Q&A With HELU: Robotic Dress Packs
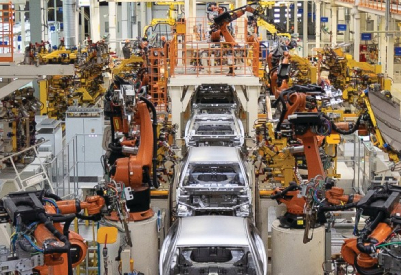
October 17, 2022
Robots are an integral part of the manufacturing industry worldwide to the extent that they are indispensable. In production, robots and cobots frequently encounter each other, working and interacting side by side with humans, but also performing tasks independently. The latest industrial robots move in a three-dimensional space and can therefore perform a wide variety of tasks. In order to ensure optimum system performance, the use of a dress pack is required to keep a robot running as frequently as possible. Regional Sales Manager Gordon Post discusses some of the questions he hears in the field about robotic cable protection systems.
Q: What is a robotic dress pack and what is its primary function?
A: Dress packages (a.k.a. dress outs, umbilicals, utility supply systems, etc.) provide an organized way of protecting the fill package from environmental hazards. They are tasked with protecting, managing, securing and guiding cables and hoses over millions of work cycles. As a ready-to-install assembly that is uniquely designed to match the application, dress packs are vital in reducing preventative maintenance downtime. Any industrial robotic application where an End Of Arm Tool (EOAT) needs various supply lines such as servo power, welding power, water or air supply, Ethernet communication, etc. would be in need of a dress pack.
Q: What typically is required in a fill package when dressing out a robot?
A: In order to mitigate failures in the best way possible, it is important to select solutions from an application-specific, as well as an overall system, point of view. In other words, each robot has a task to perform. Therefore, dress packs should be specifically designed around the complete work cycle of each task.
If we use resistance spot welding (RSW) as an example, you will have an insulated cable assembly, which consists of two high-power cables and a ground cable, that connects to the spot-welding gun. Furthermore, you would need water in and water out hoses, which depending on the customer’s configuration, could be two or three hoses. The weld gun actuator uses a servo motor that requires a double-ended motor power and feedback cable assemblies. Finally, depending again on the customer’s requirements, a three-conductor cable for secondary voltage feedback is used as well. All of these cables and hoses will go inside plastic conduct that guides them around the robot and helps protect them from getting tangled up as the robot twists and turns and in this case from any weld spatter that might occur during the welding process.
Dress packages provide an organized way of protecting the fill package from environmental hazards
Q: For the automotive industry how does the dress requirement for robots differ from non-automotive? What makes this industrial application unique?
A: The automotive industry uses these processes as well, but also introduces other stressors to the robot, which adds to the factors that must be taken into account when designing a dress pack. Automotive manufacturing uses a lot of different joining solutions that include spot welding, riveting, laser welding, stud welding, projection welding, adhesive dispense, MIG welding, and more that require specific robot dress cables and hoses for each application. Additionally, robots are used in the paint shop, which exposes them to other chemicals – lacquers, paint, etc. – that can be detrimental to operations if the cables and hoses are not properly protected.
To sum up, the dress packs have to endure a lot of abuse in the automotive manufacturing environment and must be able to hold up to avoid any downtime.
Q: Serviceability and cost are important for dress pack installations, what other factors make a manufacturer/supplier stand out when designing a robotic cable protection system?
A: As discussed previously, initial design and development should encompass an application-specific, as well as an overall system, point of view. Not all “out-of-the-box” systems, which are based on a robot model, are suited for the application the robot is being used. Having a manufacturer that is willing to start from scratch and understand the customer’s requirements for the cables, connectors, pinouts, hose types, and overall protection system mounting and routing for each application is a plus. Supporting the integrators or robot company(s) for the initial stages is key to providing accurate mechanical and electrical prints so that the installation goes smoothly. This is critical so that all the cables plug in correctly and all the signals work properly.
Additional areas that make a supplier stand out are managing the orders for on-time delivery, technical training, and support for optimization of the dress packs.
Q: Based on current trends, what advancements in dress pack technology are occurring?
A: There are more robots being deployed in industrial applications than ever before when you look at heavy-duty robots and lightweight cobots out in the field. More robots are being used in manufacturing for vision and collaborative applications so this will drive more robot dress packs to be developed in order to support these applications.Another trend that is being monitored is inside dress options for the hollow arm robot models that are being used for such applications as spot welding or material handling. The hollow arm allows for a completely internal cable routing.
Initial design and development of a robot’s dress pack should encompass an application-specific, as well as an overall system, point of view. Not all “out-of-the-box” systems, which are based on a robot model, are suited for the application the robot is being used
Q: Can you discuss the pros and cons of external dress packs versus internal dress pack systems?
A: External dress packs are quick to assemble as all mounting areas are easily accessible. They are also easy to service in the event of a cable or hose failure e.g. torn conduit can be fixed using an impact protector for minimal downtime. Conversely, external dress packs are exposed causing them to take up more space, and if not suited for the application can rub on the robot, tooling or other robots. Understanding the entire system and application to build a customer-specific solution can minimize these risks compared to some “one-size-fits-all” or “out-of-the-box” solutions.
Internal dress packs are protected using the robot arm cavity to avoid any unwanted rubbing and strenuous environmental effects. Because they use the robot’s internal structure, the overall system has fewer parts, such as no spring return for example. On the downside, internal dress packs are more difficult to assemble since space is restricted and in the event of a cable or hose break, they can take longer to repair.