor temperature. An example of S1 duty would be a fan that is switched on and then let to run non-stop.
Short Time Duty
The second type of motor duty cycle is short time duty. Similar to continuous duty, this operation runs with a constant load. Unlike continuous duty, it is shut off before it reaches thermal equilibrium. The motor is then allowed to rest long enough for it to reach ambient temperature. Short time duty is designated by S2 followed by the number of minutes in the cycle (S2 30 minutes).
Periodic Duty
Periodic duty refers to the designations S3-S8. These include cycles with and without rest that have starting, electric braking, and/or changing speeds/loads. Throughout all of these designations, the various operations of the cycle are repeated over time and the motor is not allowed to reach thermal equilibrium.
Intermittent Periodic Duty
Intermittent periodic duty is the simplest type of periodic duty. This sequence of identical cycles each contain a period of constant load and a period at rest. This is very similar to S2 duty, but differs because it never reaches ambient temperature during its rest period. This duty cycle is abbreviated as S3 followed by the percentage of time under load.
An example of intermittent periodic duty could be a conveyor that runs at constant intervals with the same loading.
Continuous Operation with Electric Braking
The final example of motor duty cycle is continuous operation with electric braking. This cycle includes a sequence of starting, constant load, and electric braking.
Additionally, there is not time during the operation for rest. This type of duty cycle is abbreviated as S7 followed by the moment of inertia of the motor and load (Jm and JL).
The other periodic duty cycles S4-S6 and S8-S9 are similar to S3 and S7, but can be done with or without rest, starting, braking, and loading.
Conclusion
When purchasing a motor, it is important to consider the required operation and declare the duty cycle. There are many types of motors and gearing combinations that can be offered for your specific application. When you let a motor manufacturer know exactly the type of duty the motor can expect, you can ensure the proper motor will be selected for your application.