Three Essential Factors for Servo Motor Sizing
June 4, 2024
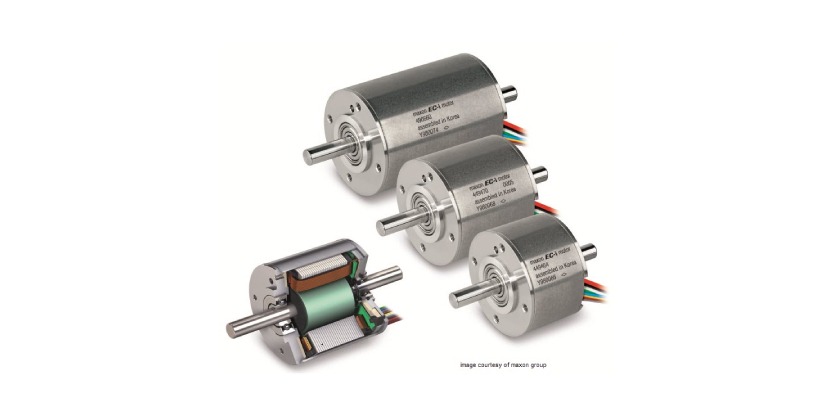
Selecting the right servo motor is a nuanced process vital for the optimal performance of a linear or rotary motion system.
While manufacturers provide helpful sizing tools, a deep understanding of the key parameters—speed, torque, and inertia—is crucial. This whitepaper expands on these factors, aiming to simplify this complex task.
Inertia: The Starting Point
Definition & Importance
Inertia refers to the resistance of a servo system to changes in its motion. It is a fundamental property that affects the performance and stability of the system. In a servo motor application, matching the motor’s inertia to the load’s inertia is crucial for maintaining system stability and responsiveness. A proper inertia match ensures that the servo system operates smoothly and efficiently, avoiding excessive overshoot, oscillations, and instability. This matching minimizes the strain on the motor and improves the overall performance of the system.
How to Calculate Inertia
Rotational Systems
In rotational systems, inertia is calculated using the formula: J=∑(m⋅r2) where:
- J is the inertia,
- m is the mass of each component,
- r is the distance from the axis of rotation.
This formula considers all the rotating parts of the system, including gears, pulleys, and the load itself.
Translational Systems
In translational systems, the load inertia is converted to the motor side using the gear ratio. The formula for this conversion is: Jload=m⋅r2/G2 where:
- Jload is the load inertia,
- m is the mass of the load,
- r is the radius or distance from the pivot point,
- G is the gear ratio.
This conversion is necessary because the gear ratio affects how the load inertia is reflected back to the motor.
Practical Tips
Balancing Inertia Ratios
- Aim for an Inertia Load to Motor Ratio between 1:1 and 10:1: This range is typically considered optimal for most servo motor applications. A 1:1 ratio means the motor inertia equals the load inertia, providing a balance between control and responsiveness. Ratios up to 10:1 are acceptable for less demanding applications where some loss in responsiveness can be tolerated.
Application-Specific Considerations
- High-Precision Applications: For applications requiring high precision, such as CNC machines or robotic arms, a lower inertia ratio (closer to 1:1) is preferable. This ensures precise control and minimizes errors due to inertia mismatch.
- Energy-Efficient Systems: In systems where energy efficiency is a priority, a higher inertia ratio (closer to 10:1) might be acceptable. These systems benefit from reduced energy consumption, even if it means a slight compromise in precision.
Additional Tips
- Use Lightweight Materials: For components that contribute to the load inertia, consider using lightweight materials. This can reduce the overall inertia and make it easier to match with the motor inertia.
- Minimize Load Distance: Reducing the distance (radius) from the axis of rotation for load components can significantly decrease the inertia, leading to a more responsive system.
- Consider the Entire System: When calculating inertia, consider all components that contribute to the load, including any fixtures, tools, and additional attachments. This comprehensive approach ensures an accurate inertia match.
By carefully considering and calculating the inertia, engineers can ensure that the servo motor system is both stable and responsive, leading to improved performance and efficiency.
Speed: Ensuring Dynamic Performance
Understanding Speed Requirements
Speed in servo motor applications is a critical factor that determines the system’s ability to meet the demands of various tasks. The required speed must be sufficient to complete tasks within the desired cycle times without sacrificing precision. If the speed is too low, the system may not be able to meet production requirements. Conversely, if the speed is too high, it can lead to excessive wear and potential system instability.
Calculating Needed Speed
To determine the required speed for a specific application, consider the following factors:
Nature of the Task
Identify the maximum speed needed during operation by understanding the task requirements. For example, in a conveyor belt system, you need to determine how fast the belt needs to move to transport items from one point to another within the required time frame.
Cycle Times
Calculate the total distance and the time needed to complete one cycle. This involves determining how far the load needs to move and how quickly it must complete the movement. Use the formula: v=d/t where:
- v is the speed,
- d is the distance,
- t is the time.
This calculation helps in determining the minimum speed required for the servo motor to achieve the desired performance.
Selection Advice
Selecting the Right Motor
- Achieving Required Speed: Ensure that the selected motor can achieve the required speed without exceeding its maximum rated speed. This is crucial to prevent motor damage and ensure reliable operation. Review the motor’s speed-torque curve to verify that it can provide the necessary torque at the required speed.
Accuracy and Efficiency
- Balancing Speed with Precision: It’s important to balance the motor’s speed with its ability to maintain accuracy. High-speed operation can sometimes lead to reduced precision due to factors like mechanical vibrations and control system limitations.
- Avoiding Maximum Speed for Extended Periods: Running the motor at its maximum speed for prolonged periods can lead to increased wear and overheating. To prevent this, select a motor with a speed rating slightly higher than your required speed, allowing the motor to operate within a comfortable range without being over-stressed.
Practical Tips
- Use Speed Reduction Mechanisms: If the required speed is beyond the capability of available motors, consider using speed reduction mechanisms such as gearboxes or pulleys. These can help achieve the desired output speed while keeping the motor within its optimal operating range.
- Consider Acceleration and Deceleration: In applications requiring rapid changes in speed, consider the motor’s acceleration and deceleration capabilities. Ensure the motor can ramp up to the required speed quickly without excessive overshoot or oscillation.
- Match Speed with Load Characteristics: Different loads have different speed requirements. Ensure the motor’s speed is well-matched to the characteristics of the load. For instance, heavy loads may require slower speeds to maintain control, while lighter loads can be moved more quickly.
Torque: The Driving Force
Torque Explained
Torque is the rotational force produced by the servo motor, essential for driving the load in various applications. It determines how much force the motor can exert to rotate or move an object. There are two primary types of torque to consider:
- Continuous Torque: The constant torque that the motor can provide without overheating. This is the torque the motor can sustain during normal operation without thermal overload.
- Peak Torque: The maximum torque the motor can deliver for short periods. This is typically required during acceleration or when overcoming initial static friction.
Calculating Torque Needs
Accurately calculating the torque requirements is crucial for selecting the right servo motor. Here are the steps to determine both continuous and peak torque:
Continuous Torque
To calculate continuous torque, use the formula: T=F⋅r/G where:
- T is the torque,
- F is the force,
- r is the radius or distance from the axis of rotation,
- G is the gear ratio.
This formula helps in determining the torque needed to maintain constant motion of the load without overheating the motor.
Peak Torque
Calculating peak torque involves considering the highest load the motor will encounter and any dynamic forces during acceleration. Peak torque can be significantly higher than continuous torque due to the need to overcome inertia and initial resistance. Factor in the dynamic forces using the following considerations:
- Acceleration and Deceleration: Include the forces required to accelerate and decelerate the load.
- Load Variations: Consider any variations in load that might require additional torque.
Choosing the Right Motor
Balancing Torque and Other Factors
When selecting a servo motor, it’s crucial to ensure that it provides adequate torque for the application while considering other factors such as size and cost. Here are some guidelines:
- Adequate Torque Provision: Ensure the motor’s continuous torque rating meets or exceeds the application’s requirements. For peak torque, the motor should be capable of handling short bursts without overheating.
- Size and Cost Considerations: While selecting a motor, balance the torque requirements with the motor’s size and cost. Larger motors with higher torque ratings are generally more expensive and might not be necessary for all applications.
Implications of Incorrect Sizing
- Under-Sizing: Choosing a motor that cannot provide sufficient torque can result in several issues, including:
- Insufficient Force: The motor may not be able to move the load, leading to performance issues.
- Overheating: Continuous operation at or near the motor’s maximum torque capacity can cause overheating and potential motor failure.
- Over-Sizing: Selecting a motor with much higher torque than required can lead to:
- Unnecessary Energy Consumption: Larger motors consume more power, leading to increased energy costs.
- Increased Costs: Higher initial costs and potentially higher maintenance costs due to the larger motor’s complexity and size.
Practical Tips
- Torque Margin: Always consider a margin of safety when calculating torque requirements to account for unforeseen variations in load or operating conditions. A good rule of thumb is to consider is a safety margin of 20% to 30% for a servo motor, and 30% to 50% for a stepper motor.
- Motor Specifications: Review the motor’s specifications carefully, including its torque-speed curve, to ensure it can deliver the required torque at the desired speed.
- Environmental Considerations: Factor in the operating environment, as temperature, humidity, and other conditions can affect motor performance and torque delivery.
By carefully considering these factors and following these guidelines, engineers can select a servo motor that meets the speed requirements of their application while maintaining accuracy, efficiency, and reliability.
Related Story
Ask An Expert at Electromate
If you have questions about any of Electromate’s product offerings, please book a consultation with one of their Sales Engineers in your area. If you just have a question about one of their motion control or robotic lines, simply fill out the Ask an Expert form below. They strive to get you an answer ASAP.