Rockwell Automation: How Connectivity and Digitization are Transforming Mine Operations
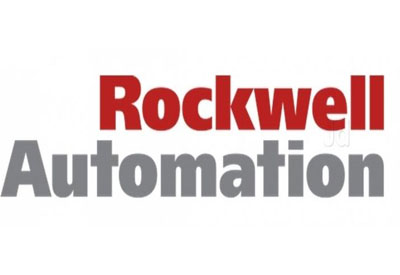
March 26, 2018
By Sujeet Chand, Senior Vice President of Strategic Development and Chief Technology Officer, Rockwell Automation
I was recently invited to speak at the Future Mining Summit 2017 event hosted by the Global Mining Standards and Guidelines Group. The two-day conference was held in early December 2017. The venue was a fitting one: 20-metres below ground in Stockholm, Sweden at Epiroc’s test mine.
In addition to my presentation, the event hosted mining companies from around the world, equipment providers, and technology thought-leaders. Presenters shared key trends they’re noticing in the mining industry, as well as opportunities for growth and improvement:
- Operations challenges arise as mines get deeper and deeper. Machine utilization at depth is relatively low – around 50-60%, compared to 80% in an open pit mine. There’s a need to better track and optimize machine use below ground.
- There are too many “Clouds.” With each automation vendor and OEM providing a separate instance of cloud data, it’s difficult for mining companies to aggregate data across systems and identify trends. Mining companies are interested in open systems so they can better own and leverage all of their data.
- Everyone is talking about Block Chain. Block Chain is not being utilized in mining today, but there are potential applications to enhance traceability, recordkeeping, and security of transactions across the supply chain.
- Fossil-free mining. Battery operated equipment is picking up steam (pun intended) as mining companies strive to minimize their environmental footprint.
- The safe connected mine (PDF). Mining companies are seeking strategies to implement greater mobility and use of wireless in their mines to enhance worker safety and optimize production.
I was also given a chance to share my insights about the future of mining, based on broad market trends I’ve observed as well as conversations I’ve had with our customers.
Insight #1: Mining companies don’t need to collect more data, they need to collect the right data. When you’re running a man-made process, there are only so many variables and meaningful data correlations – most of which we already know to expect.
And we also know that there are some pieces of data that will never connect or correlate. To prevent amassing vast, unusable amounts of data, mining companies will begin seeking ways to pre-analyze data before sending it to the Cloud, so only relevant information is moved.
As OEMs insert more and more intelligence into their machines, mining companies will be increasingly able to perform this pre-analysis.
One of the OEMs that we work closely with in the mining industry, Metso, is already moving down this path with their rock crushing machines: they’re transferring only key pieces of data to the cloud to allow for comparison with other rock crushing equipment.
This enables mining companies to find optimization opportunities based on performance measurements from across multiple sites. It also prevents them from wading through a lake of unusable data.
Insight #2: Analytics in the future will be distributed, and will leverage scalable computing. Analytics can take place in the Cloud, at the server layer, or right at the device level. In the future, mining companies will seek strategic methods of performing ‘right size’ analytics to solve their problems.
Insight #3: Safety and security are converging. As virtual threats increase in severity and frequency, physical safety and data security are merging into a single objective.
This is a trend I’ve noticed across all industries. Companies must begin drafting internal processes with this in mind: placing the same level of emphasis on virtual mine security as they do on physical mine safety.
This topic generated a lot of conversation, and GMSG took an action item to create a working group to help mines better plan for the convergence of safety and security.
Changes in the way we think about data collection and analysis will have a big impact on the mining industry. And as more and more of our information is transferred between devices and to the Cloud, a subsequent need for increased data security will change the way we think about worker and company safety.
I’ve already begun to see some of our clients adapting to these trends. How do the trends shared at the GMSG summit match up with what you are seeing in the industry? Are you taking steps to address any of the challenges we discussed at the event? Drop me a note via email or LinkedIn.
And of course, if you’d like more information about the solutions we provide for mining companies, visit our mining automation web page.