Trapezoidal vs Sinusoidal Servo Brushless Amplifiers
December 4, 2024
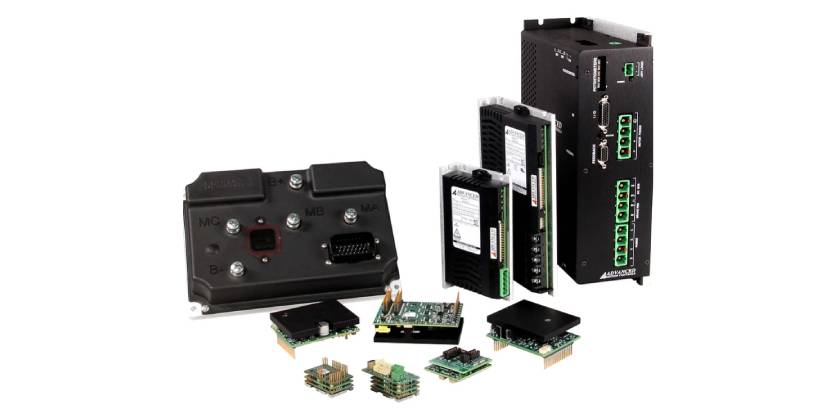
Servo brushless amplifiers are critical components in motion control systems, providing precise regulation of brushless motors for torque, velocity, and position. The two most common types of brushless amplifiers, trapezoidal and sinusoidal, differ significantly in their operation and performance characteristics.
This paper provides an in-depth comparison of these amplifier types, outlines their operational principles, and examines specific scenarios where one may be preferable to the other.
Understanding Trapezoidal and Sinusoidal Amplifiers
The fundamental distinction between trapezoidal and sinusoidal servo brushless amplifiers lies in the waveform of the current they deliver to the motor.
Trapezoidal amplifiers produce a current waveform with a trapezoidal shape, while sinusoidal amplifiers generate a smooth sinusoidal waveform.
These waveform differences affect key aspects of motor performance, such as torque smoothness, noise, and efficiency.
Trapezoidal amplifiers, often associated with 6-step commutation, offer a simpler and cost-effective approach to controlling brushless motors. In contrast, sinusoidal amplifiers employ continuous commutation and advanced control algorithms, such as Field-Oriented Control (FOC), to deliver highly precise and efficient performance.
Operational Differences Between Trapezoidal and Sinusoidal Amplifiers
Trapezoidal Amplifiers
Trapezoidal amplifiers operate using a commutation method where current is supplied to two motor phases at a time. This results in a trapezoidal back-electromotive force (back EMF). The commutation process typically relies on Hall effect sensors to detect rotor position and determine when to switch the phases.
This type of amplifier features straightforward control logic and is valued for its simplicity and cost-effectiveness. However, the abrupt switching of current between phases causes torque ripple, leading to increased vibration and audible noise during operation. Despite these drawbacks, trapezoidal amplifiers are widely used in cost-sensitive applications where performance demands are moderate.
Sinusoidal Amplifiers
Sinusoidal amplifiers use a more sophisticated approach, generating a sinusoidal current that flows continuously through all three motor phases. Using commutation from precise feedback devices, such as encoders or resolvers, these amplifiers ensure that the current waveform is optimally aligned with the motor’s magnetic field. This results in smoother torque production and a significant reduction in vibration and noise compared to trapezoidal amplifiers.
The advanced control capabilities of sinusoidal amplifiers allow them to handle complex motion profiles with exceptional accuracy. These amplifiers are commonly used in high-performance applications that prioritize precision, efficiency, and quiet operation. However, their complexity and higher cost make them less suitable for simpler systems.
Trapezoidal Amplifier Configurations: 6-Step vs. 12-Step
Trapezoidal amplifiers can be implemented in either 6-step or 12-step configurations, each with unique characteristics.
The 6-step configuration is the most basic form of trapezoidal commutation. It divides the electrical cycle into six distinct steps, with each phase energized for 120 electrical degrees. While this approach is straightforward and requires minimal hardware, it produces noticeable torque ripple due to the coarse commutation steps.
In contrast, the 12-step configuration refines the commutation process by splitting the cycle into twelve smaller steps, effectively halving the angle at which phase switching occurs. This leads to smoother torque delivery and reduced ripple, although the increased complexity demands more advanced control systems and hardware.
Advantages of Sinusoidal Amplifiers Over Trapezoidal Amplifiers
While both trapezoidal and sinusoidal amplifiers have their place in motion control, sinusoidal amplifiers excel in certain conditions:
- Precision and Smooth Torque: Sinusoidal amplifiers provide a seamless current waveform, ensuring minimal torque ripple. This is critical in applications like robotics, CNC machines, and precision assembly systems.
- Quiet Operation: The reduced torque ripple of sinusoidal amplifiers minimizes audible noise, making them ideal for environments where sound levels are a concern, such as medical devices or office equipment.
- Energy Efficiency: Continuous sinusoidal commutation optimizes motor efficiency, particularly in applications with variable speeds and dynamic loads.
- Advanced Motion Control: With their ability to manage complex motion profiles, sinusoidal amplifiers are better suited for demanding applications requiring precise control of velocity, position, and acceleration.
- Acceleration Feed Forward is an advanced control feature typically available in most sinusoidal brushless servo amplifiers. Acceleration Feed Forward is a control method that utilizes a feedforward control strategy to proactively compensate for the inertial forces experienced during the acceleration and deceleration phases of a motion profile, essentially predicting and applying the necessary torque to minimize position errors during these dynamic movements by directly calculating the required torque based on the desired acceleration of the system.
Conversely, trapezoidal amplifiers are best suited for applications where cost and simplicity take precedence, such as fans, pumps, and straightforward conveyor systems.
Conclusion
The choice between trapezoidal and sinusoidal servo brushless amplifiers depends on the specific requirements of the application. Trapezoidal amplifiers offer a cost-effective solution for simpler systems but are limited by torque ripple and noise. Sinusoidal amplifiers, while more complex and expensive, deliver superior precision, smoothness, and efficiency, making them the preferred choice for high-performance and noise-sensitive applications.
By understanding the operational differences and application-specific advantages of each amplifier type, engineers can make informed decisions that optimize system performance and cost-effectiveness.
Related Story
Advanced Motion Controls Unveils Next-Generation FlexPro® EtherNet/IP Servo Drives
The FlexPro® drive series is AMC’s latest family of digital servo drives designed for high power, small size, and reliable servo motor control. The drive architecture allows for higher power densities while still maintaining reliability and versatility. The advanced processing and storage capabilities ensure that the drives are more intelligent and operationally flexible than ever before.
The micro-sized FlexPro drives have a footprint of 1.50 x 1.00 inches (38.1 x 25.4 mm) and are available with input voltage ranges of 10-55 VDC or 20-90 VDC, and both peak and continuous current ratings as high as 60 amps.
The mini-sized versions have a slightly larger footprint of 1.70 x 1.50 inches (43.2 x 38.1 mm) and are available with an input voltage range of 20-90 VDC, with a continuous current rating of 50 amps and a peak current rating of 100 amps.