Motor Starting Methods 101: Across the Line Motor Starting Method
December 22, 2023
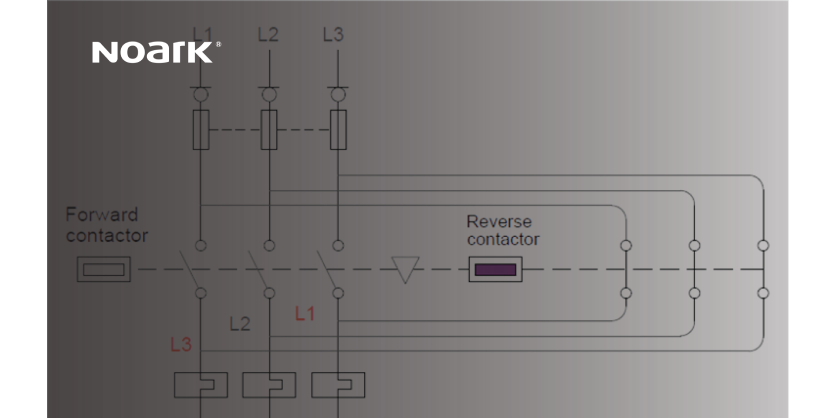
Throughout industrial manufacturing, motors play a very important role in the advancement of processes and the handling or transformation of materials from raw materials to finished products or services.
To ensure a reliable and efficient start-up of a machine, the correct starting method should be chosen to minimize stress on the motor and ensure a smooth start-up.
This article is the second installment of a four-part series designed to educate readers about the different motor starting methods and will take a comprehensive look at the various schemes associated with Across the Line Motor Starting.
What is the Across the Line Motor Starting Method?
As a common technique for starting induction motors, the “Across the Line” method is one of the most popular methods for starting motors. The windings of the motor are directly connected to the power supply at full voltage during the starting phase of the motor. While this method is straightforward and cost-effective, it may result in a high inrush current and mechanical stress on the motor.
The following is an explanation of two starting schemes associated with “Across the Line” motor starting method, namely Full Voltage Non-Reversing and Full Voltage Reversing schemes :
Full Voltage Non- Reversing Motor Starter
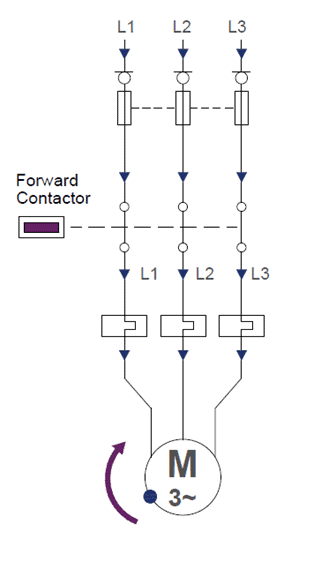
This is the most common and simple way to start the motor. The motor control in this case is achieved through the forward contactor as shown in the figure below while overcurrent protection and isolation means are achieved by the SCPD (Short circuit protection device) and overload relay. The full line voltage is applied across the motor terminals to the stator which gets the motor to rotate unidirectionally. To overcome the inertia at the start, the locked rotor current or starting current goes up to 5-6 times the FLA (full load ampere) of the motor and gradually reduces as the motor reaches its run speed.
Similarly, the starting torque of the motor increases rapidly till it gets to the maximum possible torque (breakdown torque) before settling at the full-load torque. This method of starting has the most amount of starting current compared to other starting methods and therefore demands more reactive power from the utility network. It is important to note that across the line method increases the reactive power demand in the network and the Utility provider would typically apply a penalty cost to such consumer. This starting method is particularly suitable for small and medium sized motors where the inrush current is of small order magnitude as the reactive power effect is reduced.
Full Voltage Reversing Motor Starter
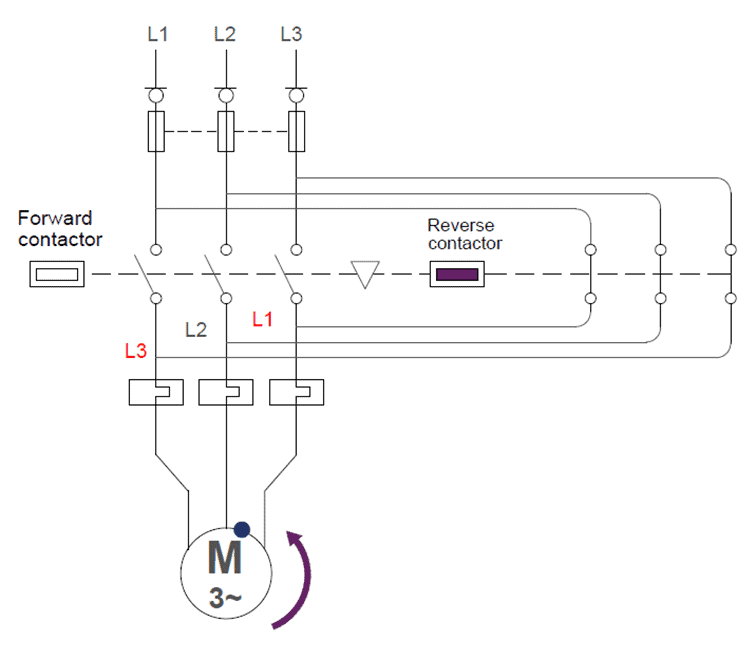
The full voltage reversing motor starting is similar to the full voltage non-reversing method as the full line voltage is also applied across the motor terminals. However, in this situation it uses two contactors which are mechanically interlocked – one applied in the forward direction of the motor and the other in the reverse direction. As shown in the figure below, the motor starts in the forward direction when the full line voltage is applied to the motor terminals and continues running while the reverse contactor is on time-delay. The mechanical and electrical interlock between the contactors ensures that only one contactor is on at any given time.
Once the reverse contactor is pulled in, it changes the direction of the rotation. By switching two of the phases in the supply line, the direction of the rotating magnetic field changes and hence the rotation in the opposite direction. The effect of inrush or starting current on the full voltage reversing starter is the same as previously stated for the full voltage non-reversing method. The components for this starting method are sized taking into account the high starting current of the motor.
Implement the Across the Line Motor Starting Method with Noark Electric
Traditionally the across line motor starting method is the most commonly used method because of the cost and simplicity. You can learn more about the pros and cons of this starting method by following this link.
At Noark, we are committed to delivering the best and most reliable products for your motor starting needs. To ensure that your motor is starting safely and efficiently, contact the Noark Electric team to find the right motor starter components for the job.
Lastly, sign up for the NoarK Newsletter to receive free monthly product updates, news and downloadables.
More Information
Related Story
Noark Electric Tech Tip: Understanding Combination Motor Controllers
Electric motors are critical components in every production process or facility because they are the movers of mechanical equipment and machinery. Without them, nothing gets done. When designing a system, it is imperative to provide protection for motors using various protection and control systems. A Combination Motor Controller (CMC) is one way to provide motor branch circuit protection and control.