The Factory of the Future . . . Today!
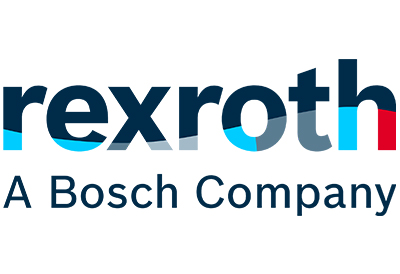
August 20, 2019
By Owen Hurst
Earlier this year, while attending Hannover Messe 2019, I had the privilege to partake in a private tour of Rexroth’s booth. As I have noted in previous writings on Hannover it is difficult to truly relate the size and scale of the booths at this show if you have not attended, but many easily reach into the 10-15,000 square foot range, and Rexroth’s booth was right there among the largest. Not only that but their booth was the only one that featured hosted 5G outside of the special 5G pavilion and was also toured by German Chancellor Angela Merkel.
Currently, Rexroth is engaged in a global push to advance the factory of the future. But what does that truly mean and is the factory of the future something we can begin to see in operation today? Simply put the answer is yes. To understand it completely I not only toured Rexroth’s booth in Hannover but also received a private tour and lesson on the factory of the future at the Advanced Design and Manufacturing Technology show (ADM) in Canada in early June. At this show Asvin Parsad, Business Development Manager i4.0 and Automation Systems walked me through the technology, with a focus on solutions already available in Canada or that will be by the end of 2019.
To tie it all together I first consider the factory of the future as it was portrayed in Hannover, which focused largely on products we will see in the years to come, and then conclude with the Canadian perspective from a local show that focused on the factory of the future today.
In Hannover Rexroth’s booth focused substantially on the connectivity and digitalization that is coming to future factories through advanced use of Automated Guided Vehicles such as ActiveShuttle, as well as other features such as advanced transport and handling systems, a digital service assistant, digitization of linear motion technology, connected hydraulics and localization. There were also several additional and interesting features available, not least of which was the ability to play foosball against a robot. But the primary focal point of the booth was the AGV’s (ActiveShuttle), and a large display featuring Rexroth’s smart factory floor.
The factory floor certainly caught the attention of most passers-by as it was white lit and showcased AGV’s zipping around in a coordinated fashion. The smart floor, which will one day likely be the standard in manufacturing facilities offers multiple benefits. Aside from actively guiding and monitoring the position and routes of AGV’s the floor is equipped with sensors that allows tracking and real-time viewing of all AGV’s and employees within the plant. It can also detect and send alerts in the event of incidents such as collisions, dropped material or even if an employee suffers a fall. The ability to monitor all movement throughout the factory is a great safety feature, but also will provide substantial data on routes and paths and will allow for advancements in efficiency of operations.
Moving now to the products and solutions showcased by Rexroth at ADM we discuss the factory of the future and how it is becoming a reality today. Asvin was a fantastic guide to the products being offered by Rexroth, and the value they deliver to manufacturers. He also pointed out that the key element that Rexroth is focusing on for the factory of the future is to ensure that every product delivers connectivity, flexibility and digitalization. This is certainly the goal for the future, and at current Rexroth is focused on having every product meet at the minimum one of these requirements and moving forward will implement all three criteria to their offerings.
Some of the interesting products we looked over were the ease and ability to immediately update orders for manufacturing and material picking machines, and the advantages provided by connectivity and in particular the ability to obtain deep analytics that have value on the plant floor and the boardroom.
It was interesting to see that rush orders could be immediately enacted within manufacturing processes, with the machine easily understanding the new process and undertaking to immediately complete it, after which it automatically returns to the order it had been previously working on completing. Those at the show were able to witness this firsthand. The ability to input new orders without the need to cancel previously inputted data ensures zero downtime and flexibility in manufacturing.
The connectivity option provided by Rexroth is also an increasingly valuable tool within the manufacturing industry, both for real-time monitoring by operational staff as well as deep analytics that can be used at the executive level to determine profitability and operational efficiencies and inefficiencies. The ability to extract data and have it presented in a clean and usable manner from the start allows companies to optimize their operations and make educated plans for the future.
Rexroth has certainly adopted a future that embraces connectivity, flexibility and digitalization and have taken that view of the factory of the future and made the first steps toward it being available today!