Omron: Top 5 ways intelligent mobile robots boost productivity in semiconductor and electronics manufacturing
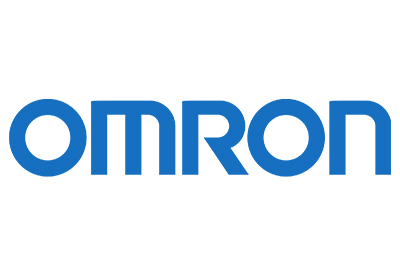
July 1, 2019
It goes without saying that materials transport in industries like consumer electronics, automotive electronics and semiconductor manufacturing can get complicated. To enable small-volume, high-mix semiconductor production, for example, wafer cassettes must be transported in complicated orders with precise timing.
Tasking human workers with these requirements is cumbersome and inefficient, but it’s also not ideal to automate the process with traditional autonomous guided vehicles (AGVs) that require costly and space-consuming factory modifications.
Enter the Omron LD Series Mobile Robot, also known as an autonomous intelligent vehicle (AIV). Capable of self-navigating through dynamic and peopled environments, these robots are the ideal solution for delicate materials transport needs. Following are some of the top reasons why AIVs are the best option for your facility.
1. AIVs save space.
Since LD mobile robots aren’t limited to travelling on specific paths within a plant, they help reduce manufacturing logistics congestion by navigating around one another much more effectively than AGVs.
AGVs typically require specific “evacuation areas” configured by magnetic tape in order to pass each other, whereas AIVs need no such thing. This means that AIVs work more effectively within narrow spaces and help to maximize space utilization.
2. AIVs cut installation costs.
Omron mobile robots can make use of an advanced localization option – known as Acuity – in addition to onboard lasers to find the best path to their destination. Acuity identifies overhead lights and overlays the “light map” with the “floor map” to enable highly accurate navigation in frequently changing environments.
With no need for factory modifications like floor magnets and navigational beacons, their implementation saves up to 15% of deployment costs compared with other transport strategies.
3. AIVs enhance traceability.
Omron’s mobile robots help improve material flow traceability because they can capture real-time data throughout the process. Each time a job is allocated to a particular robot, this event is reflected in the system, and the robot’s movement is tracked as well. This also helps customers optimize their processes and throughput.
4. AIVs optimize the workforce.
By taking care of repetitive, error-prone tasks, self-navigating robots help reduce the likelihood of mistakes while freeing up the workforce to perform activities that require human ingenuity. This reduces training requirements and helps lead to greater employee satisfaction.
AIVs also help keep semiconductor manufacturing plants free from contamination by ensuring that employees only enter the areas where their abilities are truly needed. Since contamination is major concern in the semiconductor business, the AIV solution offers major advantages.
5. AIVs improve safety.
AIVs help prevent work-related accidents such as collisions and muscle strain from heavy lifting. Maintenance of sputtering machines, for example, involves direct contact with the interior of the equipment and carries risks such as electric shocks, pinching and back strains. By automating materials transport, workers no longer needed to deal with these hazards.
Read the original article HERE