Overcoming the Challenges Facing Motor Controllers
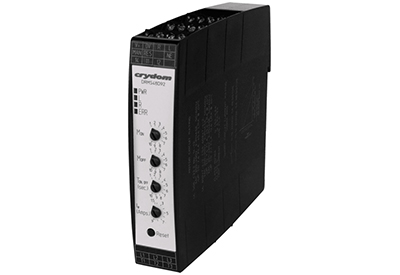
January 14, 2020
There are two types of electric motors, alternating current (AC) and direct current (DC). AC motors can be synchronous or asynchronous. Synchronous motors are found in applications where speed and accuracy are essential, including synchronous clocks, timers in electronic appliances, and audio recorders. Able to operate at variable speeds, low-maintenance, and durable, asynchronous, or induction, motors see wide industrial use. Applications such as lifting, mixing, pumping, compressing, and drilling find induction motors easy to operate and more cost-effective than synchronous and DC motors.
Of the two main types of induction (asynchronous) motors, single-phase and three-phase, the single-phase motors are usually limited to applications with small electrical loads, such as household appliances, because single-phase motors cannot self-start. Three-phase motor systems have much broader industrial and commercial use because they require less copper wiring and are therefore less expensive, smaller in size, more efficient, and run more smoothly (less vibration).
Sensata DRMS Hybrid Motor Starters offer the optimal solution for induction motors with 6 functions in the same unit including Forward/Reverse, Soft Start/Soft Stop, Motor Overload Protection, and Mains Isolating Relay.
CONTROLLERS ARE CRUCIAL
Motor systems rely on a starter, or controller, because it controls the performance of the motors by starting, stopping, forwarding, reversing, accelerating, and decelerating the motor as well as protecting it from overloads or faults.
The most basic controller is an on/off switch between the motor and the power supply, while the more complex controllers control the speed and torque of the motor.
Direct-on-line (DOL, or across-the-line) starters are the most basic type of motor starter; when energized, they immediately connect the motor terminals to the power supply. DOL starters are useful if the high inrush current of the motor does not cause excessive voltage drops in the supply circuit. They are suitable for small water pumps, compressors, fans, and conveyor belts. However, across-the-line starters cannot provide feedback.
In addition, in the case of an asynchronous motor, such as the three-phase induction motor, which draws a high starting current that is typically six to seven times that of the full load, the DOL starters will not be able to protect the motor from the inrush.
PROTECTING EQUIPMENT AND EXTENDING ITS LIFE
Motor controllers face many forms of wear and tear. In particular, three-phase induction motor starters must deal with damaging factors such as inrush current and electric arcing.
Inrush current, also known as the switch-on surge or the input surge current, is the high level of current drawn by the motor to start accelerating to full speed. During this period, the motor often needs to draw in current that is up to seven to 10 times the normal operating load. Current overloading, although lasting less than one second, will cause torque surges that cause mechanical stress on the machine, especially when the start and stop cycle is repetitive. The basic DOL starters will not be able to protect the motor from the inrush. Therefore, the controller needs to have a protective mechanism to buffer the downstream equipment adequately.
Electric arcing—where the flow of an electric current through a gas causes electrical breakdown of the gas and discharge—occurs most frequently in motor controllers where contacts repeatedly open (break) and close (make) an electrical circuit. Electric arcing produces a large amount of heat, which will melt or even vaporize small parts of the contact surface, damaging the motor controller.
In addition to dealing with inrush current and electric arcing, three-phase induction motor starters also need a soft start and stop function. Soft starts and stops prevent damaging equipment as well as the heavy and bulky objects moved by compressors, conveyor belts, and gate systems. Due to their mass, such objects have considerable momentum even at low speeds.
Soft starters and variable frequency drives can both be used to protect the equipment and extend the life of the motor by reducing inrush current and the ensuing heat generation caused by frequent starts and stops.
MAJOR TYPES OF MOTOR STARTERS
Motor soft starters, or reduced voltage solid state starters, can temporarily reduce the current load and torque surge during the start-up of a motor while smoothly ramping up the speed of the motor. As a result, the soft starter lowers the mechanical stress on the motor and shaft and lengthens the system’s life. Soft starters can be customized for individual applications. They can help avoid pressure surges in pump applications and start moving conveyor belts smoothly to aid in minimizing jerk, stress, or slip. Because soft starters have higher electrical complexity than across-the-line starters, they often incur cost-performance issues.
A variable-frequency drive (VFD) uses electromechanical drive systems to control motor speed and torque by varying motor input frequency and voltage. As a result, VFDs can reduce the current needed to start the motor. A VFD easily interfaces with automatic control systems. Variable-frequency drives are also highly energy-efficient, helping reduce peak energy demand. However, the global market penetration for VFDs is relatively small due to their high price point and sensitivity to environmental factors such as temperature and voltage surge.
While soft motor starters and variable-frequency drives already offer obvious benefits for motors, manufacturers are continuing to develop systems with greater functionality and lower price points.
HYBRID MOTOR STARTER ADVANTAGES
Sensata’s DRMS Series hybrid motor starters can provide up to six functions in the same unit: Forward/Reverse, Soft Start/Soft Stop, Motor Overload Protection, and Mains Isolating Relay.
With their soft start/stop feature, Sensata’s DRMS Series hybrid motor starters offer especially pronounced benefits to conveyor systems. In addition to their electromechanical relay feature, the DRMS Series hybrid motor starters include a solid state relay feature, which uses semiconductors for contact-free operation to achieve quick and wear-free power control.
With the performance offered by the solid state relay and the reliability of the electromechanical relay, the DRMS Series hybrid motor starters are more effective in mitigating the destructive effects of high inrush currents, the resulting mechanical stress, and the formation of gaps in the system. As a result, the combined relay features achieve higher performance and consistency, lower power consumption, better safety, and longer equipment life.
In addition, the DRMS Series hybrid motor starters are compact at only 22.5mm in width, which reduces the space requirement for a motor starter by up to 75 percent. Lastly, compared to variable-frequency drives, which cost anywhere from $400 to $1200, the DRMS devices offer a more economical option.
The DRMS Series hybrid motor starters can be used in conveyor systems, gate systems, and compressors by machine builders, panel designers or builders, and production facilities. Furthermore, these hybrid motor starters have a higher max motor rating of 400V versus other comparable products; the high max motor rating enables the use of DRMS Series hybrid motor starters in a wider range of industrial applications than other products can handle.
CONCLUSION
Motor starters for induction motors undergo many start and stop cycles. Factors to consider when comparing motor starters include performance, durability, reliability, size, price point, and protecting equipment from inrush current and other potentially damaging phenomena. Direct-on-line starters are reliable but offer little self-protection or protection for the assets the motors move. Greater protection is available with VFDs but at an expensive price point. Hybrid motor starters strike a balance between all these factors and therefore, deserve significant consideration for motors that work with valuable assets.