Strategies for Increasing Production Line Modularity
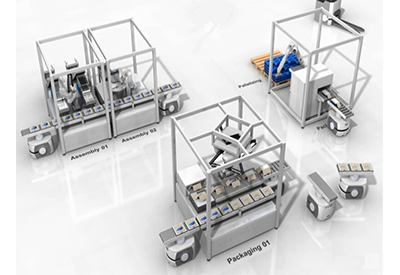
April 20, 2021
In today’s competitive business environment, customization is key. Manufacturers in all industries are expected to provide a wide range of sizes, colors, styles and assortments, and they are finding it essential to implement flexible manufacturing strategies in order to stay competitive.
The goal of these strategies is to reduce the effort required to change over from one product version to another. Let’s take a look at a couple of ways in which this can be accomplished.
Find ways to minimize rigidity
To determine how to make a system more flexible, it helps to find particular elements that are highly rigid and see how these could be made modular with cutting-edge technology. One example of an inflexible element is a conveyor belt. If conveyors connect production line stations, it can be extremely difficult to rearrange the line or add new stations.
Employing autonomous mobile robots (AMRs) with integrated conveying functionality can dramatically increase flexibility. These robots can take care of materials transport needs without requiring fixed pathways or any other changes to the factory floor. Today, we even see AMRs with integrated collaborative robotic arms that comprise a full pick-and-carry solution.
Avoid excessive part orientation hardware
Traditional parts feeding solutions, such as bowl feeders, typically require parts to be oriented in highly precise ways prior to feeding. Unfortunately, this calls for specific hardware that must be redesigned whenever a new type of part is being produced, dramatically increasing costs and lengthening the time required for a changeover.
Omron’s AnyFeeder solution combined with a vision-guided robot can accomplish any pick-and-place need without requiring custom features for every changeover. This solution is capable of picking parts regardless of shape or orientation and placing them in the required position and orientation for further processing.
Take advantage of wireless technologies
You don’t always need to purchase the most complex, next-generation technologies to make your production line more modular. Even a relatively simple technology like the Omron A2W Series wireless pushbutton can be a huge improvement if it minimizes wiring. The A2W doesn’t have any wires at all, and that’s what makes it great for maximizing layout flexibility.
In fact, the A2W is so flexible that it can even be installed on moving parts. No batteries are required thanks to the pushbutton’s self-generating power that comes from the actuation force, so maintenance is unnecessary.