Overcoming the Top Two Barriers to Predictive Maintenance
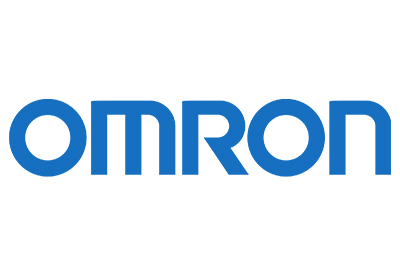
July 16, 2021
Predictive maintenance is a powerful condition-based strategy that lets manufacturers remotely monitor critical machinery using IIoT sensor devices that supply real-time data like voltage, vibration and temperature. By supplying this information in real-time, predictive maintenance solutions help companies cut maintenance costs and respond quickly to issues.
Given these enormous benefits, why would any manufacturer hesitate to implement this strategy? Let’s take a look at a couple of reasons for this hesitation and see how Omron technologies can make the transition easier.
Reason #1: Predictive maintenance has a high learning curve and requires IIoT infrastructure.
New technologies generally require some new knowledge. For manufacturers that have limited training resources, migrating to a completely new strategy can be daunting. Furthermore, the strategy is based around Industrial Internet of Things (IIoT) devices that require robust connectivity, and not all manufacturers have the means to invest in that infrastructure.
Manufacturers lacking IIoT resources and the ability to train their team on a variety of new technologies can still take advantage of turnkey predictive maintenance solutions that require little to no advanced knowledge. Omron’s motor condition monitoring devices and other technologies are designed to be user-friendly, standalone solutions.
Reason #2: The initial investment costs may seem too large given the expected payoffs.
Initial investment costs for predictive maintenance solutions vary widely from application to application, but they can sometimes be quite high. In these situations, it’s important for manufacturers to evaluate the cost of downtime and see whether this may actually outweigh the cost of implementing several new technologies.
The automotive industry is the one for which downtime costs are most pronounced, and the machinery runs on large motors that are quite expensive to replace. The larger the motor, the more likely it is to be moving critical equipment, such as a conveyor that moves cars down an assembly line. This also makes it more likely to experience wear and tear.
For the food and beverage industry, it’s less about the cost of downtime and more about the cost of spoiled goods. Temperature monitoring equipment, for instance, is very critical. Motors are also used in mixing applications and can suffer premature wear and tear if there is contamination inside.
Omron focuses on providing easy-to-implement predictive maintenance technologies that can help manufacturers immediately start monitoring their critical equipment around the clock. Turnkey solutions make it easier to migrate from less effective maintenance strategies to predictive maintenance one.