Siemens’ SIRIUS Controls Ensure Cold Beer
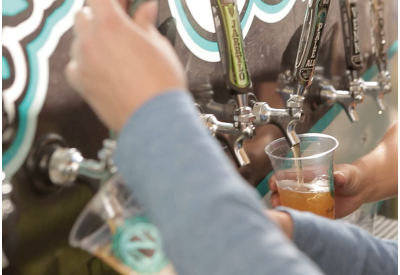
August 3, 2022
Breweries are known for transforming malt, hops, and yeast into beer in gleaming brewing kettles and large fermentation tanks linked by numerous pipes.
Over the centuries, the equipment for mashing, lautering, boiling, and fermenting beer according to carefully guarded recipes has been steadily perfected.
The chiller is the heart of the brewery
One of the most important parts of the brewery, and perhaps the least visible, is the chiller. The fermentation temperature of the beer is crucial, which means that the heat generated by the yeast fermentation must be carefully controlled by the chiller.
If the beer ferments at too high a temperature, the yeast can produce a variety of undesirable aromas that ruin the beer.
According to Justin Thomas, President of G&D Chillers, based in Oregon
“The chiller is the heart of the brewery. Owners invest not only a lot of money in the brewery and brewing equipment, but also a great deal of time in the production of beer. But if the chiller fails, all that goes out the window.”
G&D Chillers produces a wide range of small, portable glycol chillers and heaters, as well as large, customized refrigeration units.
Partnerships to keep pace with growth
Thomas says that growth at G&D Chillers has been exponential over the past 15 years. To continue this rate of success, the company had to look for new ways to meet customer demands for reliable, state-of-the-art chiller options.
For example, G&D Chillers recently teamed up with Siemens and the global distribution and supply chain solutions company WESCO to meet these needs and stay ahead of the competition. “We’re still a small manufacturing company, but big enough to produce some technically advanced equipment,” says Thomas. “We’ve always been service-oriented and always stood by our equipment, no matter what the problem. We get the same kind of support and service from Siemens that we give to our own customers.”
One of G&D Chillers’ customers, Barnum Mechanical, of Loomis, California, designs and builds sanitary process systems for the food and beverage, geothermal, and specialty process industries, including craft breweries and state-of-the-art process facilities.
Particular emphasis is placed on sustainability, not only in terms of reducing waste streams and water consumption, but also of innovative solutions for recovering and reusing energy.
The Siemens controls used by Barnum Mechanical support the brewing process by controlling the chiller under a wide range of system and environmental conditions. Cooling loads are frequently subject to severe fluctuations and can increase within a short time, for instance. Business development engineer Jared McClintock says the control system produces stable performance, even when inputs are volatile. This ability to provide constant coolant temperatures creates a controlled environment within the production plant.
Standardization of production using Siemens controls
The experienced, high-tech production team at G&D Chillers, most of whom have been with the company for more than a decade, initially had reservations about integrating the Siemens infeed system into their already successful product lines.
They soon discovered, however, that individual circuit breakers, complete load feeders, and compact starters could be clicked into the feeder system quickly and easily. It did not take long, therefore, to make the decision to standardize.
“The control cabinet’s infeed system with its toolless connection module using “snap together” technology has reduced our wiring time by 25 percent,” says General Manager John McCoy. “This alone saved us about ten hours on wiring—time we can now spend making more chillers in our lean manufacturing operation.”
To find out more about everything you need for controlling and protecting, click here