Prioritizing Safety: Understanding ISO 15066 and the Importance of Cobot Safety Validation
January 8, 2024
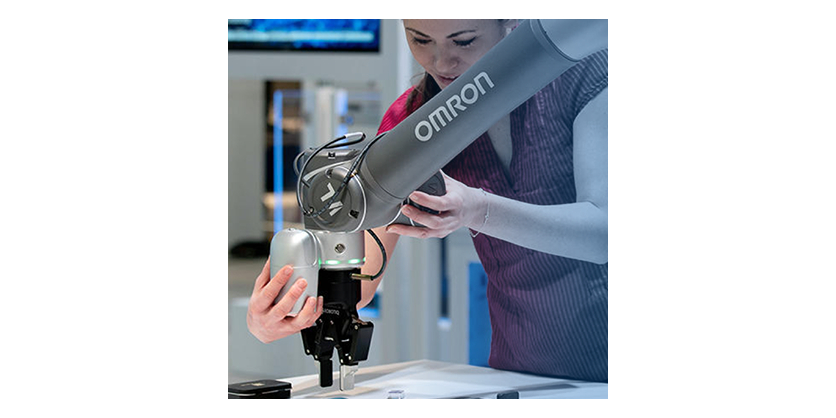
Collaborative robots, or cobots, have revolutionized the manufacturing industry by working alongside humans to increase productivity and efficiency. However, with the growing prevalence of cobots, it is crucial to prioritize safety and conduct thorough testing and validation to ensure safe operations. In this blog post, Omron explores the importance of force and pressure measurements and how it can help safeguard your team, minimize risks, and reduce liabilities.
Understanding ISO 15066 and its role in cobot safety
While collaborative robots are designed for close interaction with humans, there is always a potential for accidents and injuries if proper safety measures are not in place. Unsafe cobot operations can lead to severe consequences, including worker injuries, regulatory fines, downtime, legal fees, and increased insurance costs.
The potential risks associated with unsafe cobot operations should not be underestimated. One of the most significant risks associated with using cobots is the potential for excessive force or pressure which can lead to a range of problems, from minor traumas like sprains and strains to more severe incidents such as broken bones.
Understanding and following relevant safety standards is crucial for safe cobot operations and necessary to ensure compliant operations and avoid costly consequences. ISO 15066 is one of the safety standards providing guidelines for the safe use of collaborative robots. It specifically focuses on the limits for force and pressure that cobots can exert during operation. Adhering to ISO 15066 helps ensure compliant operations, protect employees from harm, and minimize liabilities.
Ensuring cobot compliance with ISO 15066
Regular assessments and testing should be performed to ensure cobot operations are within permissible limits according to ISO 15066. By conducting force and pressure testing, you gain essential data which identifies potential safety issues with cobot operation and allows you to proactively make necessary modifications to your cobot settings, minimizing the risk of injuries and accidents in the workplace.
Properly calibrated and well-maintained equipment along with accurate force and pressure measurements are essential to providing a safe workplace as required by OSHA. When done correctly, prioritizing cobot safety can create a safer work environment while still achieving maximum efficiency. A safe work environment not only boosts productivity but also enhances employee morale and satisfaction.
By partnering with a trusted provider, you can ensure that your cobots operate within safe limits and comply with ISO 15066. For more information about force and pressure measurements, we invite you to contact Omron regarding our Cobot Safety Validation service.
More Information
Download Omron’s cobot safety validation flyer
Related Story
Omron’s Robotic Solutions: Thousands of Possibilities
Robots can improve the productivity of many industries and processes. They can handle a variety of tasks, such as laborious or repetitive work, and can dramatically improve processes in industries such as machine tending, assembly, packaging, and other manufacturing activities. Moreover, they can handle routine operations, allowing employees to perform higher-value tasks.
This article will look at a selection of Omron’s robots and robotic solutions, such as autonomous robots and collaborative robots, and will explore how these products can be integrated into facilities to improve productivity. It also discusses the next evolution in factory automation: MoMa’s, or Mobile Manipulators – the growing trend of having collaborative robots mounted onto AMRs to achieve new levels of automation.