The New Engine Behind Agile EV Powertrain Lines
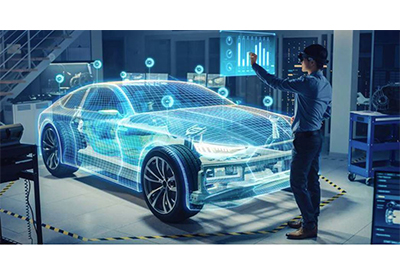
March 2, 2020
By Bill Sarver
What will the automotive marketplace look like in 10 years and how do I prepare for it? That’s the question foremost on the minds of the powertrain plant personnel I encounter in my work as an industry consultant.
It’s not an easy question to answer given that we are in the midst of a truly revolutionary time in the automotive industry. To address regional emissions mandates and upcoming bans on gasoline and diesel-powered automobiles, manufacturers are ramping up their focus on electric vehicles (EVs).
Mature automakers are beginning to abandon development of gas combustion engines altogether. EV startups are vying for their share of the market. And all players are keenly focused on optimizing powertrains and EV drivetrains for a future characterized by autonomous and connected vehicles on the one hand – and more personalized vehicles on the other.
To paraphrase a popular saying, the only constant in the “new” powertrain business is change.
And the industry winners in the years ahead will be those who can quickly transform manufacturing lines and processes to take advantage of new technology and scale up fast to meet market demand.
Roadblocks to EV Powertrain Manufacturing Agility
Computer-aided design (CAD), product lifecycle management (PLM) and automation platforms have come a long way in streamlining manufacturing planning and design. Combined with smart devices, sensors, MES, and IoT analytics, these systems deliver contextualized information to optimize operations and help guide continuous improvement.
But many existing systems fall short in one significant way. They cannot test and assess the impact of product design or line configuration choices before they are in place.
In other words, what actually happens if you add this new station or process to your EV powertrain line – or ramp-up a line originally configured to run 30 jobs per hour to one that runs 45? What choices will improve overall performance? What is the best method to rebalance your line?
Being able to quickly address logistic, quality and/or personnel issues while in production or during the design process before significant capital investments are made is critical to manufacturing agility and success.
How Digital Twins Change the Lifecycle Equation
With the advancement of dynamic digital twin software, legacy powertrain and new EV drivetrain producers are turning to the virtual world for answers and a better way to manage the manufacturing lifecycle.
A digital twin is a digital model of the physical manufacturing system created by connecting directly to CAD and PLM systems – plus the operational logic of the system. The result is a virtual, accurate representation of the manufacturing line that uses a real control system.
With a digital twin, you can prototype the design of a powertrain or drivetrain line in the virtual world – and test, debug and verify performance before you build or commission it.
Then, emulate the line throughout the system’s lifecycle to model performance and test new products and configurations. Keep in mind, digital twins leverage usage data captured by sensors and automation in the physical world to deliver a holistic picture that sheds light on current operation and potential bottlenecks.
Lower Risk of New Technology Implementations with Better Decision-making
Simply put, dynamic digital twins help you reduce the risks associated with innovation by clearly demonstrating the impact of system design choices.
Digital twins enable EV drivetrain and battery module/pack producers to address the manufacturing lifecycle in a new way – and create a truly agile environment that keeps pace with technology and market developments.
Learn more about how Rockwell Automation dynamic digital twin solutions can help you unlock a more agile manufacturing process.
And discover other ways we are helping EV manufacturers win the race to market.