Three Strategies for Immediately Improving Order Picking with Robotics
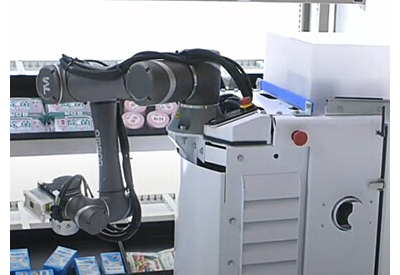
August 10, 2022
Together, shipping, receiving, and storage count for less than half of all warehouse activity costs. The lion’ share of expenses – a whopping 55% – is bound up in order picking. Breaking down the various activities associated with order picking, Omron finds that over 60% of time is spent walking, with writing, searching, and picking tasks comprising the other 40%.
Give this data, it’s safe to say that automating the “walking” portion of any order picking operation will have a strong positive impact on overall warehouse productivity. Omron’s Logistics Strategic Account Manager Yaqing Sun recently discussed some strategies for using autonomous mobile robots (AMRs) for this purpose at Automate 2022 in June.
Omron looks at a few methods for replacing unnecessary walking time with AMRs.
Strategy #1: Transporting items to employees (“Goods to person”)
By having an AMR autonomously move goods to a warehouse associate, you can reduce the amount of time that associate spends walking, which in turn reduces fatigue and generally improves work satisfaction. In addition, it improves traceability by automating the QR code scanning process.
Some potential downsides of this method include high up-front investment costs, a relatively long integration and/or installation time, and the likelihood of infrastructure changes to the facility. Still, logistics facilities by and large find that the productivity benefits heavily outweigh the initial costs of deployment.
View more solutions for logistics and warehouse automation
Strategy #2: Transporting items between zones (“Person to goods”)
This strategy involves breaking up the warehouse into separate order picking zones, each of which will have a dedicated employee. Since a single order might involve picking from more than one zone, an autonomous mobile robot will move between the zones, stopping whenever an employee needs to retrieve a particular item.
Although each employee still must do some walking, having AMRs traverse the long distances between zones cuts down on the walking by a significant amount. The main downside of this method is that employees must still scan items manually, so traceability isn’t fully automated.
Strategy #3: Transporting items to a robot (“Goods to robot”)
This method has the dual advantages of high accuracy and a low dependence on labor availability (making it a good option for companies struggling to hire personnel). Slight downsides include high investment costs and the possibility of lower throughput relative to manual picking. (It does improve traceability, however, for the same reason as Strategy #1.)
Nonetheless, collaborative robotic technology is advancing by leaps and bounds, and solutions that connect an autonomous mobile robot with a cobot are going to just get more and more efficient. Furthermore, both AMRs and cobots can work around the clock with minimal downtime.
Interested in learning more about Omron’s AMR solutions? Check out their mobile robot portfolio