Put to the Ultimate Test – Part 3: Drag Chain Tests
July 12, 2024
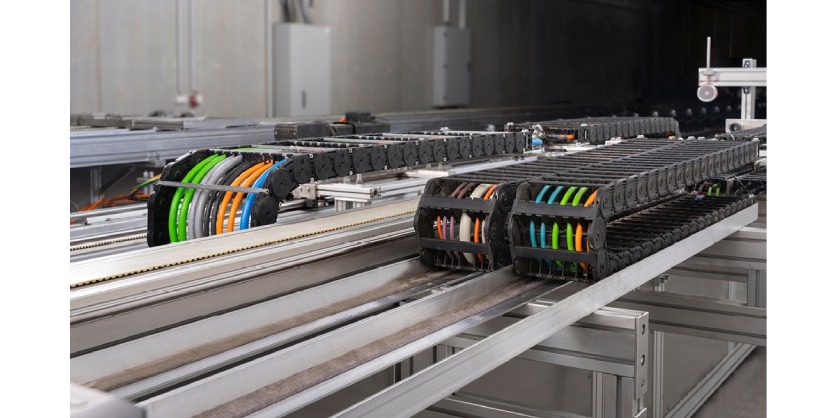
During the development of their cables and wires, HELUKABEL vigorously test each product in their testing laboratories. In the third part of their series, they’ll introduce you to their drag chain tests.
Drag chains – also known as energy chains – are ideal for guiding and protecting electrical cables, and hydraulic and pneumatic hoses in moving machinery and equipment. They are used in situations where machine components are moving back and forth – for example in lifts, machine tools, and in the control stations of high-bay warehouses. The guide ensures that the smallest permissible bending radius for the cables is not exceeded, thereby avoiding damage.
Drag chain cables are constantly moving – often non-stop around the clock – making fast accelerations, tight bending radii, and continuous abrasion ongoing challenges. There are many applications where drag chain cables have to withstand millions of bending cycles undamaged, and at the same time be resilient to oil, heat and chemicals. High-quality conductor insulation and jacketing materials are essential to reduce the risk of abrasive wear that might damage the cables and lead to expensive machine outages.
The HELUKABEL portfolio contains special drag chain cables for moving applications in drag chains. To ensure that they meet the stringent demands of day-to-day use, they subject them to extensive testing in their testing laboratory in Windsbach, Germany. They have a variety of drag chain test facilities with traverse paths ranging from 0.9 to 40 meters. With accelerations of up to 50 m/s², velocities of up to 10 m/s, and different chain radii, they can realistically simulate diverse operating conditions. The aim of these tests is to prove that the copper wires, conductor insulations, stranding, and outer jacketing withstand constantly changing bending stresses undamaged and therefore meet their high quality standards.
Only cables that fulfill every one of their strict requirements find their way into their product portfolio. Therefore, their drag chain cables are HELUKABEL’s contribution to ensuring that plant and machinery are able to operate both cost-effectively and efficiently over the long term, even in harsh conditions.
Click here to read more about the drag chain test equipment they use and the performance criteria they can evaluate.
Ask the Expert
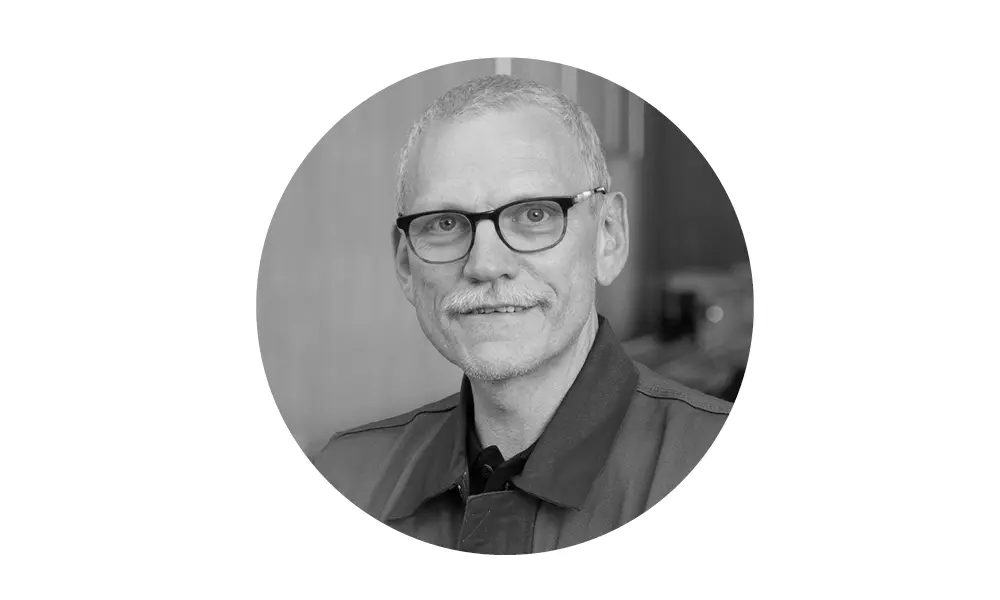
What do you have to pay particular attention to when choosing a drag chain cable?
There are several criteria: firstly, the copper wires should be finely stranded, i.e., are conductor class 5 / Class K or M (AWG). The individual conductors should be stranded with the smallest possible lay length to optimize flexibility.
The design of the jacketing and insulating materials must take into account the required movements as well as the relevant ambient conditions. It is also recommended to keep the number of conductors to a minimum: if the number of conductors increases, a special stranding process is required. This increases the diameter of the cable which might lead to space problems in the chain.
Furthermore, drag chain cables must be designed to be as light as possible. The drag chain has to carry its own weight as well as that of the cables inside it. The lower the overall weight, the greater the dynamic performance and the less energy needed to get the system moving.
How are the cables aligned in a drag chain?
For optimal alignment, it is important to define beforehand precisely which cables and other components such as pneumatic and hydraulic hoses will be used and to select the drag chain accordingly. Cables and hoses should be loosely placed beside each other in the chambers of the drag chain and, ideally, kept apart from one another using dividers. Maintaining a specified clearance between the cable and the divider ensures that the cables can move freely. Symmetrical weight distribution in the chain helps to ensure smooth operation. Additionally, the cables in each section should all have the same jacketing material to avoid unnecessary abrasion.
Related Story
Put to the Ultimate Test – Part 2: Bending Tests by HELUKABEL
In dynamic applications typical to mechanical and plant engineering or drive and automation technology, cables and wires are frequently subject to mechanical bending stresses. Although these stresses also occur in static installations, they are much higher in dynamic applications because the force and direction of movement are constantly changing. Such situations are pure stress for the cable. The wires, conductor insulation and jacketing material are squeezed on the inside and stretched on the outside, and the cable can tear. Degradation, up to and including cable damage, leads to faults and functional failures.