Q&A With HELU: Cable Glands
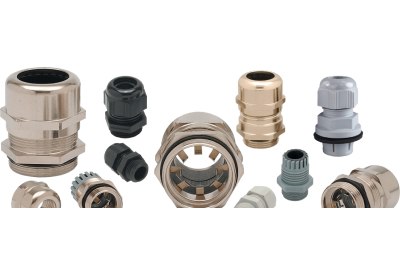
October 3, 2022
Whether you call them cord grips, cable strain reliefs, or cable fittings the cable gland is an important piece within the cable system. Several factors need to be considered when choosing the correct type of cable gland for industrial applications. Doing your homework in advance will prevent unnecessary problems, such as time wasted on-site because the incorrect size or thread type was purchased. Regional Sales Director John Scott gives us the answers to some of the questions he hears in the field about cable glands.
Q: What are cable glands?
A: A cable gland is defined as a “mechanical cable entry device” that is used in conjunction with cable for wiring electrical, instrumentation and control, and automation systems, including lighting, power, and data. Their main function is to act as a sealing and terminating device to ensure the protection of electrical equipment and enclosures.
Q: What types of materials are cable glands made from?
A: Cable glands are made from a range of materials, including:
- •Polyvinyl chloride (PVC) — a flexible and non-reactive plastic
- •Polytetrafluoroethylene (PTFE) — a plastic that is highly resistant to chemicals and similar substances
- •Nylon — a tough, multi-purpose material with strong resistance to pressure
- •Metal — steel, stainless steel, aluminum, or brass
- •Synthetic rubbers
Q: What parts make up a cable gland?
A: The specific parts depend on the type of cable gland but most will have what is referred to as a cap nut (1), molded seal (2), clamping seal insert (3), and gland body (4). Other components that one would see are the metallic contact tines or brush (EMC glands), O-ring (5), and locknut (6) if the enclosure entry is not threaded.
Q: How do I determine what size cable gland to use based on cable size?
A: For standard glands, the key is the outside diameter (O.D.) of the cable in question. Each cable gland size can take a varying range of cable sizes based on the thread type chosen. Some gland manufacturers provide reducing seals to increase the O.D. range a gland can accept. For EMC glands, it’s recommended to choose cable glands with a lower clamping range that is sufficiently smaller than the cable’s outer diameter to ensure there is proper contact between the EMC contact element and the cable shield.
Q: What are available thread types and what is the purpose of each?
A: When it comes to cable glands, choosing the right thread type for the job makes all the difference. The success of your application relies on proper installation, which is why choosing the correct thread is so important. The three mos tcommon thread types are metric, NPT and PG.
Metric threads are the most common thread type used around the world. Metric threads are characterized by their major diameter and pitch, both expressed in millimeters. For example, an M20 x 1.5 fitting has a thread diameter of 20 mm and a pitch of 1.5 mm. You would want to use metric threads on exported equipment or on projects that could beused worldwide. NPT stands for National Pipe Thread and is the US standard for tapered threads on connectors and fittings.
NPT threads are usually longer than metric or PG and taper toward the end. The taper rate for all NPT threads is 1/16 in. NPT threads are designed to create a liquid-tight seal upon tightening.The flanks of the threads compress against each other, which allows them to form a seal when torque is applied. You want to use NPT threads in applications that require an effective seal from liquids, gases, and steam.
PG stands for Panzer-Gewinde and is an older German thread type. PG threads are straight threads designed with a smaller thread depth and larger flank angle. The 80° angle of the PG thread gives it a shorter profile than the more common 60° angle found in metric threads.
Q: Why should I use a cable gland instead of just putting the cable in an entry hole?
A: Not using cable glands in an installation can create a host of problems as there is no protection for the cable or the components within the enclosure where the cable will ultimately be installed. By using them customers can accomplish several things at once:
- •Secure cables in place and prevent them from being twisted or accidentally pulled out.
- •Providing an airtight seal to keep out dust, dirt, water, and moisture – a key function with electrical equipment.
- •Fortifying the cable against strain.
- •Protecting the vulnerable end of the cable from damage.
- •Ground electrical cables and cut the risk of shock and electrocution (EMC glands only).
Q: What are cable glands IP rated and why is it important?
A: An ingress protection (IP) rating represents the level of protection provided by a device against the intrusion of solid objects and liquids. An IP rating usually has two numbers: the first number (1-6) represents the level of protection from solid materials, and the second number (1-8) represents the level of protection from liquids. The higher the number, the better protection that is provided. Having the gland rated to match the final product is important because when a manufacturer desires an IP rating for their product, they must have it tested by a certified, independent company. That company assigns a numerical IP rating to the product to signify how well the item protects against intrusion of solids and liquids. If a given cable gland’s IP rating does not match the equipment it is being used on, then the equipment or enclosure has the potential of being de-rated.
Q: What are some key considerations when selecting a cable gland for an application?
A: While choosing cable glands, some top considerations would be:
- •Is it suitable for the size and type of cable used?
- •Is it going to be used indoors or outdoors?
- •Is it going to be used in an explosive or hazardous environment or a safe industrial zone?
- •Will it be installed in a place where the surroundings are dusty or damp?
- •Is there any presence of corrosive materials or explosive gases nearby?
- •Is a shielded cable being used that will need to be grounded to the enclosure?
- •Are there any special environmental requirements related to corrosion protection?
- •What is the material of the mating electrical enclosures to eliminate dissimilar metals where possible or if required?
- •Does a protective plating or coating need to be applied tothe cable gland, e.g. nickel plating?
- •What is the type and size of the cable entry hole in the mating electrical equipment?
- •What is the wall thickness of the enclosure or gland plate, as a longer cable gland thread may be required?
- •What is the IP rating of the electrical equipment or sitestandard that must be maintained?
- •Is an entry thread sealing washer required to meet the IP rating?
- •Are fixing accessories such as locknuts or serrated washers required?
- •Is a grounding locknut or earth tag required?
- •Is a thread conversion adapter/reducer required to complete the installation?
- •Are any stopper plugs required to close unused cable entries?