Introduction to SEW-Eurodrive’s Innovation Lab
August 3, 2022
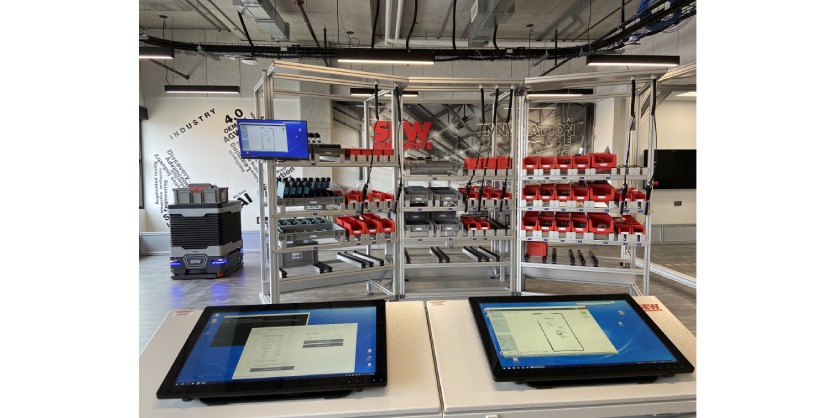
By Krystie Johnston
SEW-Eurodrive’s Innovation Lab
The introduction to SEW-Eurodrive’s Innovation Lab was a big success. With Ontario reopening earlier this year, SEW-Eurodrive has been excited to present their technology and automation solutions with customers, students, and the public again. Konrad Kurylo, P. Eng., was on site with other SEW-Eurodrive experts to welcome an enthusiastic and engaged audience, who were eager to see what products and solutions SEW-Eurodrive has to offer for Industry 4.0.
Automated guided vehicles (AGVs), collaborative robots (cobots), and augmented reality (AR) all had a turn in the spotlight, where the SEW-Eurodrive professionals explained their technology and applications, and customers could ask questions to gain insight into how they could be integrated in their facilities. Seeing the technologies in the Innovation Lab demonstrated how small and medium enterprises (SMEs) can use these technologies to enhance their production processes and elevate their factories into the future.
“You can see that we employ a lot of forward-looking technology, and we are all about Industry 4.0. One aspect of Industry 4.0 is about interconnectivity of high-level IT systems and real time process data transfer between all the parts of the manufacturing process/cycle. From the high-level IT like a WMS/EMS such as SAP for example, all the way down to the production line, between individual machines, and the smart components at the factory floor.”- Konrad Kurylo, P. Eng., Technical Sales, SEW-Eurodrive Canada
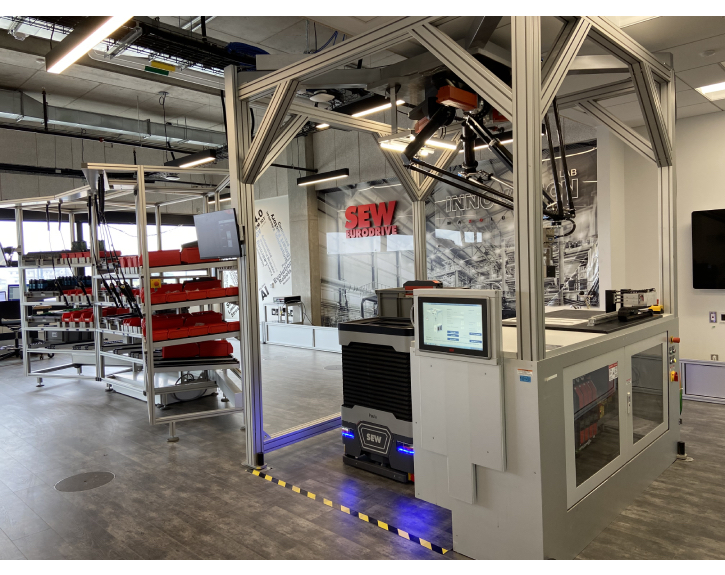
SEW-Eurodrive’s Modular System
SEW-Eurodrive is a manufacturing company founded in Germany in the 1930s. They specialize in a highly modular and configurable line of gear motors, complementary motion controllers and complete system solutions under the banner of Maxolution. The company’s modular system uses the pillars of Industry 4.0, interconnectivity, automation, machine learning, and real-time data to make products and support their customers via a network of over 70 assembly centers and dozens of manufacturing plants across the globe.
When a customer orders a drive solution through SEW-Eurodrive’s online portal, they can configure the product to meet their specific application and set the required delivery time. This sets the priority in the assembly facility, and using this data, the Systems Applications and enterprise resource planning software (SAP) plans the resources that will be used to fulfill the order.
A modern scalable process flow configured using “process modules” instead of fixed rigid assembly lines allows SEW-Eurodrive to run a much more flexible and efficient production. This in turn not only ensures rapid delivery of highly configurable products, but it also allows SEW-Eurodrive to retool and reorganize the entire process as rapidly as new technology and new product offerings are introduced in their portfolio. Additionally, a modular system provides rapid scalability when demand increases.
A warehouse that has all the components stored and available prior to assembly uses interconnectivity and automation to improve production with AVGs, cobots, Delta robots, and AR intertwined with pick by light racking. Based on the customer’s order, cobots can pick up parts from automated warehouses and deliver them to the assembly module.
Smart racking and AR can show the assembler which parts to pick and uses interconnected technology to indicate which tool to use and which parts get picked up for that assembly. In this system, nothing is missed. The assembler will see a head’s up display of the assembly process and will use real-time data to see the step-by-step assembly for a range of products.
Watch this video to see an animation of a Smart Factory in operation
Individual Customization
The Innovation Lab is all about demonstrating how these technologies can come together and be customized for individual production facilities, increase the productivity level of every plant, and even impact the basic job satisfaction of each worker. For example, the AR can allow workers to assemble a wide variety of highly complex and sophisticated components, varying from order to order, instead of monotonous repetitive assembly of the same product.
It can also be used for training as well as service functions of complex machinery. Seeing the AGVs (i.e., cobots), the delta 5 axis robot, the augmented reality heads up display, and smart pick by light racking working together in the Innovation Lab, it becomes evident how these solutions can have an impact on SMEs to improve throughput. The Lab is a scaled down version of a manufacturing facility. As Kurylo says,
“This is a small section of a much broader installation in a real manufacturing facility, consisting of many different elements. An automated storage warehouse would automatically dispense the required parts once the order is generated and prioritized within the IT system. From there these parts would be shuttled to each assembly module by the cobots, which in turn are configured to be used as smart workstations. Once the product is assembled to the customer’s specification, the cobot continues to a testing module, followed by an oil filling station, for example, if the product happens to be one of SEW-Eurodrive’s gear reducers, then to a packing and shipping module.”
– Konrad Kurylo,
Customization depends on what the facility needs, and the basic infrastructure available. These solutions are flexible and scalable and can be changed based on the needs, size, and configuration of the plant or facility. Every time the facility needs to retool, it is as easy as rearranging or adding additional modules. The cobots are easily reprogrammed for a new product flow route or retooled to handle a new product altogether. SEW-Eurodrive’s lab emphasizes the coexistence of robots and humans, hence the term “cobots.” These cobots work alongside their human counterpart instead of replacing them. Humans do the value part of the manufacturing, while the cobots perform the monotonous, labor intensive, or hazardous task.
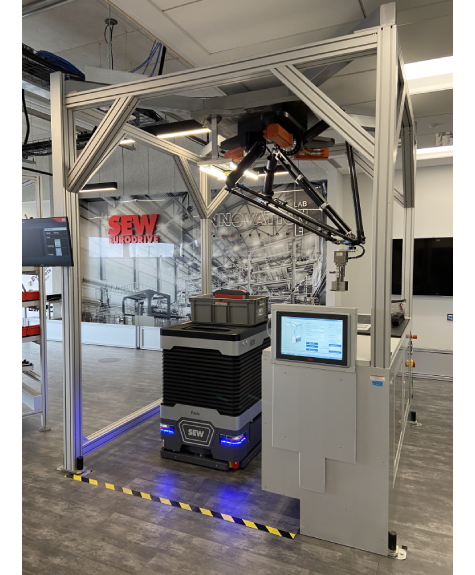
Seamless Integration for Existing Facilities
SEW-Eurodrive’s cobots can be powered continuously or periodically in key locations wirelessly. Contactless charging via induction eliminates the need and space for stationary charging stations.
It also eliminates the need for any extra vehicles, which would be required for a two or three shift operation, since the cobot is never offline due to stationary recharging. This could literally save the user $100’s of thousands of dollars in capital investment. The need for any onboard energy storage can be eliminated if the system is powered continuously, which is most advantageous in a progressive assembly of any product.
The solution can also incorporate ultra-fast supercapacitors, which can be recharged in about a minute (depending on the size). This would allow the cobots to deviate from the charging loop if the process required it. Charging spots or short charging lanes can also be placed strategically to ensure that they can charge without interfering with workflow or stopping production. When integrating these systems into a manufacturing facility, SEW-Eurodrive’s system planning team would analyze the layout and the process carefully to ensure optimal configuration to maximize the payback.
The cobot, smart pick by light racking, and the AR assembly instructions work seamlessly together to ensure that the assembly process is done with efficiency and accuracy. The assembly instructions based on the specific product version being put together are displayed on the worker’s headset. The smart racking (pick by light led system) will display which parts are to be picked. Because the entire process is connected, the smart racking knows which order is being processed, and which assembly instructions are to be displayed in the AR set. – Konrad Kurylo
Safety and Collaboration
The cobots configured as mobile workbenches have pre-settings based on which operator is working that shift and can be modified based on their height and reach so that they can work in the most ergonomic position. The cobots use LiDAR for navigation and follow a preplanned virtual path. There are two safety rated scanners which give the AGV or cobot 360 degrees of safety. Additional safety features are specific to the application, but with SEW-Eurodrive’s vast portfolio of safety-rated motors, brakes, encoders, drives, and controllers, the system can achieve SIL 2 or PL d safety requirements.
SEW-Eurodrive is driven by their customers’ success, and they have nearly a generation of experience in supporting them with customized products and solutions. Power transmission and automation being the core of their business, SEW-Eurodrive faces the same challenges as other suppliers in a global market, irrelevant of what is being manufactured.
More Information
Related Story
SEW-Eurodrive Dorval, Quebec Canada Investments
SEW-Eurodrive in Dorval Quebec Canada is now open. With an 88,000 square foot facility equipped with the largest inventory of parts in Canada. Their 24/7/365 unstoppable service is built right in, and their state-of-the-art paint line is now open.