Not All Cables Perform Alike – Four Key Cable Design Considerations from Kollmorgen
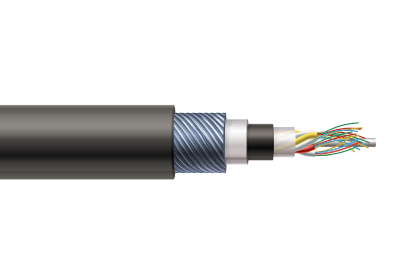
March 15, 2022
Servo systems are widely used in many precision applications. While careful deliberation on the optimum servo motor, servo drive, and feedback elements is the norm, the cables that connect the power and feedback are often an afterthought that compromises the desired system performance. The four key specifications that must be considered when choosing the right cable design for a servo system are voltage, current, shielding, and flexibility.
Voltage and Current
Since the servo motor and drive have specific voltage and current ratings, the power cable choice should match those ratings. Other factors, such as NEC regulations and other safety codes, may also dictate cable sizes and current capacity levels. Voltage ratings are determined by the insulation systems of cables as relation to the individual wires and the entire bundle. Current ratings are determined by the conductor size and influence the overall diameter of the cable.
Shielding
Shielding plays a major role in the successful operation of a precision servo system. Shielding prevents unwanted noise from being carried on feedback signals back to the drive and eliminates RFI and EMI emissions that interfere with other nearby electronic devices. Depending on the specifics of the feedback elements, twisted, shielded pairs of wires will mitigate noise issues, while the overall cable shielding can sink unwanted interference to ground. Different shielding methods are determined by the frequency of the signal carried by the cable.
Flexibility
For some applications, the most important metric for cable flexibility is bend radius, which determines the allowable bend radius for the cable. In applications where the cable always remains stationary, the flex rating is not much of a concern. In applications where the cable is constantly in motion, the flex rating is critical. Stiffer cables require a much larger bend radius than cables made of more pliable materials. Using a stiff cable in a dynamic application where the cables are constantly moving back and forth will eventually cause cable failure and possibly damage other components in the system. Linear motor applications are ideal candidates for highly flexible cable designs.
The interaction of these key elements, along with environmental factors that may add further considerations, make the choice of cable material an important design concern. Food packaging applications often require food grade cable materials, while wet or washdown applications require specific protection against fluids. Machine designers who work with Kollmorgen can better navigate the complicated motor/drive application requirements to find the most appropriate cable design for optimal performance.