Understanding Industrial Relay Contact Configurations: NO, NC, SPDT, and DPDT
November 19, 2024
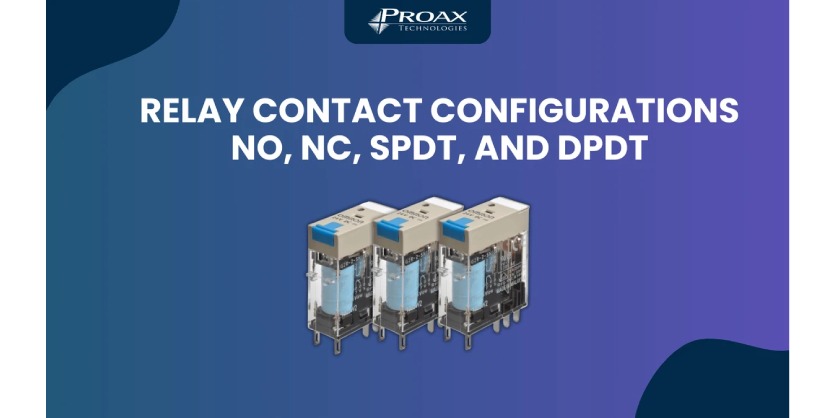
Relays serve as the backbone of industrial control systems, enabling the control of high-power circuits using low-power signals. Understanding different relay contact configurations is crucial for designing effective control systems. Let’s explore the various types of relay contacts and their applications in industrial automation.
Basic Contact Types and Their Applications
The foundation of relay operation lies in their contact arrangements. Normally Open (NO) and Normally Closed (NC) contacts form the basic building blocks of relay switching.
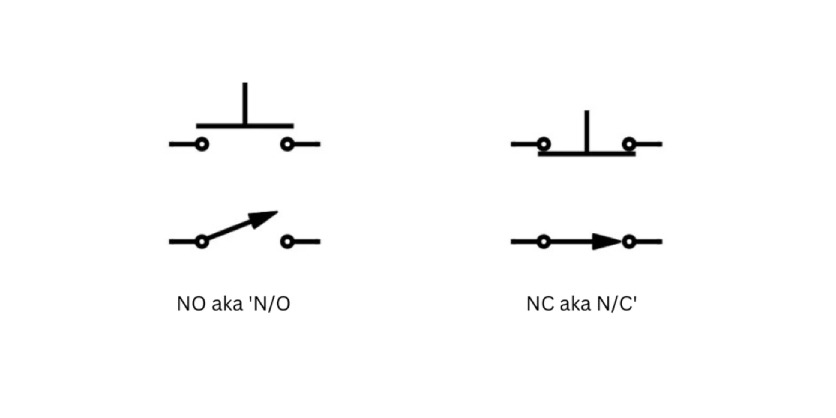
Normally Open (NO) Contacts
When you’re designing a circuit that needs to turn on a device or start a process, NO contacts are your go-to choice. These contacts remain open until the relay is energized, making them perfect for controlling motors, lights, or process equipment. Think of them as a light switch that’s normally off until you flip it.
Normally Closed (NC) Contacts
NC contacts play a crucial role in safety and monitoring applications. These contacts maintain a closed circuit until the relay is energized. They’re particularly valuable in emergency stop circuits and fault monitoring systems, where a break in the circuit needs to trigger an immediate response.
Advanced Contact Configurations
SPDT (Single Pole, Double Throw)
SPDT relays offer versatility by combining both NO and NC contacts with a common terminal. This configuration allows you to control two different circuits with one relay, making it ideal for applications like:
- Switching between main and backup power sources
- Reversing motor directions
- Alternating between two different signals
- Creating interlock systems
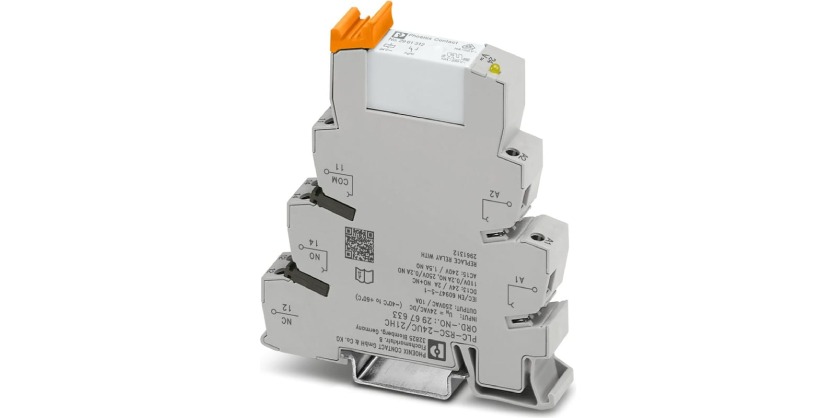
DPDT (Double Pole, Double Throw)
DPDT relays take versatility a step further by providing two sets of SPDT contacts. This configuration enables sophisticated control schemes where multiple circuits need to be switched simultaneously while maintaining isolation between them.
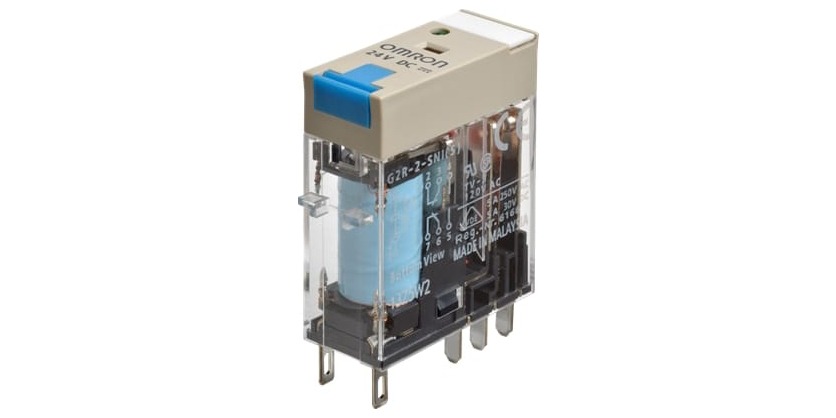
Modern Relay Technologies
Force-Guided Contact Relays
Force-guided relays represent a significant advancement in safety relay technology. These relays ensure that NO and NC contacts cannot be closed simultaneously, making them essential for safety-critical applications. They provide mechanical linkage between contacts, ensuring reliable operation in safety systems.
Safety Relay Units
Modern safety relay units combine traditional relay functionality with advanced monitoring capabilities. These devices offer features like:
- Dual-channel monitoring for redundancy
- Automatic fault detection
- Configurable reset modes
- Status indicators for quick diagnostics
Solid State Relays
For applications requiring frequent switching or dealing with sensitive loads, solid state relays offer several advantages:
- Silent operation
- No mechanical wear
- Zero-crossing switching for reduced electrical noise
- Long operational life
- Compatibility with both AC and DC loads
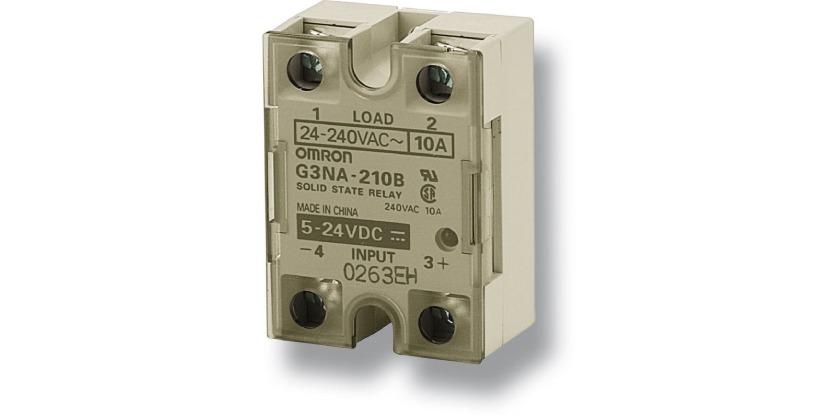
Choosing the Right Relay Configuration
When selecting a relay configuration, consider these key factors:
Application Requirements
Start by evaluating your specific needs:
- Switching voltage and current requirements
- Switching frequency
- Environmental conditions
- Safety requirements
- Control system compatibility
Installation Considerations
Think about the practical aspects:
- Available mounting space
- Wiring accessibility
- Maintenance requirements
- Heat dissipation needs
Common Applications in Industry
Different relay configurations find their place across various industrial applications:
Machine Safety Systems
Safety relays with force-guided contacts ensure reliable emergency stops and guard door monitoring. They provide the redundancy and monitoring required by safety standards while maintaining fail-safe operation.
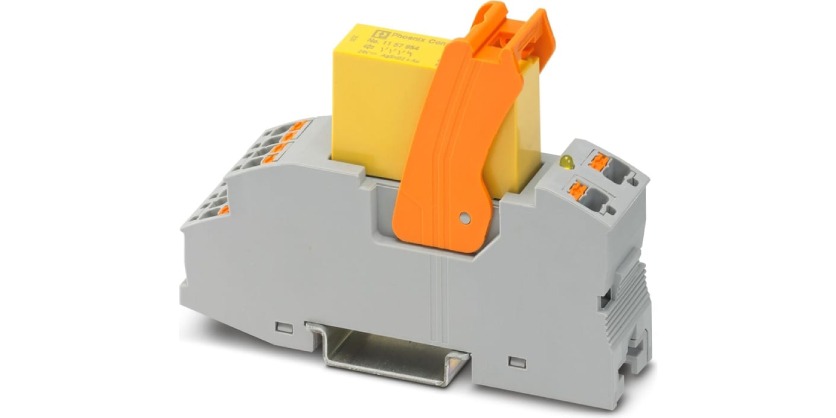
Process Control
In process control applications, relays handle tasks ranging from simple on/off control to complex sequencing operations. SPDT and DPDT configurations allow for sophisticated control schemes while maintaining signal isolation.
Power Distribution
Solid state relays excel in power distribution applications, offering reliable switching for both resistive and inductive loads. Their zero-crossing switching capability helps reduce electrical noise in sensitive environments.
Looking Ahead: The Future of Relay Technology
The relay industry continues to evolve, incorporating features like:
- Enhanced diagnostic capabilities
- Network connectivity
- Improved energy efficiency
- More compact designs
- Advanced monitoring functions
Ready to Find the Right Relay?
Whether you need safety relays for critical applications, solid state relays for frequent switching, or traditional electromechanical relays for general purposes, Proax offers a comprehensive selection of industrial relays to meet your needs. Contact their team for assistance in selecting the optimal relay configuration for your application.
Related Story
Power Supply Options for Your Industries
The dependability and functionality of electronic devices and systems are greatly dependent on power sources in today’s technologically advanced society. Power supply guarantees that electronic equipment, ranging from industrial machinery on factory floors to smartphones in our pockets, receives the precise, consistent, and secure power required for optimal operation.
Power supply knowledge is essential whether you’re a consumer trying to figure out how your devices are fueled, an engineer creating intricate systems, or a business owner looking for dependable solutions for your operations. This article will discuss power supply basics, types, uses, and important factors to consider when choosing the best power supply for your requirements.