Boosting Machine Performance: How Motors, Drives and PLCs Enable Success
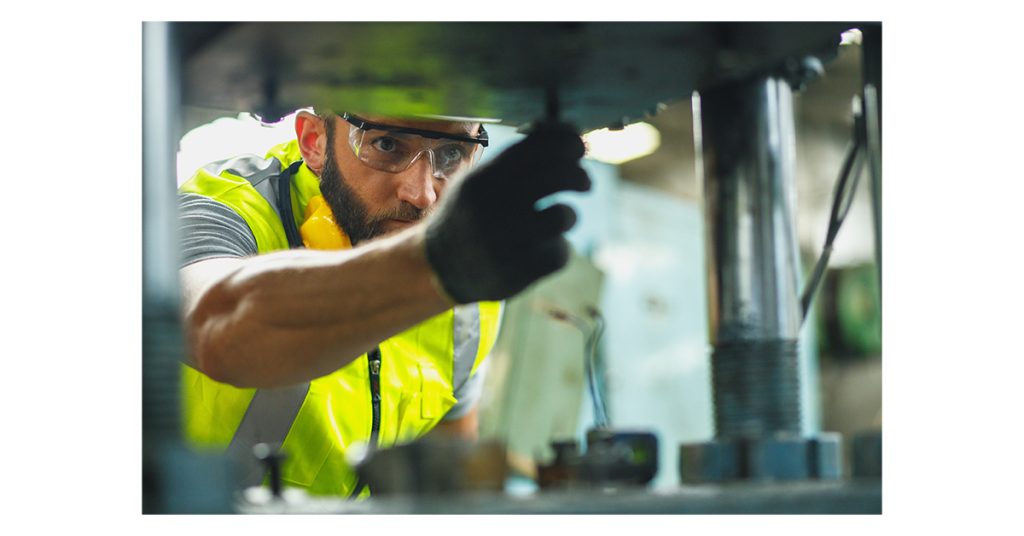
November 16, 2023
By Johann Arndt, Global Product Line Manager Automation, ABB Drives
In today’s competitive market, machine builders face pressure to deliver highly reliable, cost-effective, sustainable and energy-efficient machines. Customers also expect new equipment to be compatible with digitalization and automation technologies. The key to meeting these customer expectations is using high-quality, advanced variable speed drives (VSDs) also known as variable frequency drives (VFDs), or just drives, along with programmable logic controllers (PLCs).
Drives enable machine builders to create machines that use less electricity and complete critical processes as precisely as possible. PLCs, meanwhile, enable a range of data-driven features – including automation – which increase reliability, reduce costs, and further improve energy efficiency.
Sustainability as a top priority
Machine manufacturers and their industry customers are increasingly concerned about sustainability and reaching Net Zero emissions. The International Energy Agency (IEA) describes energy efficiency as the “first fuel” for reaching Net Zero. Machine builders therefore must develop machines that are productive and energy efficient.
By ensuring that a motor moves at precisely the correct speed for its process, motor-drive packages can achieve significant energy savings. Savings up to 25 percent or more are common in applications where the motor is not required to run continuously at full speed, such as fans or pumps.
Machine builders can also specify efficient motors. Today, the most efficient motors are IE5 synchronous reluctance motors (SynRM). Paired with a drive, SynRM motors achieve 40 percent lower electrical losses than the IE3 motors that are still in common use.
A primary concern for machine builders is lowering the total cost of ownership (TCO). The savings produced by using variable speed technology are multiplied due to today’s high energy prices – higher efficiency drastically reduces operational costs and CO2 emissions. This means that a customer’s moderate initial investment into a drive can currently be paid back within a matter of months. From then on, it represents a saving on operating expenses and emissions.
PLCs, meanwhile, can improve sustainability by reducing waste. For example, PLCs can reduce unnecessary variations in the main process parameters and improve operating efficiency by enabling better maintenance practices. Improved processes – including automation – also reduce downtime and material waste.
In addition to energy efficiency, companies must also consider material efficiency as part of a circular approach, including using recycled materials wherever possible. Additionally, product designs should undergo reliability testing and be focused on durability. Premium services and digital solutions can further extend the product lifespan. When these products eventually reach the end of their lifecycle, they should be easily recyclable, with up to 95% of the drive’s materials recoverable for use in new products. ABB aims to ensure that, by 2030, at least 80 percent of its products and solutions are compatible with a circular economy model.
Enabling smarter maintenance
Customers are also concerned with maintenance requirements. Drives enable more precise control over motor-driven equipment, limiting unnecessary wear and tear. Modern drives and PLCs also offer remote condition monitoring that provides end users with data on their driven equipment. This enables them to identify potential issues before the machine fails and perform preventative maintenance, avoiding costly unplanned downtime. Building machines using these drives creates a valuable selling point for machine builders.
Modern ABB drives and PLCs are designed with networking capabilities that embrace openness and easy integration with other technologies. This enables greater flexibility – including customization on the part of the machine builder and the end user.
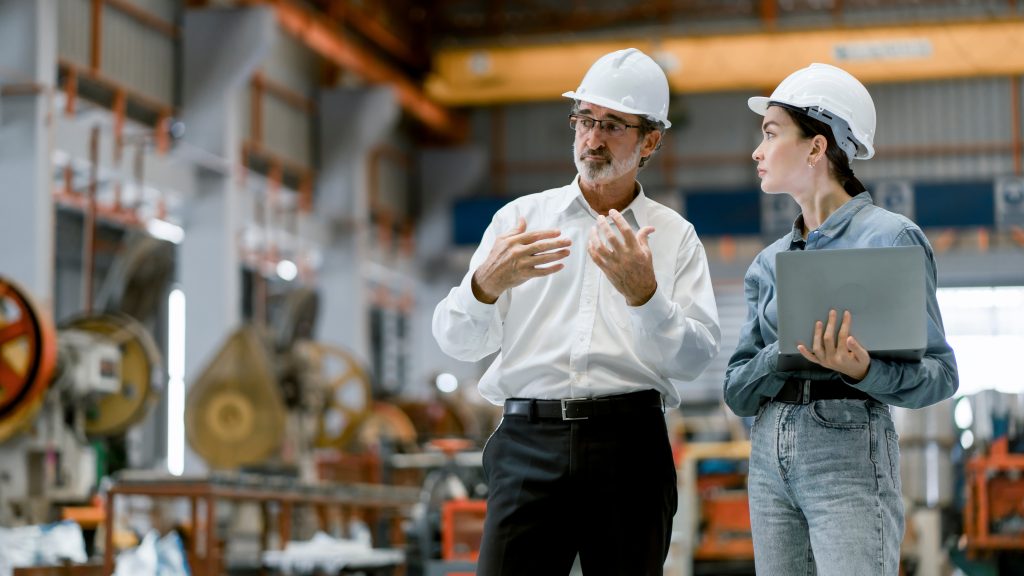
Safety first
Regulatory compliance and safety are essential. Drives and PLCs can support machine builders in constructing machines that achieve the highest standards of functional safety. There are economic advantages to integrating safety into a design, such as increased productivity and minimum downtime.
Safety functions embedded in drives begin with safe torque off (STO), which comes as standard. Additional safety functions are available, including safe stop 1 (SS1), safe stop emergency (SSE), safe brake control (SBC), safely-limited speed (SLS), safe maximum speed (SMS), prevention of unexpected start-up (POUS), safe direction (SDI) and safe speed monitor (SSM). These safety functions meet relevant legislative requirements, including European Union Machinery Directive 2006/42/EC, and they are TÜV Nord certified.
PLCs also add important safety features. ABB’s AC500-S Safety PLC, for example, enables both machine builders and end users to write and run safety-focused code in a range of formats. It contains a discrete safety CPU to ensure that the safety functions continue to run even when the non-safety hardware is inactive. Extreme conditions (XC) modules are also available for machines designed for challenging environments, such as in the marine and wind sectors.
Exceeding customer expectations
The purchasing decisions of end-user customers in the industry are influenced by various factors, including safety, energy efficiency, and sustainability. Fortunately, modern drives and PLCs enable machine builders to create machines that excel in each of these areas, while also being cost-effective and customizable. By specifying drives and PLCs with the latest technology and a broad range of built-in features, machine builders can create the best possible machines.
Learn more at new.abb.com/drives/machine-builders.